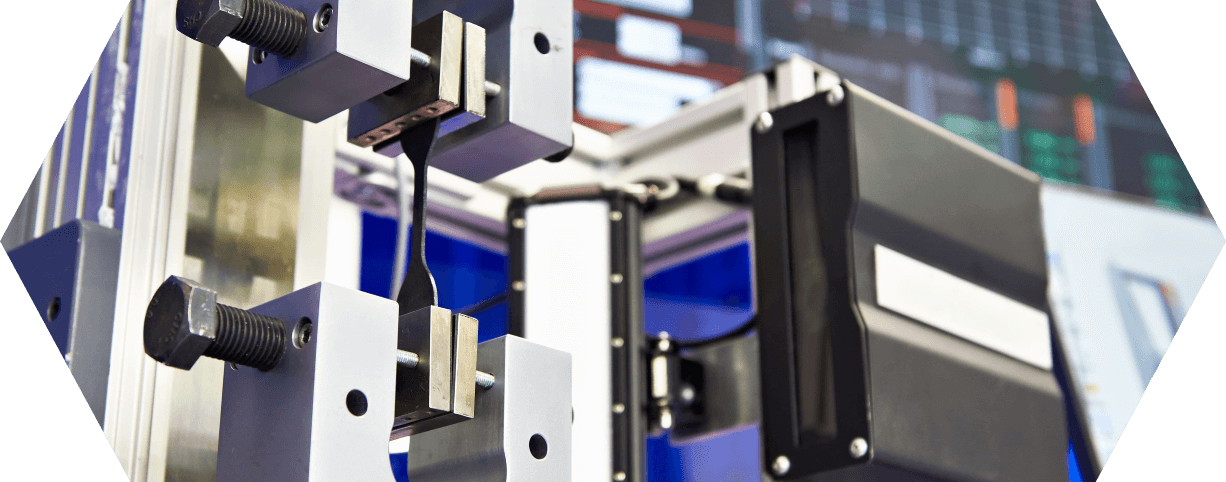
10 questions: O-ring data sheets
In this short article, we answer the 10 most important questions about the correct design of O-ring data sheets in a simple and understandable way.
An O-ring without elastic properties? This only works in exceptional cases. O-rings need the rubber elasticity to flow into the fine unevenness of the sealing surfaces. This also requires mechanical pressing of the O-ring.
So they ensure maximum tightness even between components that are not optimally machined. Elastic behavior is also required if, for example, sudden pressure surges change the position of the sealing surfaces in relation to each other.
Provided they are manufactured and stored correctly, elastomer O-rings have the necessary restoring force during installation to automatically return to their original shape after the pressure has been relieved. However, extreme temperatures and harmful media can greatly reduce this capability during operation.
Permanent deformation then occurs, which severely limits the service life of the seal.
If the O-ring is permanently deformed, it has adapted to a static position in the sealing system. This is determined by the compression of the cross-section between the sealing surfaces.
In addition, a medium such as cooling water or hydraulic oil can exert pressure on the sealing element. This also determines the positioning of the O-ring in the sealing gap and can cause further deformation of its cross-section.
If the pressure conditions change, an elastic O-ring tends to return to its original geometry and dimensions.
This is determined when the polymer molecules are cross-linked during the shaping process. Force-induced stretching stretches the molecules. If the force is removed, the molecules return to their original position in relation to each other. Entropic processes are responsible for this.
If, for example, the screw connection on the cover of a flange gasket becomes loose, the pressure on the O-ring decreases. The axial compression of the cross-section between the sealing surfaces is reduced.
From the forced oval shape, the cross-section of the O-ring must return to the round shape as far as possible. This fills the enlarged space between the groove in the housing and the flange cover.
In dynamic applications, changes in the sealing system occur even more quickly. The arrangement of the components to be sealed is less fixed here.
The forces acting on the O-ring are therefore constantly changing. How well it adapts to the pressure conditions determines the tightness of the connection. In the process industry, where chemical and pharmaceutical products are manufactured, there are often changing pressure conditions.
Liquids and gases are subjected to very high maximum pressures, but these can drop again very quickly. This must also be cushioned by the O-ring.
If a permanent deformation occurs, the O-ring is often no longer able to do this. The pressure then drops without the O-ring returning to its original shape.
In the case of the flange gasket with a loosening screw connection, the cross-section does not relax sufficiently to close the enlarged sealing gap. There is a leak. A lower permanent deformation generally indicates a higher quality of the O-ring material.
The ability of an O-ring to return to its original shape after pressure relief is measured by the compression set (compression set). This is an important material-dependent key figure. It can always be found in the data sheet of an O-ring material.
The higher the compression set, the more the seal is affected by temporary compressive stress. The O-ring then retains a permanent plastic deformation.
The technician determines the compression set in this way: The cross-section of the O-ring is compressed by 25 percent using a weight.
This can be done in tempered air, but also on all other relevant contact media. This is because temperature and media have an influence on the compression set. In this way, laboratories can also evaluate the effects of swelling or extraction on the compression set.
However, the information in the material data sheet refers to storage in heated air in a heating cabinet. After releasing the load, the sample is given time to relax again.
The extent to which the O-ring cross-section has returned to its original round shape can now be measured. When designing a seal, it is important to take into account the compression set in the corresponding contact medium.
This is illustrated by the example of EPDM: in air, the material shows high permanent deformation even at 150 °C. However, O-rings made of EPDM are very suitable for use with hot water and steam. Here, the seals retain a low permanent deformation even at higher temperatures.
This is how technicians recognize the permanent deformation during damage analysis, for example: When removing an internally sealing piston seal, the lack of radial contact pressure on the sealing surface is noticeable. Then the O-ring has permanently taken on the change in shape caused by the oversize of the piston.
The mechanism behind the loss of elasticity is always this: under the influence of environmental conditions, bonds in the molecular structure of the polymer are lost. At the same time, high temperatures can lead to post-crosslinking.
In the process, the molecules form further bonds that increase the rigidity of the material. Permanent deformation does not only occur in hot environments. Cold can also cause such a reaction in the material. Unlike the other causes, however, the permanent deformation is reversible by reheating.
The elasticity of an O-ring depends on the base polymer, material formulation and sufficient vulcanization. However, the design of the groove and the operating parameters can also contribute to failure due to permanent deformation.
If the installation space is too small, for example, this leads to a very high compression of the O-ring cross-section. The general target range is between 15 and 30 percent. However, the recommendations differ for certain materials. This also applies to the FFKM material, which requires less compression.
Important to know: The deformation forces increase with the same percentage compression and increasing cord thickness. The effect of a larger cord thickness must therefore be compensated for by lower compression.
In addition, the combination of temperatures, pressure and aggressive media can quickly lead to permanent deformation in unfavorable cases. If not stored properly, O-rings can be installed with permanent deformation. For this reason, central storage of O-rings is always preferable. Optimal conditions can be created here.
In addition to preventing premature ageing, this also includes the exclusion of unwanted pressure loads. In the workshop, it is easy for tools or material to accidentally land on an O-ring and permanently deform it.
The permanent deformation provides information on how well the elastic recovery capacity of an O-ring is maintained. However, how long an O-ring with permanent deformation maintains its tightness depends on the individual sealing system.
In some cases, O-rings can still be tight with a permanent deformation of 80 percent, while other seals fail even with significantly less permanent deformation.
It therefore depends on the entire sealing system how effectively permanent deformation must be excluded. Engineers have to take a large number of mutually influencing factors into account when designing.
If the sealing point is present, the O-ring itself is tested first. The best possible fit between the O-ring and the operating conditions can be achieved by selecting different base polymers and compounds. Hardness and media resistance with simultaneous exposure to temperature play an important role here.
Improvements in quality are also possible. Only if an O-ring is optimally cross-linked during vulcanization will it meet the specifications for compression set. Quality controls ensure that the O-rings meet the specifications.
If this is not enough to create a stable sealing system, much more complex measures usually follow. Depending on the type and size of the technical system, installation grooves can be reworked to optimize the compression of the O-ring cross-section.
This can be done as part of planned maintenance, which limits downtime. Improving the operating conditions at the sealing point is often particularly time-consuming. The temperature and pressure of process media cannot usually be changed easily.
The same applies to friction-induced heat development at the sealing point.
“I am convinced that we should share our knowledge with the world. I hope I have been able to answer all your questions. If you have any further questions, please feel free to contact us at any time. We will be happy to help you.”
Lord of the O-rings
Author of the sealing academy
In this short article, we answer the 10 most important questions about the correct design of O-ring data sheets in a simple and understandable way.
In this short article, we answer the 10 most important questions about the correct design of O-ring grooves in a simple and understandable way.
In this short article, we answer the 10 most important questions about the correct storage of O-rings in a simple and understandable way.
You need to load content from reCAPTCHA to submit the form. Please note that doing so will share data with third-party providers.
More Information