Overview of all O-ring designations | Advantages and disadvantages
One thing is clear: with 12 different O-ring designations, it can be difficult to select the optimum O-ring material.
We want to make your life easier, which is why we have listed all 12 O-ring designations and their most important properties below.
Accordingly, you will find relevant information on material designation, resistance and mechanical load-bearing capacity for all materials.
Material | Temperature resistance | Chemical resistance | Elasticity |
---|---|---|---|
FFKM | -40°C to +340°C | High | High |
FEP coated | -60°C to +200°C | High | Medium |
FKM (VITON) | -25°C to +200°C | Medium | High |
PTFE | -250°C to +250°C | High | Low |
NBR | -30°C to +120°C | Low | High |
HNBR | -30°C to +150°C | Medium | High |
EPDM | -45°C to +150°C | Medium | High |
SILICONE | -60°C to +200°C | Low | High |
FVMQ | -60°C to +200°C | Medium | High |
FEPM | -10°C to +200°C | Medium | High |
CR | -40°C to +100°C | Low | High |
ACM | -20°C to +150°C | Medium | High |
REQUEST O-RINGS QUICKLY AND EASILY?
Almost any dimension available
Offer received in record time
No minimum order quantities or minimum item values
One contact for all concerns
#1 FFKM | O-RING DESIGNATIONS
Feature | Value |
---|---|
ISO designation | FFKM |
Chemical name | Perfluoro rubber |
Cross-linking | Peroxide cross-linked |
Trade names | ECOLAST |
Media resistance | Almost universal media resistance |
Temperature resistance | -40°C to +340°C (depending on mixture) |
Standard color | Black |
Standard hardness | 75 Shore A |
Industries | Chemicals, food, pharmaceuticals, oil & gas |
Manufacture | Compression molding and injection molding |
Tolerances | DIN ISO 3601 |
Durability | 13 years |
The biggest advantages of FFKM
FFKM is by far the best performing O-ring material.
This is because FFKM combines almost universal media resistance with the highest temperature resistance of -40°C to +340°C (depending on the compound).
In addition, FFKM is elastic, unlike FEP or PTFE. Accordingly, FFKM can be used for any type of application (flange, piston or rod seal).
Another advantage is that FFKM is available in a wide range of material mixtures. There are FFKM compounds for chemical engineering, the food industry (FDA), the oil and gas industry (Norsok), the semiconductor industry, low and high temperatures and much more.
Summary of advantages
+ Almost universal media resistance
+ Excellent temperature resistance
+ Can be used flexibly for any type of application
+ Variety of material mixtures
The biggest disadvantages of FFKM
The fantastic properties of FFKM have the disadvantage that the raw material price for FFKM is extremely high. As a reference value, the raw material price of FFKM is 100 times higher than that of FKM.
As a result, very few suppliers (apart from us 😉 ) stock FFKM O-rings. stock FFKM O-rings. This creates difficulties when it comes to the short-term availability of FFKM O-rings.
Important to note: FFKM must not come into contact with molten alkali metals under any circumstances. This is because toxic gases can be produced.
Summary of the disadvantages
– High price
– Low availability
– Must not come into contact with molten alkali metals
– The variety of blends can cause confusion
#2 FEP | O-RING DESIGNATIONS
Feature | Value |
---|---|
ISO designation | FEP / PFA |
Chemical name | Fluoroethylene propylene (FEP), perfluoroethylene propylene (PFA) |
Cross-linking | Core-dependent: Silicone = sulphur, FKM = bisphenol |
Trade names | Teflex |
Media resistance | Almost universal media resistance |
Temperature resistance | Depending on the core material |
Standard color | Black |
Standard hardness | 90 Shore A |
Industries | Chemistry, oil & gas, high temperature |
Production | Durable plastic cover + elastic rubber core |
Tolerances | |
Durability | 20 years |
The biggest advantages of FEP
FEP is a plastic that is used to encase O-rings.
Accordingly, the finished O-ring is a combination product consisting of the seamless FEP coating and the elastic core material. FKM (black) or silicone (red) are typically used for the core material.
This means that the almost universal media resistance of FEP is combined with the elasticity of rubber. In addition, the FEP coating complies with FDA requirements and Directive EC 1935/2004, meaning that FEP O-rings can be used in the food and pharmaceutical industries.
Another advantage is that FEP O-rings can be produced in almost any size and in any quantity. As a reference value: Our largest FEP O-ring to date had an inner diameter of just under 5 meters.
Summary of advantages
+ Almost universal media resistance
+ Partially elastic due to the rubber core
+ FDA and EC 1935/2004 compliant
+ Can be produced in any dimension
The biggest disadvantages of FEP
A FEP coated O-ring is a combination product and this results in disadvantages.
With no other O-ring material are there such serious differences in quality as with FEP-coated O-rings. You can recognize good quality by the fact that there is little air between the core and the casing and that the ring is clean and, above all, seamlessly welded.
In addition, the FEP sheathing must not be damaged. Accordingly, FEP O-rings should not be used for heavy abrasion loads or dynamic applications.
Another disadvantage is that FEP O-rings should only be used as flange or rod seals due to their partial elasticity. This is because FEP O-rings must not be stretched by more than 3% during assembly. (Tip: place FEP O-rings in hot water before fitting)
Summary of the disadvantages
– Serious differences in quality
– Must not be used in abrasion or dynamic applications
– Can only be used as a flange or rod seal
– May only be stretched up to 3% during assembly
#3 FKM | O-RING DESIGNATIONS
Feature | Value |
---|---|
ISO designation | FKM |
Chemical name | Fluororubber |
Cross-linking | Bisphenol cross-linked |
Trade names | FPM, VITON |
Media resistance | Excellent media resistance |
Temperature resistance | -20°C to +200°C |
Standard color | Black |
Standard hardness | 75 Shore A |
Industries | Chemistry, oil & gas, vacuum |
Production | Compression molding and injection molding |
Tolerances | DIN ISO 3601 |
Durability | 10 years |
The biggest advantages of FKM
FKM is a real all-rounder among the O-ring materials.
This is because FKM has good media resistance and at the same time good temperature resistance from -25°C to +200°C.
There are also a large number of FKM compounds. This is because FKM compounds are available in various Shore hardnesses, colors and approvals (e.g. FDA or BAM). FKM compounds for low-temperature (-40°C) or high-temperature applications (+225°C) are also available.
With these outstanding properties, FKM has an excellent price-performance ratio.
Summary of advantages
+ Good media resistance
+ Wide temperature range
+ Variety of blends
+ Excellent price-performance ratio
The biggest disadvantages of FKM
In fact FKM does not have any serious disadvantages.
Of course, the FFKM is superior to the FKM in every respect, but the FKM is significantly cheaper. If no extreme requirements make it necessary to choose an FFKM O-ring, then an FKM O-ring is an excellent alternative.
A small minus point is that the cold flexibility is rather low compared to other O-ring materials. However, FKM is available in LT compounds (LT = low-temperature) that are resistant down to -40°C.
Otherwise, a real classic is the confusion regarding the ISO designation. To help you avoid falling into this trap in future, we have briefly explained the term:
FKM is currently the official name for fluororubber.
FPM is an obsolete term for fluororubber.
VITON is FKM and only a trademark of the DuPont company.
Summary of the disadvantages
– FKM has hardly any serious disadvantages
– Low flexibility at low temperatures
– Comprehension problems with the designation (FKM, FPM, VITON)
#4 PTFE | O-RING DESIGNATIONS
Feature | Value |
---|---|
ISO designation | PTFE |
Chemical name | Polyetrafluoroethylene |
Cross-linking | None |
Trade names | Teflon |
Media resistance | Almost universal media resistance |
Temperature resistance | -250°C to +250°C |
Standard color | White |
Standard hardness | 60 Shore D |
Industries | Chemicals, food, pharmaceuticals |
Production | Machining process |
Tolerances | DIN ISO 3601 |
Durability | 20 years |
The biggest advantages of PTFE
PTFE is almost universally resistant to media and also complies with FDA guidelines. PTFE also has an extremely wide temperature range from -250°C to +250°C.
PTFE is also known for its excellent coefficient of friction, making it perfect for dynamic applications.
Another advantage of PTFE O-rings is that they can be manufactured in any size.
Summary of advantages
+ Almost universal media resistance
+ Extremely wide temperature range
+ Optimal for dynamic applications
+ Available in any dimension
The biggest disadvantages of PTFE
In contrast to all other O-ring materials, PTFE is PTFE is not an elastomer, but a thermoplastic. This results in a high degree of hardness of 60 Shore D (approx. 100 Shore A) for PTFE O-rings.
Due to their high hardness, PTFE O-rings cannot be expanded and can therefore only be used as flange gaskets. It should be noted that PTFE O-rings deform plastically during compression. Accordingly, they can only be pressed once.
This also means that PTFE O-rings must be stored more carefully, as they can otherwise lose their round shape over time.
Summary of disadvantages
– Cannot be expanded
– Plastic deformation during pressing
– More careful storage necessary
#5 NBR |O-RING DESIGNATIONS
Feature | Value |
---|---|
ISO designation | NBR |
Chemical name | Nitrile butadiene rubber |
Cross-linking | Sulphur cross-linked |
Trade names | Perbunan |
Media resistance | Medium media resistance |
Temperature resistance | -30°C to +120°C |
Standard color | Black |
Standard hardness | 70 Shore A |
Industries | Oil&Gas, Automotive industry |
Production | Compression molding and injection molding |
Tolerances | DIN ISO 3601 |
Durability | 6 years |
The biggest advantages of NBR
NBR is probably the best-known O-ring material and is therefore the most commonly used.
A major advantage of NBR is that it can be produced in large quantities due to its very low price.
NBR also has good resistance to oils and fuels and is mechanically resilient. Against this background, it is not surprising that NBR is particularly popular in the automotive industry.
But NBR is also interesting for vacuum applications. In addition to FFKM and FKM, NBR also has a comparatively low gas permeability.
Summary of advantages
+ Very low price
+ Good oil and fuel resistance
+ Good mechanical load capacity
+ Low gas permeability
The biggest disadvantages of NBR
The biggest disadvantage of NBR O-rings is their low resistance to temperature, ozone, weathering and a large number of chemicals.
Accordingly, it is particularly important when designing NBR O-rings to check whether NBR will withstand the requirements of the application.
Furthermore, NBR O-rings must be stored in a dark and airtight place. This is because the shelf life for NBR O-rings is only 6 years, and inappropriate storage reduces the shelf life even further.
Summary of disadvantages
– Low temperature resistance
– Not resistant to ozone and weathering
– Low durability
– Low media resistance
#6 HNBR | O-RING DESIGNATIONS
Feature | Value |
---|---|
ISO designation | HNBR |
Chemical name | Hydrogenated nitrile butadiene rubber |
Cross-linking | Peroxide cross-linked |
Trade names | None |
Media resistance | Good media resistance |
Temperature resistance | -30°C to +150°C |
Standard color | Black |
Standard hardness | 70 Shore A |
Industries | Oil&Gas, Automotive industry |
Production | Compression molding and injection molding |
Tolerances | DIN ISO 3601 |
Durability | 8 years |
The biggest advantages of HNBR
HNBR is hydrogenated NBR and therefore very comparable in its properties.
However, compared to NBR, HNBR has a higher temperature resistance (-30°C to +150°C) and a higher resistance to chemicals.
In addition, HNBR is peroxide crosslinked and NBR is sulphur crosslinked. This is not a difference in quality, but there are some applications where sulphur must not be present in the O-ring mixture.
Furthermore, HNBR is more resistant to ozone and weathering and also has a longer shelf life of 8 years.
Summary of advantages
+ Higher temperature resistance than NBR
+ Higher media resistance than NBR
+ Peroxide crosslinking
+ Longer durability than NBR
The biggest disadvantages of HNBR
The biggest disadvantage of HNBR is its poor availability. This is because very few dimensions are available from stock and therefore have to be produced when required.
Basically, if there is little raw material available for O-rings, for example, and it only has to be mixed when required, this has a negative effect on the price. Accordingly, HNBR O-rings have a comparatively high price in relation to their properties.
This means that in most cases it makes sense to use FKM instead of HNBR. This is because there are very few chemicals to which HNBR but not FKM is resistant.
Summary of disadvantages
– Low availability
– Mediocre price-performance ratio
– FKM is often the better choice
#7 EPDM | O-RING DESIGNATIONS
Feature | Value |
---|---|
ISO designation | EPDM |
Chemical name | Ethylene propylene diene rubber |
Cross-linking | Sulphur or peroxide cross-linked |
Trade names | Buna, Vistalon |
Media resistance | Good media resistance |
Temperature resistance | -45°C to +120°C |
Standard color | Black |
Standard hardness | 70 Shore A |
Industries | Chemistry, water&steam, food |
Production | Compression molding and injection molding |
Tolerances | DIN ISO 3601 |
Durability | 8 years |
The biggest advantages of EPDM
EPDM is an interesting and versatile O-ring material.
The greatest advantage of EPDM is its resistance to a wide range of chemicals and its resistance to the aggressive cleaning processes CIP (Clean in Place) and SIP (Sterilization in Place). Accordingly, EPDM is particularly popular in the chemical, food and pharmaceutical industries.
EPDM also has excellent resistance to hot water and steam up to +170°C. As a reference value: FKM is only resistant up to +120°C with steam.
Another advantage is that EPDM has good low-temperature flexibility and can be used down to -50°C.
Summary of advantages
+ Excellent media resistance
+ Hot water and steam resistant up to +170°C
+ Cold flexibility down to -50°C
+ Blends with FDA, USP Class and 3-A Sanitary approvals available
The biggest disadvantages of EPDM
The biggest disadvantage of EPDM is its lack of resistance to oils and greases. If an EPDM O-ring comes into contact with oil or grease, the O-ring becomes saturated and increases significantly in volume.
As a result, the O-ring will lose its feel and surface structure and the sealing effect will fail sooner or later.
Another disadvantage is that EPDM is only resistant up to +120°C (peroxide cross-linked = +150°C). As a reference value: FKM or silicone are permanently resistant up to +200°C.
Summary of disadvantages
– Not resistant to oils and greases
– Below-average temperature resistance
#8 VMQ | O-RING DESIGNATIONS
Feature | Value |
---|---|
ISO designation | VMQ |
Chemical name | Silicone rubber |
Cross-linking | Peroxide cross-linked |
Trade names | Silicone, Silicone |
Media resistance | Medium media resistance |
Temperature resistance | -60°C to +200°C |
Standard color | Red |
Standard hardness | 70 Shore A |
Industries | Food industry, gas/water installation |
Production | Compression molding and injection molding |
Tolerances | DIN ISO 3601 |
Durability | 10 years |
The biggest advantages of VMQ
VMQ (silicone) is very frequently used in industry.
This is partly because silicone is comparatively inexpensive and partly because silicone has attractive properties for most branches of industry.
For example, silicone has high elasticity, outstanding flexibility at low temperatures down to -60°C, excellent weather resistance and basic compliance with FDA guidelines.
Accordingly, silicone is used in particular in the food industry, the pharmaceutical industry and in plant engineering.
Summary of advantages
+ High elasticity
+ Excellent low-temperature flexibility down to -60°C
+ Excellent weather resistance
+ FDA-compliant in principle
The biggest disadvantages of VMQ
The biggest disadvantage of silicone is its comparatively low media resistance. Silicone O-rings fail after only a short time when exposed to a variety of chemicals.
Furthermore, the mechanical strength of silicone is low. Although the elongation at break is high, the tensile strength is very low. This means that silicone O-rings can be stretched widely, but only with a small amount of force.
Another disadvantage is that silicone has a high coefficient of friction and is therefore not suitable for dynamic applications.
Summary of disadvantages
– Low media resistance
– Low tear resistance
– High coefficient of friction
– Not suitable for dynamic applications
#9 FVMQ | O-RING DESIGNATIONS
Feature | Value |
---|---|
ISO designation | FVMQ |
Chemical name | Fluorosilicone rubber |
Cross-linking | Peroxide cross-linked |
Trade names | None |
Media resistance | Good media resistance |
Temperature resistance | -60°C to +200°C |
Standard color | Blue |
Standard hardness | 70 Shore A |
Industries | Oil&Gas, Automotive industry |
Production | Compression molding and injection molding |
Tolerances | DIN ISO 3601 |
Durability | 10 years |
The biggest advantages of FVMQ
FVMQ is a fluorinated VMQ. In other words, fluorosilicone (FVMQ) combines silicone (VMQ) with fluorine (F).
This combination results in FVMQ, a material that has all the advantages of silicone and the excellent media resistance of fluorine.
Thanks to the fluorine, FVMQ is even resistant to oils and fuels and is therefore popular in the automotive and oil and gas industries.
Summary of advantages
+ Excellent media resistance
+ Can be used in the automotive and oil and gas industries
+ Excellent low-temperature flexibility down to -60°C
+ FDA-compliant in principle
The biggest disadvantages of FVMQ
For FVMQ there are only a few areas of application where its use would make sense.
FVMQ is mainly used only where high resistance to oils and fuels is combined with very low temperatures of down to -60°C.
Accordingly, the availability of FVMQ is very low and FVMQ O-rings are rarely available from stock. As a result, FVMQ O-rings are almost always new productions, which has a negative impact on the price.
Summary of disadvantages
– Low availability
– Comparatively high price
– Only a few sensible applications
#10 FEPM | O-RING DESIGNATIONS
Feature | Value |
---|---|
ISO designation | FEPM |
Chemical name | Tetrafluoroethylene rubber |
Cross-linking | Peroxide cross-linked |
Trade names | AFLAS |
Media resistance | Good media resistance |
Temperature resistance | -10°C to +200°C |
Standard color | Black |
Standard hardness | 75 Shore A |
Industries | Oil&Gas, Automotive industry |
Production | Compression molding and injection molding |
Tolerances | DIN ISO 3601 |
Durability | 10 years |
The biggest advantages of FEPM
FEPM is comparable to FKM in its basic properties.
The biggest advantage of FEPM is its excellent resistance to a wide range of chemicals.
FEPM also has outstanding mechanical properties and excellent weather resistance.
Another advantage of FEPM is that the material has very good paint resistance.
Summary of advantages
+ Excellent media resistance
+ Outstanding mechanical properties
+ Excellent weather resistance
+ Very good paint resistance
The biggest disadvantages of FEPM
The biggest disadvantage of FEPM is the low availability and the associated comparatively high price.
In most applications, FKM is a better choice. This is because most O-ring dimensions in FKM are available from stock and are also significantly cheaper.
Another disadvantage is the low cold flexibility of -10°C.
Summary of disadvantages
– Low availability
– Comparatively high price
– Low cold flexibility of -10°C
#11 CR | O-RING DESIGNATIONS
Feature | Value |
---|---|
ISO designation | CR |
Chemical name | Chloroprene rubber |
Cross-linking | Sulphur cross-linked |
Trade names | Neoprene |
Media resistance | Medium media resistance |
Temperature resistance | -40°C to +100°C |
Standard color | Black |
Standard hardness | 70 Shore A |
Industries | Oil&Gas, Automotive industry |
Production | Compression molding and injection molding |
Tolerances | DIN ISO 3601 |
Durability | 16 years |
The biggest advantages of CR
CR (Neoprene) is comparatively rarely selected as an O-ring material.
However, there are some applications where the use of CR makes sense. This is because CR has excellent resistance to a wide range of refrigerants.
In addition, CR has excellent mechanical resistance and can therefore be used as a dynamic seal.
CR is mainly used in air conditioning and refrigeration technology and in the shipping industry.
Summary of benefits
+ Excellent resistance to refrigerants
+ Excellent mechanical resistance
+ Suitable for dynamic applications
+ High cold flexibility down to -40°C
The biggest disadvantages of CR
The biggest disadvantage of CR is the low availability and the associated comparatively high price.
Overall, there are only a few applications where it makes sense to use CR. This is because CR has only a low temperature resistance on the one hand and only average media resistance on the other.
At 6 years, the service life of CR O-rings is also rather short.
Summary of disadvantages
– Low availability
– Comparatively high price
– Low temperature resistance from -40°C to +100°C
– Short shelf life of 6 years
#12 ACM | O-RING DESIGNATIONS
Feature | Value |
---|---|
ISO designation | ACM |
Chemical name | Acrylic rubber |
Cross-linking | Sulphur cross-linked |
Trade names | None |
Media resistance | Good media resistance |
Temperature resistance | -20°C to +150°C |
Standard color | Black |
Standard hardness | 70 Shore A |
Industries | Oil&Gas, Automotive industry |
Production | Compression molding and injection molding |
Tolerances | DIN ISO 3601 |
Durability | 10 years |
The biggest advantages of ACM
ACM is a material that was developed for the automotive industry.
This is because ACM has excellent resistance to heating oil and lubricants. In addition, ACM has excellent resistance to ozone and hot air.
Another advantage is that ACM has low gas permeability, which is why ACM is also used in vacuum applications.
Summary of benefits
+ Excellent resistance to heating oil and lubricants
+ Excellent resistance to ozone and hot air
+ Low gas permeability
+ Can be used for vacuum applications
The biggest disadvantages of ACM
ACM is the least in demand in the world of O-rings.
This is mainly due to the fact that fluorine materials such as FKM, FEPM or FFKM have gradually replaced the ACM material.
There are now only a few car manufacturers that still use ACM for their production.
As a result, ACM O-rings are hardly ever stock items, resulting in comparatively high costs for new production.
Summary of disadvantages
– Low availability
– Comparatively high price
– Fluorine materials are often the better choice
– Average temperature resistance
“I am convinced that we should share our knowledge with the world. I hope I have been able to answer all your questions. If you have any further questions, please feel free to contact us at any time. We will be happy to help you.”
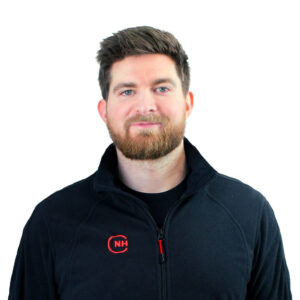
Lord of the O-rings
Author of the sealing academy