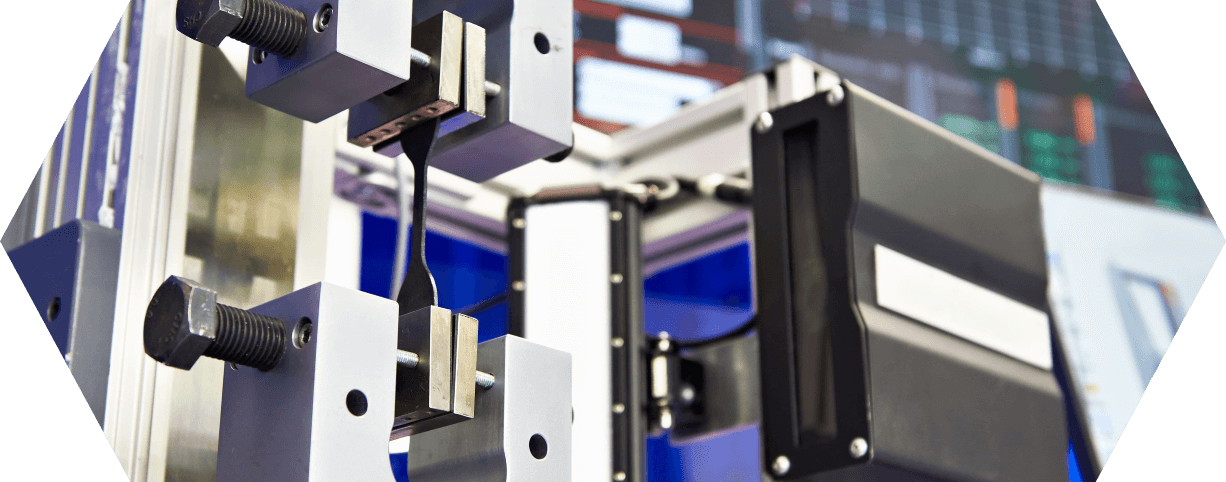
10 questions: O-ring data sheets
In this short article, we answer the 10 most important questions about the correct design of O-ring data sheets in a simple and understandable way.
Hardness is undeniably an important parameter for the quality of O-rings. Above all, it indicates how well the material adapts to unevenness in the sealing surfaces under pressure. Less hard O-rings can do this better, but are also more susceptible to gap extrusion at high pressure. The right choice of hardness is crucial for the reliability of the seal.
Hardness testing is also used to identify and test the quality of elastomer formulations and finished parts. However, hardness only provides part of the necessary information.
Although the key value is important, it is of limited significance on its own. In this article, we summarize everything you need to know about the hardness of O-rings.
According to the general definition, the hardness of a material indicates the resistance it offers to penetration by a harder body. To a certain extent, the harder body produces an elastic deformation of the softer one.
The object then returns to its original shape after being relieved. If the deformation is plastic, the body retains part of the deformation even when the pressure is no longer applied. Hardness is one of many important specifications that can be found in the technical data sheets of O-rings:
When using O-rings as a sealing element, their elastic deformation is desired. To do this, the elements to be sealed exert pressure on the O-ring. This adapts to the contours and seals the gap between the sealing surface and the installation groove.
The cross-section of the O-ring is then no longer circular, but elliptical. This deformation is also called compression.
The softer an elastomer is, the less pressure is required to achieve the deformation. The O-ring then compensates for even larger surface defects on the sealing surfaces under low loads. These originate from the machining of the components. For example, cast parts have burrs along the demolding plane.
The quality of the post-processing determines how much of these production-related traces are still present when the O-ring is installed. O-rings with higher hardness require more pressure to achieve the necessary compression. O-rings with low hardness are therefore more suitable for applications with low pressure.
But there is another factor: the medium to be sealed can also exert pressure on the O-ring. This is initially good for the sealing effect, as it increases the compression. However, if the pressure is too great, the effect is counterproductive.
The O-ring moves to the side of the groove facing away from the pressure. The O-ring may then move into the sealing gap. This so-called gap extrusion can cause permanent damage so that the sealing effect of the O-ring is lost.
There are two measures available to the designer for media with high pressure: He can optimize the installation situation so that the sealing gap is as small as possible. Choosing an O-ring with a higher hardness also helps with this problem. In the case of dynamic seals, friction and wear of the O-ring also play an important role. They are also related to the hardness of the O-ring.
The hardness of the O-ring must therefore always be matched to the individual operating conditions.
The principle behind the test methods for hardness is simple: a test specimen exerts pressure on the material being tested. The depth to which the harder body penetrates the softer body is measured.
Among other things, the shape of the test specimen, compressive force and measuring time must correspond to the comply with standardized procedures. This is precisely where the widely used Shore and IRHD (International Rubber Hardness Degree) test methods differ. This also has an impact on the application of the procedures in practice.
The specifications for the Shore measurement are given in DIN ISO 7619. The test engineer does not usually use this method to test the hardness of the finished part.
Instead, a standard sample with defined dimensions is used. This measured value can be found later in the O-ring data sheet. There are two different variants, Shore A and D. For O-ring materials, the Shore A test is particularly applicable.
The standard stipulates a specimen thickness of at least 6 millimetres for testing vulcanizates, such as O-rings. The conical test specimen acts on the sample for 3 seconds under spring force. The temperature also has an influence on the material behavior.
For this reason, a target temperature of 23 degrees applies, from which there should be no deviation of more than 2 degrees up or down.
During evaluation, the tester converts the measurement result for the penetration depth. A depth of 2.5 millimeters corresponds to a hardness of 0 Shore A. If the sample leaves no impression at all, the hardness is 100 Shore A. Very hard materials reach 90 points. The Shore hardness of finished parts can also be measured. This applies at least if the cord thickness of the O-ring is over 3 millimeters.
In the Shore D hardness test for tougher elastomers, key parameters change with the pressure and dimensions of the test specimen. Therefore, there is no linear relationship between the measured values for the two Shore hardnesses. However, a conversion is possible.
The hardness test according to IRHD-M also provides the hardness in scale values from 0 to 100. The method is primarily used to determine the hardness of prefabricated parts.
However, the IRHD measurement is not suitable for line thicknesses of less than 1.6 millimeters. In contrast to the determination of the Shore hardness, a significantly smaller spherical test specimen penetrates the O-ring here. The highest point in the cross-section of the O-ring should be the attachment point. After the test specimen has acted on the O-ring for 30 seconds, the operator can read off the hardness.
It is important to note that the hardnesses of an identical elastomer determined on standard samples and finished parts will almost always differ. In addition, the measurement results according to Shore A and IRHD-M cannot be converted into each other. This is true even though the results in the medium hardness range can be relatively close to each other.
This is due to the different measuring methods, but also to the shape-related deviations in the properties. Geometrically, the standard sample of a material and the O-ring as a finished part hardly have anything in common.
Different material thicknesses and the curved surface affect the measurement. As the O-ring cross-section decreases, the precision of the process decreases significantly.
Just as important is where the tester places the test specimen on the finished part. The many possible errors pose a major problem in hardness testing. The results are generally much less reliable than the other measurement methods.
A tolerance of 5 Shore A or IRHD hardness points upwards and downwards is therefore common. High-quality prefabricated parts comply with the specifications in the data sheet.
The widespread assumption that a hard O-ring is always better than a softer one is a misconception. In practice, it is much more a question of using an O-ring that is exactly as hard or soft as the application requires.
The engineer must take into account the complex interaction between the dimensions of the sealing gap, the properties of the O-ring and the pressure load.
However, one thing is undisputed: The hardness of the O-ring as supplied should correspond as closely as possible to the target value specified when the order was placed.
This ensures that the O-ring can reliably fulfill its sealing function. Very good suppliers of O-rings set themselves apart from average suppliers by taking comprehensive measures to monitor series quality. In this way, they ensure that their products meet the requirements of demanding applications.
In addition to hardness, they also keep an eye on other material properties such as weight and tensile strength. In addition, there is the behavior of the O-ring at high and low temperatures and the interaction with test media. Only together do these tests provide a comprehensive picture of the O-rings.
“I am convinced that we should share our knowledge with the world. I hope I have been able to answer all your questions. If you have any further questions, please feel free to contact us at any time. We will be happy to help you.”
Lord of the O-rings
Author of the sealing academy
In this short article, we answer the 10 most important questions about the correct design of O-ring data sheets in a simple and understandable way.
In this short article, we answer the 10 most important questions about the correct design of O-ring grooves in a simple and understandable way.
In this short article, we answer the 10 most important questions about the correct storage of O-rings in a simple and understandable way.
You need to load content from reCAPTCHA to submit the form. Please note that doing so will share data with third-party providers.
More Information