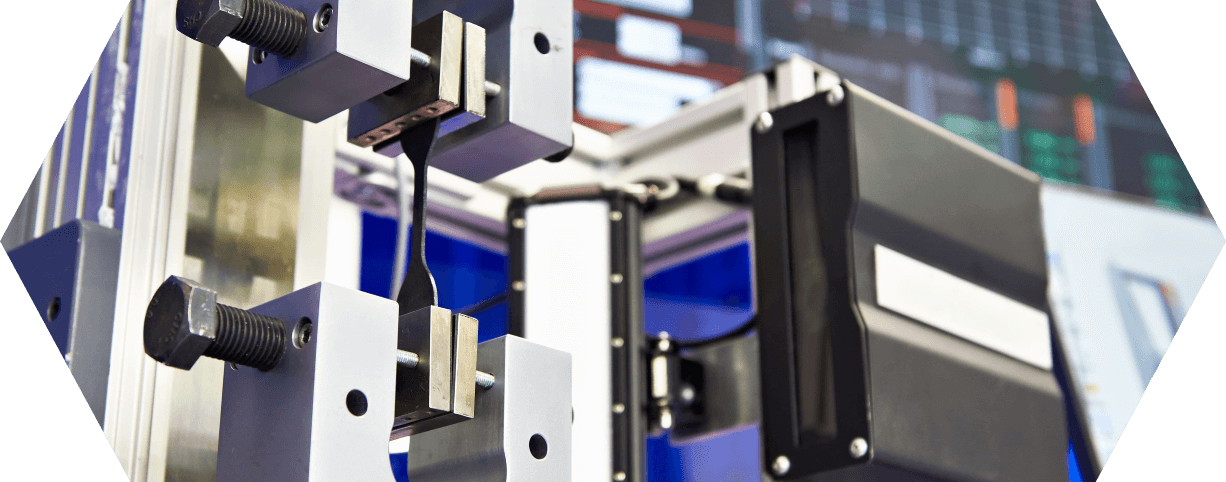
10 questions: O-ring data sheets
In this short article, we answer the 10 most important questions about the correct design of O-ring data sheets in a simple and understandable way.
Whether to facilitate assembly, improve mechanical properties or visually differentiate O-rings: The finishing of elastomer surfaces is playing an increasingly important role in professional sealing applications.
This represents significant potential for increasing efficiency in many areas of application, but also brings with it new challenges. Given the large number of base polymers, it is not easy for engineers to find the optimum technical solution anyway.
This is how complex the interaction of mechanical, thermal and chemical loads, industry-specific material requirements and the design of the sealing point is.
However, in order to make optimum use of the surface finishing options for O-rings, the technician must not only be familiar with them. Early consideration of possible refinements during the design process is also becoming increasingly important.
Elastomer technology has not reinvented the principle of surface finishing. As in general surface technology, the engineer also strives for functional separation between the volume and surface of the O-ring in elastomers.
The motives for changing the surface properties can be very different: improved mechanical protection of the component, the prevention of interactions between interfaces and optical recognition and differentiation are just a few examples.
Many properties of O-rings can be better adapted to the intended application by specifically influencing their surface.
In the case of O-rings, most surface requirements are aimed at improving assembly behavior, automating assembly processes and increasing resistance to dynamic stress. The top priority here is to minimize the impact on the technical properties of the elastomer material.
After all, it is precisely these that ensure the primary function of the components with the sealing effect. In addition, suitable surface finishing processes are also characterized by the fact that they have little effect on the component dimensions.
Improved sliding properties of the surface significantly reduce assembly forces. This reduces the risk of mechanical damage to the O-ring due to excessive stretching or twisting. Assembly oils and greases are the simplest countermeasure against excessive friction.
During the operating phase, however, they can cause undesirable interactions with the components to be sealed. They not only influence the results of leak tests.
As a result, surfaces contaminated with lubricants can hardly be painted without defects and the strength of bonded joints also suffers. In addition, auxiliary materials that are unsuitable for the sealing material can irreversibly damage the elastomer, for example through leaching. Dry friction-reducing coatings for O-rings prevent both: they make installation easier and damage-proof without restricting the functionality of the seal during operation.
Not only does manual assembly benefit from the reduction in friction of the O-rings, automatic process steps for handling and positioning the sealing elements also gain substantially in reliability. Excessive friction coefficients of the O-rings, for example, regularly make automatic feeding to the assembly process more difficult.
Vn addition, many O-rings made of elastomers in their pure form tend to stick together, meaning that separation is not always successful. Static charging and the contamination of system parts by loosely applied auxiliary materials also cause problems.
The visual differentiation of O-rings of different types not only plays an important role in incoming goods.
It also makes an important contribution to the reliability of assembly processes. While handling and manual installation are primarily concerned with reliably distinguishing between gaskets made of different materials or with different dimensions, there is another aspect to processes with a higher degree of automation.
Many users safeguard the automatic assembly of O-rings with camera-based 100% monitoring. This is how they ensure the desired result: there should be exactly one seal at the installation location. Colors or markings on the O-ring help here. They provide a remedy, for example, if a camera has difficulty recognizing a normally black sealing ring in a dark housing.
The fact that untreated elastomers tend to adhere to interfaces is also a challenge when O-rings are used dynamically as piston or rod seals. O-rings can stick to their mating surfaces, especially during longer downtimes.
If the connection becomes loose again during movement, the so-called stick-slip effect can occur. This results in jerky sliding of the friction partners. In addition to the disruption of the movement sequence, there are undesirable side effects in the form of increased wear and noise.
By reducing friction, the engineers ensure less abrasion and precise movements.
An original industry-specific requirement relates to the cleanliness of the O-rings themselves. The requirement that not only the components used, but also tools and systems must be free of paint wetting impairment substances (LABS) originally comes from the automotive industry.
However, similar specifications, in some cases adopting the original test specifications, are now also used in many other areas.
The background: O-rings in their raw state may contain manufacturing residues and formulation components that prevent the formation of a closed coating layer on contaminated component surfaces. Unlike with metals and many plastics, surface cleaning is not sufficient to ensure that elastomer seals are LABS-free.
The increasing demands on sealing elements have also led to greater differentiation in the finishing processes.
This means that there is a suitable finishing process available for almost every application. Here we provide an overview of standard processes for the common objectives of modifying the surface properties of O-rings: Easier assembly, increasing the degree of automation and usability for dynamic applications.
A clean material surface is the basis for successful surface treatment. However, there are also cases in which it is not a matter of coating or converting the surface of the O-ring. This is the case when ensuring freedom from LABS.
Deep cleaning is required to ensure that the substances that impair paint wetting disappear completely.
Simple wet cleaning using a drum process to remove superficial production residues is not sufficient here. The plasma cleaning process penetrates to the core of the material without affecting its physical properties. Important: Special packaging is required to maintain the absence of LABS after cleaning.
The sliding properties of O-rings can also be improved by the manufacturer adding the solid lubricants to the material formulation.
No further processing of the finished O-ring is then necessary, but only a very small proportion of the lubricant it contains becomes tribologically effective. For the coating of the surface, the drumming on of substances has become established to facilitate assembly and for dynamic applications, bonded coating.
Silicone (silicone coating), talcum (talcum coating) and molybdenum sulphate (molycoating) are widely used. All materials have their disadvantages: While silicone tends to stick to the O-rings, talcum and molybdenum have low abrasion resistance, which can lead to contamination of system parts.
The anti-friction coating with PTFE or graphite stands out due to its dry and clean surface. Depending on the requirements, manufacturers can apply durable PTFE coatings in many colors, transparent and with different microstructures.
Due to their comprehensive material approvals and high reliability, encapsulated or solid O-rings made of FEP and PTFE represent an important segment in the portfolio of high-quality sealing elements.
Considerable freedom in the choice of O-ring dimensions facilitates their use. This diversity poses a challenge: Customers must be able to rely on the short-term availability of O-rings according to their specifications.
We respond to these requirements with a wide range of solid and filled FEP and PTFE O-rings in stock, as well as short response times for customized production and delivery. As experts, we are also on hand to assist our customers with questions relating to design and testing, which need to be checked particularly thoroughly when O-rings are used dynamically.
“I am convinced that we should share our knowledge with the world. I hope I have been able to answer all your questions. If you have any further questions, please feel free to contact us at any time. We will be happy to help you.”
Lord of the O-rings
Author of the sealing academy
In this short article, we answer the 10 most important questions about the correct design of O-ring data sheets in a simple and understandable way.
In this short article, we answer the 10 most important questions about the correct design of O-ring grooves in a simple and understandable way.
In this short article, we answer the 10 most important questions about the correct storage of O-rings in a simple and understandable way.
You need to load content from reCAPTCHA to submit the form. Please note that doing so will share data with third-party providers.
More Information