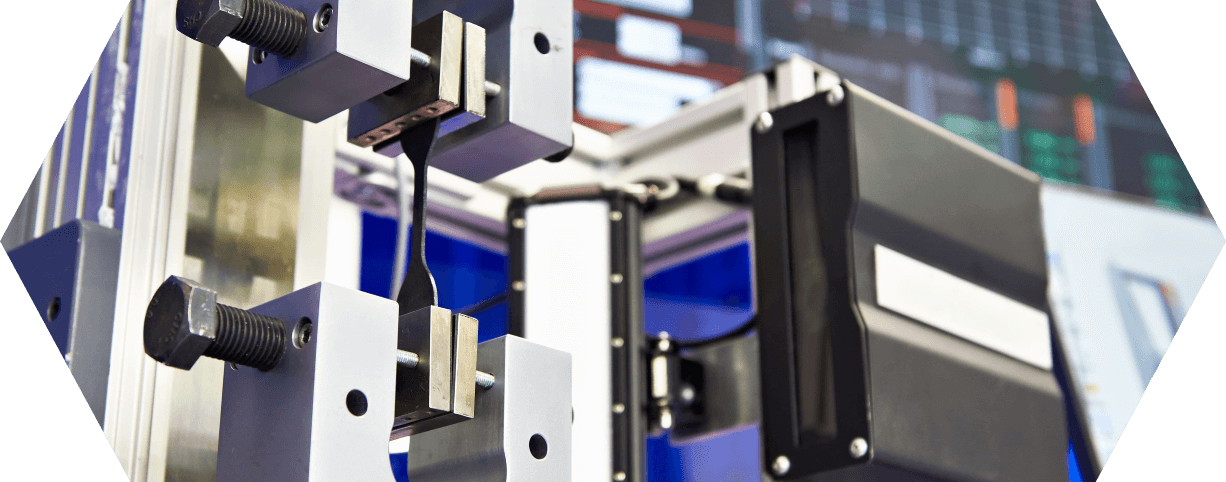
10 questions: O-ring data sheets
In this short article, we answer the 10 most important questions about the correct design of O-ring data sheets in a simple and understandable way.
Users are attaching more and more importance to the careful design of O-ring seals. They check the operating conditions and select a suitable O-ring material in the correct dimensions. This results in the groove design and other design details. Trained personnel use the recommended installation tools and install the O-ring without causing damage.
Does this mean that all the precautions for a reliable seal have been taken? Not quite, because the quality of the O-rings often remains a big unknown. Global procurement markets and the considerable influence of formulations and production processes on the performance of sealing elements create uncertainty.
In this article, we show why end customers should definitely rely on supply chains with assured quality standards. We also outline a practical quality assurance system for sealing elements.
Low prices and few objective technical differentiators: This is the perspective from which many end users view the procurement market for sealing elements. Accordingly, price is the leading factor in purchasing decisions.
Too little focus on quality has its risks: Because if O-rings fail during operation, this can have considerable consequences. For example, entire product batches can be contaminated, leading to their disposal. In the same way, hazardous or environmentally harmful media can escape at the sealing point.
In addition to this almost incalculable risk, there is the possibility of consequential damage to machines and systems.
A look at some areas of application shows that the durability of O-rings is a critical factor:
Reliable seals with O-rings are based on careful selection of material and dimensioning. In addition, there is the damage-free installation. However, these steps are only fully effective if the O-rings themselves meet the specified quality requirements.
Conversely, stable product quality forms the basis for reliable and economical seals. What is needed are secure supply chains with integrated quality management. They ensure that only O-rings that are up to the task are used. But which properties are decisive for the sealing effect of an O-ring? This question will be addressed in the next section.
The sealing effect of an O-ring results primarily from the uniform compression of the round cross-section between the sealing surfaces. Some requirements for dimensional accuracy and surface quality can already be derived from this.
To ensure adequate durability, the O-ring must also have a high resilience and sufficient hardness. This enables it to bridge changes in the sealing gap and withstand pressure peaks. The last category: The selected O-ring formulation should meet the expectations for resistance to ageing in air and to chemical attack by a wide range of contact media.
The task of quality assurance is to minimize the deviations of the finished O-rings from the defined target condition. Accordingly, quality control is aimed equally at detecting processing-related and recipe-related defects.
The generally accepted standards for O-rings indicate which properties are particularly important for their function. For example, DIN ISO 3601-1 specifies nominal dimensions and permissible tolerances for the inner diameter and cross-section of O-rings.
The 2015 edition of the DIN ISO 3601-5 standard is also considered a major success. This is because it defines internationally valid material properties for elastomer seals for the first time. The target values are specified on test specimens and on the finished product.
This is new, because up to now data sheet information has mainly referred to results on test panels. Due to the measurement methods, however, there may be significant deviations from the properties of finished products.
There are also many other guidelines for specific areas of application for O-rings. DIN EN 681 refers, for example, to the use of vulcanized rubbers for sealing water supply systems. This standard is only representative of many fields of application with special requirements for the properties of O-rings. Overall, the requirements can be divided into these categories:
Quality tests ensure that the finished O-rings meet the applicable requirements.
The choice of a base polymer determines the essential properties of a gasket material. This is because each rubber has its own individual profile in terms of temperature range, media compatibility and mechanical properties. Nevertheless, it should not be neglected: Depending on the formulation and processing, this profile can vary in the finished O-ring. The examples show how these factors can affect durability.
Fluctuations in hardness: Test laboratories have noticed fluctuations in the hardness of O-ring materials based on VMQ in particular. They often result from post-processing steps. The hardness influences how well the O-ring adapts to the metal sealing surfaces. O-rings that are too soft are susceptible to gap extrusion under pressure.
Ensuring the quality of sealing elements is a demanding task. It is divided into the usually one-off inspection of the material formulation.
It is particularly extensive and is the responsibility of the manufacturer. This is followed by tests during series production to ensure consistent product properties. This mainly relates to the composition and dimensional tolerances of the O-rings.
The technical possibilities for measuring O-rings and testing the material composition have developed significantly. Today, they allow much more efficient quality control. This applies to all relevant property fields:
Great progress has been made in the area of workpiece dimensions in particular. Non-contact systems avoid deformation of the O-ring and thus lead to significantly better results. Optical measurement technology is just one example. The table shows that common laboratory procedures require a wide range of high-quality equipment:
Procedure/ measuring equipment |
Scope |
Optical measuring machine |
Diameter, cord thickness |
Digital microscope |
Surface deviations |
Compressive stress relaxation test |
Material behavior under the influence of temperature |
Thermogravimetric analysis |
Description of the material composition |
But the equipment alone is not enough. Reliable results are hardly possible without the necessary know-how on the part of the user. NH O-RING therefore works together with a proven specialist: The O-ring testing laboratory Richter uses state-of-the-art processes to ensure the quality of its products. Here, new materials are comprehensively qualified for series production.
The laboratory also carries out ongoing tests to ensure series quality. With this competent partner, NH Dichtungsservice does everything to ensure that only perfect quality reaches the end customer.
The purchasers of O-rings generally carry out a simplified identity check on incoming goods. It usually consists of these components:
The main aim here is to rule out any mix-up of materials in the upstream process chain. In addition, some companies also use tensile tests or swelling tests.
The mechanical tests can also reveal significant processing-related deviations between different batches. In addition, dimensional tolerances and surface quality are checked.
End users can effectively protect themselves against the risks of poor quality O-rings. Above all, they should rely on transparent supply chains and reliable partners.
Manufacturers and suppliers of O-rings for commercial use carry out extensive quality tests in order to maintain a high standard. This not only relieves their customers of the risk, but also saves costs. The more customers can rely on the quality of the O-rings supplied, the less effort is required for internal testing.
Provided you have reliable partners, a lean process in incoming goods provides sufficient security. Those who increasingly take quality criteria into account when making procurement decisions can realize lower costs overall.
“I am convinced that we should share our knowledge with the world. I hope I have been able to answer all your questions. If you have any further questions, please feel free to contact us at any time. We will be happy to help you.”
Lord of the O-rings
Author of the sealing academy
In this short article, we answer the 10 most important questions about the correct design of O-ring data sheets in a simple and understandable way.
In this short article, we answer the 10 most important questions about the correct design of O-ring grooves in a simple and understandable way.
In this short article, we answer the 10 most important questions about the correct storage of O-rings in a simple and understandable way.
You need to load content from reCAPTCHA to submit the form. Please note that doing so will share data with third-party providers.
More Information