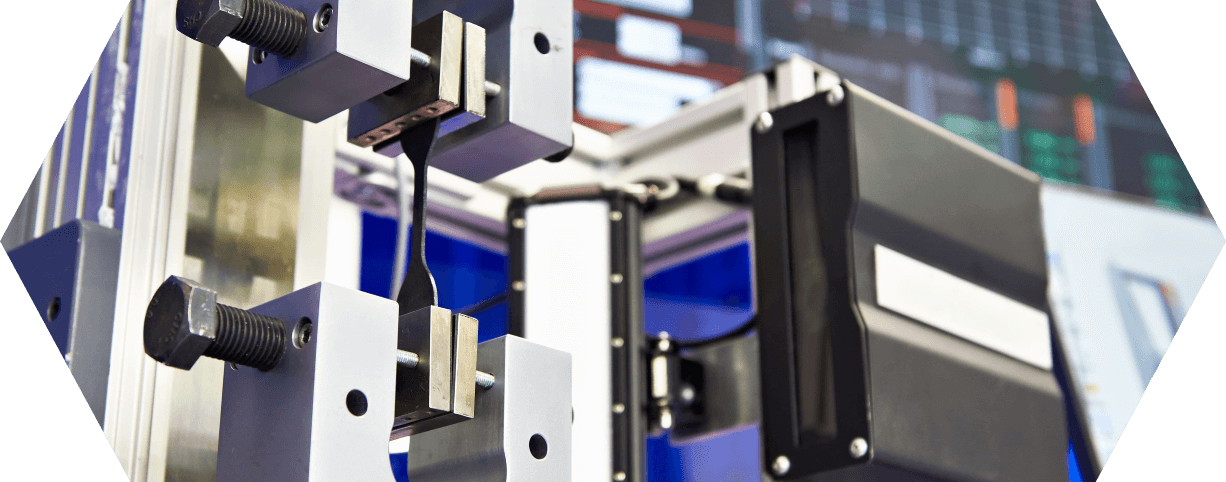
10 questions: O-ring data sheets
In this short article, we answer the 10 most important questions about the correct design of O-ring data sheets in a simple and understandable way.
Gap extrusion is one of the most prominent types of damage to O-rings. This is mainly due to the very distinctive peeling on the elastomer.
They clearly demonstrate the stresses to which O-rings are exposed in tough operating conditions. Cyclically alternating phases of very high and low pressure are the main cause of the damage.
In hydraulics in particular, gap extrusion is therefore one of the most common causes of O-ring failure. In this article, you will learn how gap extrusion occurs and how maintenance engineers can recognize the damage. At least as important for practitioners: We provide an overview of the factors that promote gap extrusion. This results in the most effective strategy against gap extrusion.
The phenomenon of gap extrusion can also be found in technical literature under the terms extrusion, gap migration or extrusion. The principle behind it is simple: O-rings made of elastomers have almost no compressibility.
As the pressure increases, the O-ring takes on more and more of the contour of the installation space. As the O-ring cannot be compressed, the pressure eventually presses it into the sealing gap between the piston and cylinder.
This process leaves very characteristic peeling marks on the sealing element. The edge of the groove shears off a thin layer from the surface of the O-ring. This usually does not happen in a circle, but mainly at the point with the largest gap.
If the piston and cylinder are not arranged precisely concentric to each other, the sealing gap will have different widths along the circumference. Under particularly unfavorable constellations of the sealing system, however, the O-ring can also roll around its entire circumference.
Depending on how strong the prevailing pressure is and how the sealing system is designed in its entirety, the length of the extrusion vane can reach a multiple of the cord thickness. In the event of rapidly changing pressure conditions, parts of the extruded material can also be separated from the O-ring. These particles pose a risk to sensitive processes. They can contaminate the process media or damage other system components.
Gap extrusion is caused by the mechanical load on the O-ring during operation. In practice, mechanical and physical influences on the sealing element are responsible for most seal failures.
In addition to gap extrusion, damage caused by assembly errors or inadequate groove design also plays an important role in this category. The description of the damage has already made this clear. These factors are particularly decisive for the risk of gap extrusion:
In gap extrusion, high and pulsating pressure provides the stress. Not only the level of the maximum pressure, but also the speed at which pressure changes occur, influences the load on the O-ring. Unmediated pressure surges cause an increased risk of gap extrusion.
The seal can offer little resistance to rapid deformation. Such a sudden pressure build-up occurs very frequently in hydraulic systems. Such pressure surges can occur in vehicle components as a result of sudden braking or abrupt changes in direction, for example.
In addition, the deformation resistance of elastomers varies greatly depending on the temperature. O-rings in hot temperatures can offer less resistance to the load than sealing elements in cooler environments.
If extreme temperature peaks are added to high operating pressure, gap extrusion is particularly likely. This applies at least if the designer does not include any protective measures in the design.
Here, the interplay between the dimensions of the sealing gap, the design of the groove recesses and the dimensions of the O-ring are decisive. The coordination of these factors is the basic prerequisite for the function of static seals. For dynamic seals, which have an even higher risk of gap extrusion, this design point is crucial.
The risk of gap extrusion increases with the size of the sealing gap. The problem: The realization of lower tolerances for the corresponding components leads to higher production costs. The components can also change shape under the effect of pressure and temperature.
In unfavorable cases, the maximum sealing gap can be the entire diameter clearance. This is the case when the piston and cylinder are positioned maximally off-center in relation to each other. Then there is the design of the groove edges. A sharp edge shears off the O-ring particularly easily when it enters the gap.
The designer should therefore provide a radius for the grooves. O-rings that are too thin are susceptible to gap extrusion. Although the pressure presses even stronger O-rings into the sealing gap, they can withstand the material removal for longer.
The choice of a harder O-ring is the standard recommendation for applications at risk of extrusion. However, it is actually the rigidity of the seal that protects it from being pressed into the gap.
However, the modulus of elasticity of the O-ring under different environmental conditions is often not available. Hardness is therefore an important indicator of the extrusion strength of an O-ring material.
Materials whose mechanical properties decrease significantly with increasing temperature are very susceptible to high pressures. The stress caused by the process media should also be taken into account when selecting the material. Damage caused by swelling and shrinkage reduces the gasket’s resistance to gap extrusion.
Knowledge of the active principle of gap extrusion and the causes is the decisive basis for successful prevention.
Therefore, designers who create sealing systems should be as well informed as possible about the behavior of elastomer materials under demanding operating conditions. Only then can they recognize sealing cases with a particularly high risk of gap extrusion and take countermeasures during the design phase.
When selecting the material, O-rings with higher hardness and strength should be given preference. Resistance to the process media used is always a prerequisite. If it suits the application, O-rings made of thermoplastics are an alternative.
Further possibilities arise through the use of molded seals or support rings. Moulded seals can be provided with a vulcanized fabric reinforcement. This makes the seal stiffer.
Designers follow a similar principle with the use of support rings. They are not firmly connected to the O-ring. Instead, the fitter inserts it in front of the O-ring on the side facing away from the pressure. If the pressure is applied alternately from both sides, a support ring is used on each side.
The components themselves have no sealing effect, but prevent the O-ring from migrating into the gap. They are available with a wide variety of profiles in slotted or closed versions.
This allows them to adapt to the installation situation and operating conditions. The standard material for back-up rings is PTFE, but POM or PA are also used.
If the options for material selection are exhausted without the desired success, the preventive measures become more complex. Other starting points are the reduction of the sealing gap and finer machining of the groove. The designer should use radii instead of chamfers.
However, the realization of smaller tolerances and precise radii requires increased manufacturing effort. A decision must be made on a case-by-case basis as to which combination of preventive measures is most effective in preventing crevice extrusion.
Operating conditions that are very challenging for O-rings require particularly careful design of the entire sealing system. This includes the selection of the sealing material as well as the definition of the cord thickness and the design of the groove.
The easiest way to alleviate the situation is, of course, to reduce the system pressure. This is the most problematic factor in gap extrusion.
However, as the pressure ranges are usually predetermined by other dependencies, the designer should make even better use of the remaining degrees of freedom. Various elastomer compounds with or without support ring, cord thickness and design of the installation groove offer effective approaches to limiting risk.
Our offer: Contact our team of application experts for the sealing of highly pressurized media. With their many years of experience, they support you in the holistic optimization of the seal. Through the interaction of all components, they create permanently extrusion-proof sealing systems.
“I am convinced that we should share our knowledge with the world. I hope I have been able to answer all your questions. If you have any further questions, please feel free to contact us at any time. We will be happy to help you.”
Lord of the O-rings
Author of the sealing academy
In this short article, we answer the 10 most important questions about the correct design of O-ring data sheets in a simple and understandable way.
In this short article, we answer the 10 most important questions about the correct design of O-ring grooves in a simple and understandable way.
In this short article, we answer the 10 most important questions about the correct storage of O-rings in a simple and understandable way.
You need to load content from reCAPTCHA to submit the form. Please note that doing so will share data with third-party providers.
More Information