O-RING DESIGN | DESIGN SIMPLY EXPLAINED
The optimum O-ring design
During the design phase, the course is set for a permanently reliable seal with O-rings.
What is neglected here has an impact during the operating phase of the technical systems and devices in the form of high maintenance costs or, in the worst case, unplanned malfunctions.
This means that high follow-up costs are inevitable. Designers can avoid this by taking all the operating conditions into account during the design phase.
By defining the dimensions, selecting the material and designing the groove, they find the optimum balance between cost and sealing performance.
REQUEST O-RINGS QUICKLY AND EASILY?
Almost any dimension available
Offer received in record time
No minimum order quantities or minimum item values
One contact for all concerns
#1 Functional principle of pressing
The functionality of O-ring seals is all about the compression of the sealing element between the contact surfaces.
This compensates for unevenness in the surfaces and eccentric positioning. In general, the target value for the deformation of the O-ring between the sealing surfaces is 20 percent of the cord thickness.
The appropriate depth and width of the groove ensures that the O-ring securely seals the sealing point even if it shrinks due to the effects of media or if the workpiece tolerances at certain points are unfavorable.
At the same time, the seal is robust against pressure-induced movement of the O-ring.
#2 O-ring tables as a guide for the choice of dimension
Cord thickness and diameter are the two determining characteristics for the dimensions of O-rings.
Together with the depth of the installation groove this results in the compression in the installed state. The use of standardized O-rings has decisive advantages:
- Standardized O-rings have the best availability
- Customers can refer to standardized tolerances of the finished parts
- Tables specify the installation spaces for standard-compliant O-rings
The use of the standards list from ISO 3601 has become the global and cross-industry standard for O-rings.
It links tables for the dimensions of O-rings with the suitable installation spaces for various applications. This enables designers to determine the optimum O-ring dimension for a given installation space, but also to draw conclusions about the required installation space from the O-ring.
All with the aim of keeping the compression of the sealing element within the target range.
#3 Temperatures and media determine the choice of material
Every elastomer has its ideal temperature range. Within this, the service life is at a high level because the material properties relevant to the seal remain stable.
Particularly high or low temperatures must be taken into account when designing the O-ring, as these can have a negative effect on the sealing effect. sealing effect of an O-ring.
To control these effects, the lower and upper temperature application limits must be taken into account in the design.
Temperature too high
Excessive heat causes O-rings to lose their elasticity permanently. The ageing process usually begins with a strong expansion of the sealing element.
The increased compression results in significantly greater friction, especially in dynamic applications. This mechanical load can in turn cause the O-ring to lose material.
When cold, this material is then missing in order to ensure the necessary minimum level of compression. When cooling down after excessive heat, the O-rings do not fully return to their original shape.
There is also the effect of post-vulcanization at high temperatures. Additional bonds are formed between the molecules, which permanently disrupt the flexible behavior of the O-ring.
Temperature too low
Below the material-specific glass transition temperature, the O-rings lose their elasticity and mechanical strength.
However, this process is reversible, so that the properties return when the temperature load decreases. Nevertheless, there is a risk that the seal will fail at low temperatures.
If, for example, particularly high pressure peaks or external impacts on the sealing system occur during temperature exposure, the O-ring cannot sufficiently bridge the changed sealing gap.
The temperature resistance of O-rings can only be assessed in connection with the relevant media.
The general temperature range of FKM between -25 and +200 °C. However, air as the ambient medium is decisive for this specification. If an EPDM O-ring is exposed to hot water instead, its durability drops significantly from 120 °C.
Media can affect sealing materials in two ways and thus disrupt their original function:
- Physical change: Media penetrate the sealing material or dissolve out compound components such as plasticizers. These processes change the volume of the O-ring. Shrinkage can reduce the compression to such an extent that leaks occur. If the O-ring swells, mechanical properties such as hardness or tear resistance change.
- Chemical change: The chemical influence of media relates to the bonds of the polymers. They are what give the O-ring its good sealing properties in its initial state. Aggressive media break these polymer chains, causing the O-ring to become hard and brittle.
Material | Temperature resistance | Chemical resistance | Elasticity |
---|---|---|---|
FFKM | -40°C to +340°C | High | High |
FEP coated | -60°C to +200°C | High | Medium |
FKM (VITON) | -25°C to +200°C | Medium | High |
PTFE | -250°C to +250°C | High | Low |
NBR | -30°C to +120°C | Low | High |
HNBR | -30°C to +150°C | Medium | High |
EPDM | -45°C to +150°C | Medium | High |
SILICONE | -60°C to +200°C | Low | High |
FVMQ | -60°C to +200°C | Medium | High |
FEPM | -10°C to +200°C | Medium | High |
CR | -40°C to +100°C | Low | High |
ACM | -20°C to +150°C | Medium | High |
#4 The most important O-ring materials and their application profile
Different operating temperatures and media limit the field of suitable sealing materials during the design phase. These are the most common O-ring materials and their suitability for various applications.
In addition to the general suitability profiles, even more detailed key areas of application can be derived for practical use:
FFKM:
Solvents, strong acids and alkalis
FFKM currently offers the best performance spectrum of all sealing materials. With a wide temperature range with +340 °C as the upper limit and almost complete chemical resistance, this high-quality material can be used universally.
FKM:
Acids and alkalis
In contrast to FFKM, the bonds of FKM are not fully saturated with fluorine. Nevertheless, the fluoropolymer offers temperature properties and media resistance at a very high level.
EPDM:
Hot water applications
This O-ring material is particularly stable in air and hot water applications. Both the volume and the mechanical properties hardly change up to 200 °C (at water).
Silicone:
Food products
Silicone O-rings offer very good low-temperature flexibility, but are only suitable for static use due to their low abrasion resistance. Due to its odorless and tasteless properties, the material is physiologically ideal for food applications.
NBR
Oils and natural gases
The acrylonitrile content gives NBR excellent resistance to petroleum-based products such as gasoline, diesel and heating oil. The lack of weather resistance and heat resistance up to 100 °C have a limiting effect.
#5 Optimum O-ring design: Groove design
The optimum width and depth of the groove for standardized O-rings can be found in the respective tables.
Designers should also take into account the specific requirements of certain O-ring materials. The target compression range for FFKM is approx. 10 percent below the usual level.
Particularly with larger cord thicknesses, the O-ring design should ensure less compression via the groove.
We have put together a table to make it easier for you to design the optimum groove. Below you will find all the table values you need to design a flange, piston or rod seal.
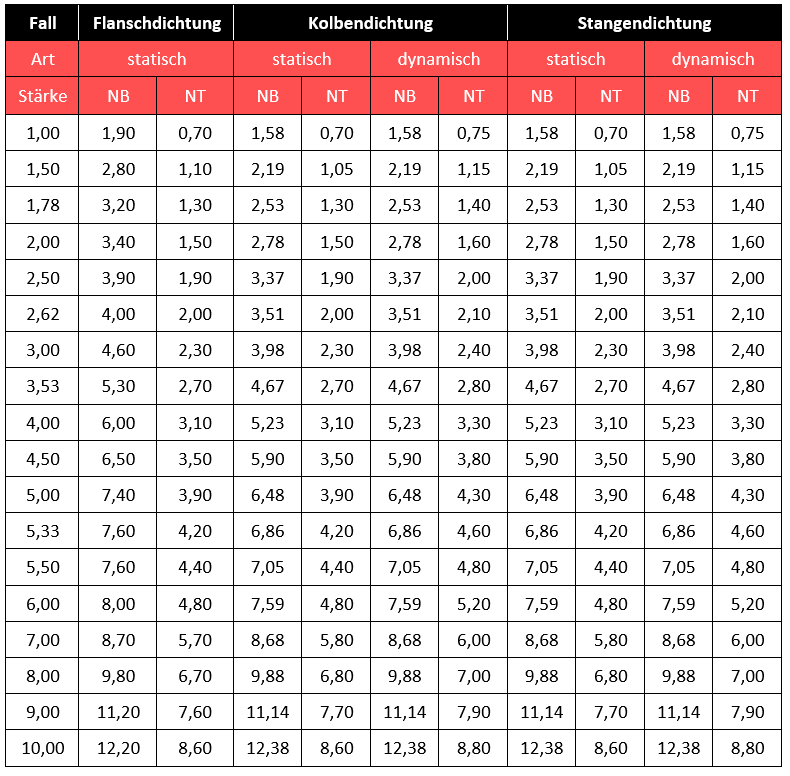
#6 Optimum O-ring design: System pressure
Four things are important to consider when designing a pressurized groove:
1. height of the pressure
2. direction of pressure
3. shore hardness of the O-ring
4. size of the sealing gap
These 4 points result in three basic rules:
1. high pressure = high hardness of the O-ring + minimum sealing gap
2.Pressure from inside = design O-ring with compression on the outer diameter
3. pressure from outside = design O-ring with expansion on the inside diameter
High system pressures and changing pressure conditions also require special care in the design.
The design can influence the extent to which the O-ring can move in the groove via the groove width. Especially in changing conditions, the movement to the side facing away from the pressure can cause mechanical wear on the O-ring.
The sealing gap also requires special attention. If it is lower, this reduces the risk of gap extrusion, where parts of the O-ring are sheared off at the groove edge. Materials with high hardness are less susceptible to this.
To make it easier for you to choose the optimum Shore hardness for printing, we have put together a table with the most important data.
Note: The table is based on a cord thickness of 2 mm. As a general rule, the greater the cord thickness of the O-ring, the larger the sealing gap may be.
O-ring hardness | Print height | Sealing gap |
---|---|---|
70 Shore A | 0-50 bar | 0.06 mm |
50-100 bar | 0.03 mm | |
100-200 bar | Do not use | |
80 Shore A | 0-50 bar | 0.08 mm |
50-100 bar | 0.05 mm | |
100-200 bar | 0.02 mm | |
90 Shore A | 0-50 bar | 0.11 mm |
50-100 bar | 0.06 mm | |
100-200 bar | 0.03 mm |
#7 Optimum O-ring design: Static vs. dynamic application
Back-up rings are particularly suitable for static seals.
However, this is not the only difference between static and dynamic applications. For example, some materials are hardly suitable for dynamic use from the outset because they are too susceptible to abrasion.
Other materials can be used without any problems, but a lower compression should be selected.
Note: In principle, FEP-coated, VMQ and FVMQ O-rings are not suitable for dynamic applications. All other O-ring materials can be used for dynamic applications.
#8 Optimum design for greater efficiency
With O-ring seals, it is not the cost of producing the installation groove or procuring the O-rings that determines cost-effectiveness.
In the long term, a reliable operating phase has an enormously positive effect on overall costs. The one-off savings on purchases can quickly evaporate.
The construction should therefore be designed from the outset to create optimum conditions for a long service life through the right choice of materials, careful groove design and specific consideration of the operating conditions.
“I am convinced that we should share our knowledge with the world. I hope I have been able to answer all your questions. If you have any further questions, please feel free to contact us at any time. We will be happy to help you.”
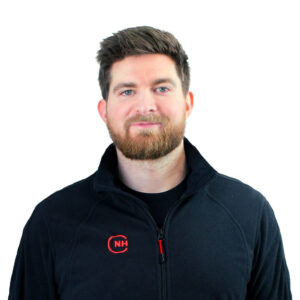
Lord of the O-rings
Author of the poetry academy