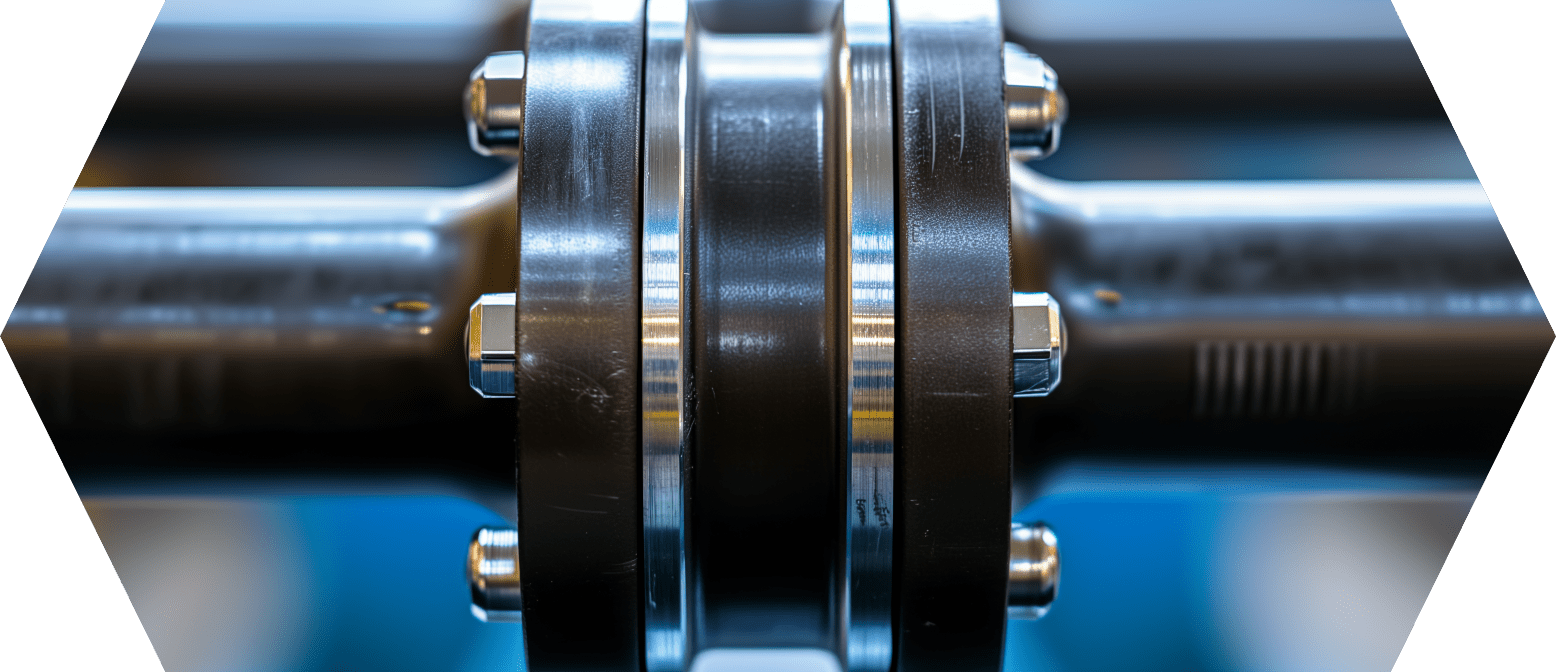
Flange gasket
Flange gaskets are crucial for the integrity of piping systems and their safety.
Water and steam put the durability of O-rings to the test. The challenge is that extreme temperatures are added to the undesirable interactions between the contact medium and the sealing material.
Such demanding operating conditions are found primarily in the process industry, power plant technology and in the sanitary and heating engineering sectors. Only special O-ring qualities offer the necessary resistance. Here you can find out what requirements hot water and steam have and which materials are suitable.
The process industry is a prime example of the very high demands placed on the quality of sealing elements. Very high heat is usually generated during operation – often alternating cyclically with thermal conditions well below room temperature.
This applies to refineries, for example, as well as to food and beverage production. At the same time, the O-rings come into contact with media that can attack the material of the O-ring. Hot water and steam have proven to be particularly problematic in practice. These media must also be handled in power plants and district heating systems. Water temperatures of up to 175 °C are not uncommon.
In plants for the production of dairy products, for example, O-rings are exposed to intermediate and end products with a high fat content.
Aggressive media and very hot steam are used to maintain hygienic conditions. High-quality O-rings must be able to withstand these conditions permanently, because the service intervals are long. This results in high downtime costs and costly replacement procedures.
In many applications, it is also important that the O-ring itself does not affect the contact media. This is required by the strict industry standards.
Long replacement intervals, extreme temperatures and pressures: These are demanding operating conditions. These influences cause the O-ring to lose its elastic restoring force over time. If this is weakened too much, the O-ring cannot withstand mechanical loads and does not adapt sufficiently to the sealing gap.
The component loses its sealing effect. But hot water and steam also damage the O-ring.
The media cause unsuitable elastomer materials to age very quickly. There are various damage mechanisms. Contact media can penetrate the material of the O-ring and cause it to swell. If the groove is overfilled by a swelling O-ring, gap extrusion can occur when pressure is applied.
Media also cause a change in the mechanical material properties. This applies, for example, to elongation at break and hardness, two key parameters for the sealing function. Shrinkage, in which aggressive media dissolve formulation components from the elastomer, has the same consequence. In addition to the impairment of the sealing effect, the medium is usually contaminated in an impermissible manner.
Among other things, water contains hardening agents, carbon dioxide and oxygen, which cause metals to corrode. The water breaks down chemical compounds through hydrolysis.
It gradually degrades many polymer sealing materials, resulting in shrinkage and the associated loss of compression. However, a minimum compression is necessary so that the O-ring can fully develop its restoring force and bridge the sealing gap.
The mechanisms also work with water vapor. However, the aggressiveness of the medium also depends on the saturation of the water vapor. The degree of saturation expresses how highly concentrated the water vapor is in the air. This is particularly important when using EPDM O-rings. This is because this material has the extremely useful property that its resistance to air is significantly lower than its resistance to steam.
In addition, many systems with hot water and steam have a cyclical sequence of operating phases. Here, extreme heat alternates with cold.
Low temperatures are generally gentler on the O-rings. However, cyclical operation results in many changes of state, which affect the sealing gap each time. A falling temperature causes the sealing gap to become larger, while the O-ring itself is also subject to thermal shrinkage.
When the gap is bridged, the resilience of the O-ring is significantly more stressed than at a permanently high operating temperature. This means that leaks can occur during cyclical operation even if the O-ring still has elastic properties.
O-rings suitable for use with hot water and steam are characterized by the fact that they retain their initial properties for as long as possible when exposed to the media. After they have been exposed to them for a certain period of time, they are examined in laboratories, primarily for these criteria:
The more consistent the properties remain even after prolonged use, the better the suitability of the polymer material.
There are some materials that have the potential to withstand water and steam at high operating temperatures. How well they do this in practice is significantly influenced by the exact composition of the O-ring and how carefully it is manufactured.
In general, the following base polymers are suitable. In practice, the elastomers EPDM and FFKM in particular have proven themselves.
Material | Temperature resistance air | Temperature resistance steam |
---|---|---|
NBR | 120°C | 80°C |
VMQ (silicone) | 200°C | 100°C |
FKM (VITON) | 200°C | 120°C |
EPDM (PC) | 150°C | 170°C |
FEP coated | 200°C | 200°C |
PTFE | 200°C | 200°C |
FFKM - ECOLAST NH5750 | 270°C | 210°C |
FFKM - ECOLAST NH5751 HT | 330°C | 230°C |
FFKM - ECOLAST NH5755 HT | 330°C | 260°C |
O-rings with EPDM as the base polymer and very good chemical stability reliably retain their properties even when exposed to hot water and steam at temperatures of up to 200 °C.
The prerequisites for this are a high-quality recipe and optimally adjusted production processes.
O-rings made of EPDM for hot water applications are peroxide cross-linked and contain as little plasticizer as possible. By adding special anti-ageing agents to the formulation, the manufacturer can increase resistance even further. A high degree of vulcanization gives the elastomer its elastic properties.
Time, pressure and temperature must work together optimally here.
If this is the case, EPDM O-rings show only slight changes in volume, elongation at break and tear resistance in hot water and steam. The O-ring can therefore offer almost constant resistance to mechanical loads.
It is elastic enough to bridge even a varying sealing gap. However, EPDM O-rings are not suitable for some hot water applications as they are not resistant to mineral oil-based compounds. If air acts on the O-ring in addition to water, this also limits the durability of the O-ring. Resistance data in air above 150 °C are rare.
Together with FKM and FEPM, FFKM is a fluorinated elastomer. These are characterized by a very wide air temperature range.
O-rings made of FFKM are suitable for continuous temperatures well above 300 °C. Use with hot water also requires special recipes. The degree of cross-linking and the type of cross-linking in the polymer are just as decisive.
At the same time, FFKM has a very high resistance to aggressive media. Such substances are widely used in the chemical and petrochemical industries, for example. Mineral oil is therefore not a problem for FFKM. Therefore, the comparatively high costs for FFKM O-rings are particularly justified if the sealing elements are exposed to other aggressive media in addition to hot water or steam.
When it comes to O-ring seals for hot water and steam, it is not just the choice of material that is decisive. Equally important is the appropriate design of the installation groove.
The compression of FFKM O-rings, for example, should be significantly lower than that of other materials. In general, you should give preference to axial seals if feasible. These are less susceptible to component tolerances and also limit the effect of air on EPDM O-rings.
Installation requires special care from the technician. While FFKM O-rings are susceptible to mechanical damage, only suitable assembly greases may be used for EPDM O-rings.
Free expert advice:
Take advantage of the application expertise of our experts. They will work with you to identify the right O-ring for your sealing application. They also pay attention to the optimal design of the installation space and thus create the durability that demanding applications require.
“I am convinced that we should share our knowledge with the world. I hope I have been able to answer all your questions. If you have any further questions, please feel free to contact us at any time. We will be happy to help you.”
Lord of the O-rings
Author of the sealing academy
Flange gaskets are crucial for the integrity of piping systems and their safety.
Flange gaskets are crucial for the integrity of piping systems and their safety.
Flange gaskets are crucial for the integrity of piping systems and their safety.