FEP O-RINGS | MATERIALS SIMPLY EXPLAINED
What are FEP O-rings?
FEP O-rings consist of a plastic coating and a rubber core.
The plastic sheath is made of FEP or the slightly higher quality PFA and the rubber core is made of black FKM (Viton) or red silicone (VMQ) . The combination of highly resistant plastic jacket and flexible rubber core makes FEP or PFA O-rings an excellent choice for aggressive media and high temperatures.
In the article description, the sheath is always stated first and then the rubber core.
Example: 10 x 2 FEP/FKM (FEP sheath with black FKM core)
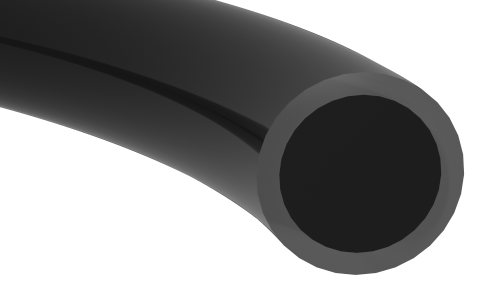
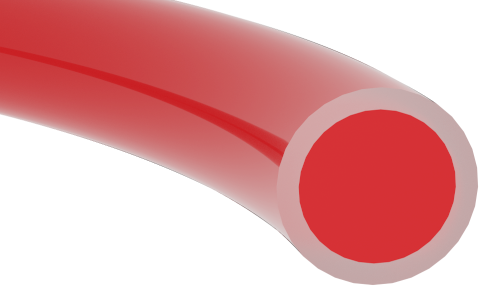
Feature | Value |
---|---|
ISO designation | FEP / PFA |
Trade names | Teflex |
Chemical name | Fluoroethylene propylene (FEP), perfluoroethylene propylene (PFA) |
Media resistance | Almost universal media resistance |
Temperature resistance | -60°C to +205°C (depending on core material) |
Standard color | Black |
Standard hardness | 90 Shore A |
Industries | Chemistry, oil & gas, high temperature |
Production | Durable plastic cover + elastic rubber core |
Tolerances | |
Durability | 20 years |
REQUEST FEP O-RINGS QUICKLY AND EASILY?
Almost any dimension available
Possible core materials: FKM (Viton), silicone and EPDM
Offer received in record time
No minimum order values or minimum quantities
#1 The 5 most important advantages of FEP O-rings
1. Almost universal media resistance
2. High temperature resistance
3. Long shelf life
4. Almost any dimension available
5. Cost-effective alternative to FFKM O-rings
An O-ring with elastic properties and a uniformly shaped surface that can withstand almost all media and temperatures, even at high temperatures. This is the ideal sealing element for demanding applications.
FEP O-rings come very close to this target image. Here, FEP forms the resistant sheath, while an elastic core (e.g. FKM (Viton) or silicone) provides the resilience and uniform contact pressure of the sealing ring.
In this way, a low compression set can be achieved with FEP-coated O-rings. The low coefficient of friction also makes assembly easier.
A comparison of the most important O-ring materials
Material | Temperature resistance | Chemical resistance | Elasticity |
---|---|---|---|
NBR | -30°C to +120°C | Low | High |
HNBR | -30°C to +150°C | Medium | High |
EPDM | -45°C to +150°C | Medium | High |
SILICONE | -60°C to +200°C | Low | High |
FKM (VITON) | -25°C to +200°C | Medium | High |
FEP coated | -60°C to +200°C | High | Medium |
PTFE | -250°C to +250°C | High | Low |
FFKM | -40°C to +340°C | High | High |
#2 The 3 most common areas of application for FEP O-rings
Chemical industry
O-rings in the chemical industry are generally selected according to their media resistance.
As highly aggressive chemicals are used in the chemical industry, which can even degrade O-rings with low resistance, FEP O-rings are therefore often used for demanding applications.
In terms of media resistance, the only other options are FFKM (Ecolast®) and PTFE can keep up with the FEP O-rings.
Oil and gas industry
The special features of applications in the gas industry are the extreme system pressures on the one hand and the high temperatures on the other.
FEP O-rings are well equipped against these two factors. This is because they have a comparatively high Shore hardness of 85-90° Shore A and can easily withstand temperatures of up to +200°C.
Furthermore, the higher-quality PFA sheathing can be used at temperatures above 200°C. This can even withstand temperatures up to +260°.
Food industry
In the biomedical and food industries, biocompatibility is an indispensable property of sealing materials.
It is therefore extremely practical that all FEP and PFA sheaths comply with FDA guidelines (food approval). In addition, all FEP O-rings with silicone or EPDM cores also have FDA approval.
This ensures that food or pharmaceutical products cannot be contaminated by the O-rings.
#3 What is the media resistance of FEP O-rings?
FEP and PFA sheathing are highly resistant to almost all chemicals.
FEP is resistant to
- Mineral oils and greases
- Vegetable and animal oils and fats
- Aliphatic and aromatic hydrocarbons
- Fuels (diesel, gasoline, fuels containing methanol)
- Chlorinated hydrocarbons
- Silicone oils and lubricants
FEP is not resistant to
- Highly fluorinated substances
- Alkalis
Alternatively, only FFKM or PTFE O-rings come close to this comprehensive media resistance. However, PTFE O-rings are rigid due to their hardness and FFKM O-rings are elastic but extremely cost-intensive.
Accordingly, FEP O-rings are a wonderful alternative to PTFE or FFKM O-rings and have rightly taken on an important role in the O-ring world.
Another advantage is that FEP O-rings are resistant to both assembly greases based on mineral oil and silicone oil. As a result, any fat or oil can be used.
#4 What is the temperature resistance of FEP O-rings?
It is important to know that the temperature resistance depends on the choice of sheathing and core material.
FEP/silicone: -60°C to +205°C
FEP/FKM: -25°C to +205°C
PFA/silicone: -60°C to +260°C
PFA/FKM: -25°C to +260°C
However, it should always be noted that the specified temperature limits depend on the respective contact medium are dependent. If nothing is stated, air is always assumed to be the medium.
Just like FFKM O-rings FEP O-rings can be used in applications with superheated steam. Particularly interesting for applications in the hygiene industry, where production lines are cleaned and sterilized during aggressive CIP processes.
#5 What are the mechanical properties of FEP O-rings?
1. FEP O-rings should not be subjected to dynamic loads
2. No abrasive (rubbing) medium
3. No high expansion during assembly
As a general rule, the FEP sheathing must not be damaged under any circumstances.
This is because the media resistance is provided by the plastic jacket. If this is damaged to such an extent that an aggressive medium can attack the FKM or silicone core, the FEP O-ring will fail after a short time.
Accordingly, FEP O-rings should not be used with abrasive (rubbing) media on the one hand and with dynamic applications be used. In both cases, the risk of the FEP coating being damaged and the O-ring failing is too high.
In addition, FEP O-rings must not be stretched too far during installation, otherwise the sheath may be damaged.
#6 What do I need to consider when designing an FEP O-ring?
1. They have higher manufacturing tolerances than standard O-rings according ISO 3601
2. They should not be used as piston seal and rod seals
3. There must be no sharp edges, especially with FEP O-rings
Correct installation is crucial to ensuring that the careful design of the entire sealing system pays off in the form of a long service life.
This is because the O-ring is often pre-damaged during installation, which reduces its service life. However, the correct design of the installation space also determines the performance of the sealing system.
As a general rule: Due to the lack of elasticity of the jacket, FEP-coated O-rings should only be deformed very carefully. Compared to elastomer O-rings, they can be stretched and compressed to a limited extent.
Designers can make it much easier to replace an FEP-coated O-ring if they provide axially accessible installation spaces. Split grooves are therefore preferable. If this is not possible, the fitter should always use an installation cone. This ensures even and controlled stretching.
Professional tip: It helps to temper the O-ring in hot water for a few minutes before fitting.
All components involved must be burr-free. As with all sealing elements, the production of dirt-free surfaces is essential preparation for assembly. The technician should also check for deformation.
#7 Further important information on FEP O-rings
Finally, we would like to answer a few questions that we are frequently asked in everyday life.
#7.1 What is a unique quality feature of FEP O-rings?
In order for them to function reliably, inserts overmolded with FEP or PFA require particularly controlled manufacturing conditions.
As these are hybrid components in which the material properties of the core and shell differ significantly, the tight bond between the two materials is particularly important.
The industry is therefore constantly working to minimize air pockets between the core and shell during the injection moulding process. In order to achieve an optimum material bond, the injection molding machines work under vacuum conditions.
#7.2 What kind of material is FEP?
FEP (tetrafluoroethylene-hexafluoropropylene copolymer) is a thermoplastic fluoropolymer.
Just like the best-known representative of the fluoropolymer group, PTFE (polytetrafluoroethylene), FEP also gets its outstanding media resistance from the multiple carbon-fluorine compounds.
Fluorine replaces all or at least some of the hydrogen bonds on the carbon skeleton of the molecules. This also increases the temperature resistance of these materials. PFA (perfluoroalkoxy polymers) are fully fluorinated plastics which, like FEP, can also be processed thermoplastically.
In terms of their media resistance, all 3 materials are suitable as a cover for an O-ring with an elastomer core.
#7.3 Is FEP Teflon?
No, FEP is not Teflon. Teflon is a trade name and stands for the PTFE material.
FEP and PTFE are very similar in terms of their properties, but there is one major difference: while PTFE can only be sintered, FEP and PFA can be manufactured using the hot forming process (e.g. injection molding).
Basically, the thermoplastic properties of FEP and PFA make it possible for us to seamlessly coat elastomer cores (FKM and silicone) with FEP or PFA.
#7.4 What does FEP mean?
FEP (tetrafluoroethylene-hexafluoropropylene copolymer) is a thermoplastic fluoropolymer.
It can be used in the injection moulding process as a coating for elastomer O-rings to optimize the temperature and media resistance of the O-ring.
#7.5 What possible combinations of sheathing and core are there?
FEP/silicone: -60°C to +205°C
FEP/FKM: -25°C to +205°C
FEP/EPDM: -40°C to +150°C
PFA/Silicone: -60°C to +260°C
PFA/FKM: -25°C to +260°C
Note: The rubber core can also be manufactured as a hollow version for applications with a low compression capability.
“I am convinced that we should share our knowledge with the world. I hope I have been able to answer all your questions. If you have any further questions, please feel free to contact us at any time. We will be happy to help you.”
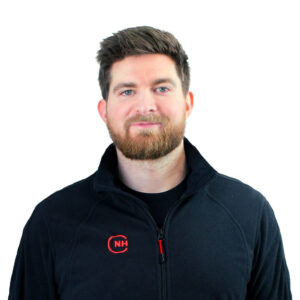
Lord of the O-rings
Author of the sealing academy