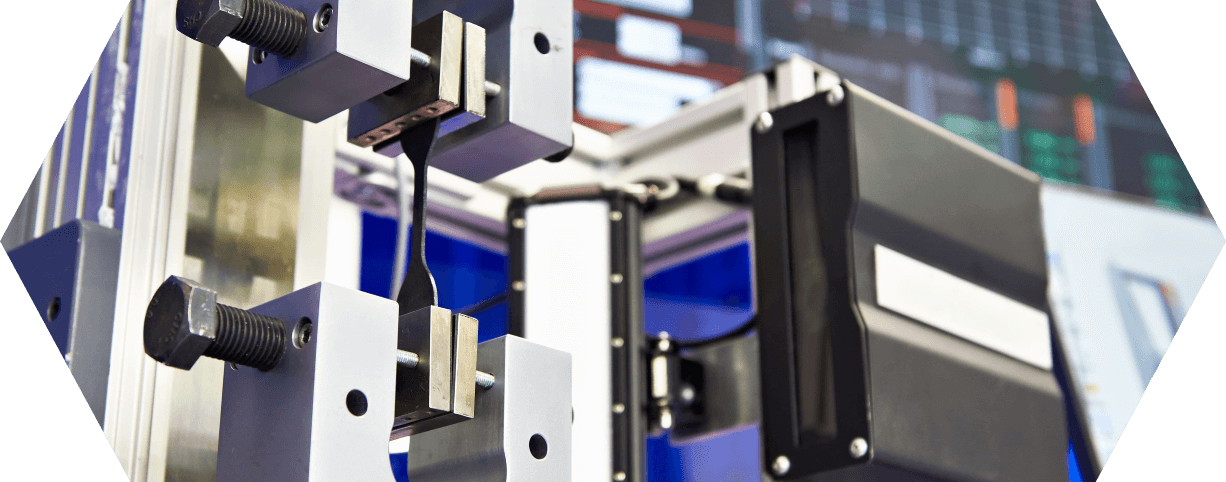
10 questions: O-ring data sheets
In this short article, we answer the 10 most important questions about the correct design of O-ring data sheets in a simple and understandable way.
Customers have a wide range of requirements for seals in terms of media contact, pressure and temperature loads and service life. The portfolio of sealing elements is correspondingly broad.
Just as the optimum product can be found for every sealing application, the right manufacturing process must also be selected for its production. The production method influences not only the technical properties of the seal, but also its cost. For industrial users, the successful resolution of the resulting conflict of objectives is crucial.
Quantities and delivery times that are acceptable to the customer are the decisive factors in the choice of process from an economic point of view.
On the technical side, other important factors include workpiece dimensions, the permissible tolerance range and the physical properties. The experts can already make a preselection based on the type of seal and material.
The rest of this article will focus on the manufacture of two classic seals: O-rings and flat gaskets.
The most widely used O-ring seal is a closed ring with a circular cross-section, the dimensions of which are determined by the inside diameter and cord diameter. O-rings are used for stationary (static) and moving (dynamic) seals.
The sealing effect occurs when pressure elastically deforms the cross-section of the O-ring. This results in surface pressure between the seal and groove base on the one hand and the seal and sealing surface on the other. For the system to work, the groove design and choice of material must be right.
O-rings are primarily made of elastomers, which have rubber-elastic properties. The raw rubber product acquires this property during vulcanization.
This process leads to cross-linking of the macromolecules and the resulting cross-links allow the material to return to its original position after an externally induced change in shape.
Because the media resistance of elastomers is not sufficient even for many demanding applications, the properties can be increased by coating the O-rings with suitable materials. These in turn often lack the elastic properties of an elastomer.
Examples of elastomers frequently used in sealing applications are NBR (acrylonitrile butadiene rubber), FKM (perfluoro rubber) and FFKM (fluoro rubber). However, the materials are just as well known under the protected trade names of the respective manufacturers.
Flat gaskets are mainly used to seal flanges. These are connections with two flat sealing surfaces that are widely used in pipeline construction. The contact surface of the sealant is significantly larger here than with the O-ring.
Accordingly, the flat gasket lacks its circular profile cross-section. The flat gasket compensates for unevenness in the surfaces and seals them through the contact pressure achieved by a screw connection, for example.
Flat gaskets are used almost exclusively for static sealing applications. Together with the often aggressive environment in the chemical, pharmaceutical and food industries, this makes other sealing materials besides elastomers interesting.
Flat gaskets are also made of fibrous materials or PTFE (polytetrafluoroethylene). Metal-reinforced materials are also used for applications under high pressure. The manufacturing processes must not only take into account the different materials. Flat gaskets for special applications also take on very individual shapes and dimensions.
The production of conventional O-rings and flat gaskets is fundamentally different. Nevertheless, the high demands on precision, cost-effectiveness and short-term availability are common to both types of seal.
It must be possible to produce customized seals in a short time in order to avoid expensive machine downtime for the customer.
Two main processes are used to manufacture elastomer O-rings: compression molding and injection molding.
The compression process begins with the production of a blank using the extrusion process. In the next step, this is placed in a mold and pressed at high temperature to form a circular O-ring. After final deburring, the O-ring is ready. The process is particularly suitable for the production of small quantities of seals with large dimensions.
Advantages of compression molding:
For O-rings in standard sizes, which the market demands in high volumes, the injection molding process is more suitable.
Here, the starting material is given its final shape by automatic injection into the closed mold. After ejection, the O-ring is ready for further processing or sale. Here, too, high temperatures act on the material to achieve the vulcanization required for the elastic properties.
Advantages of injection molding:
Particularly large O-rings with common cord lengths of up to 3,000 mm require a less automated manufacturing process.
This takes into account the usually unfavorable relationship between demand volume and the cost of tool production. The most widespread method is impact vulcanization of extruded cords. The availability of the round cord in various diameters is the only limit to the design freedom.
For impact vulcanization, the specialist inserts the cord ends into special devices. There he provides them with an adhesive mixture.
Temperature and pressure now act to vulcanize the joints, i.e. to link the molecules. Due to the superior physical values of the vulcanized joint, the process has largely replaced the previously used bonding of O-rings.
Nevertheless, the shock is a weak point compared to the extruded line. The process is also responsible for the greater manufacturing tolerances compared to the other methods.
Advantages of impact vulcanization:
The starting material for flat gaskets is usually plate-shaped semi-finished products, which can consist of elastomers, fiber materials or multi-layer material combinations, depending on the application.
Flat gaskets in a variety of contours can be cut out of the sheets using punching, plotting or water jet cutting. The process selection is based on the number of pieces, delivery time and material.
To punch a flat gasket, the manufacturer needs a specific cutting tool that presses a hydraulic press into the sheet material. Due to the manageable tool costs, medium to large series can be processed economically with punching.
The tool production time is a disadvantage for customized flat gaskets. There is also a technical limitation: In the case of materials with a cellular and soft structure, the yielding can result in a concave cutting pattern.
Waterjet cutting is a particularly precise alternative. It is predestined for materials where mechanical and thermal processes reach their limits.
By cutting the sealing material with a water jet under high pressure, not only the smallest geometries and bores are produced within tight tolerances. Soft sealing materials can also be processed without deformation. Waterjet cutting can even produce simple three-dimensional seals.
Another advantage that makes the process particularly interesting for small series and one-off production is that a digital model of the flat gasket is sufficient to generate the commands for the CNC-controlled machine. Provided that the corresponding semi-finished product is available, production can begin immediately once the data has been provided.
For materials with a height of over 100 mm, the increasing scattering of the water jet begins to have a negative effect on precision. In the intended area of application, however, the process can produce workpieces with very thin walls and clean edges.
Plotting is also suitable for the production of small to medium quantities. Here, an electronically controlled oscillating knife separates the contour of the flat gasket from the semi-finished product. The absence of a specific tool means that set-up costs are low. One advantage over waterjet cutting is the size range.
Depending on the cutting table, very large seals of several meters in length can also be produced here. Depending on the material, the process is suitable for maximum material heights of up to 10 mm.
Whether a seal can reliably fulfill its task depends not only on the choice of material and the correct design of the sealing system, but also on the manufacturing standards. The experts at NH O-RING will advise you on all these issues and ensure that the seal meets your technical and economic requirements.
For seals with specific geometries or prototype parts, there is also a particular focus on rapid availability.
Whether flat gaskets as cut-to-size sheets, profile cords or molded parts, short reaction times are required here. We select the optimum manufacturing process so that you always receive the seals as quickly as possible.
“I am convinced that we should share our knowledge with the world. I hope I have been able to answer all your questions. If you have any further questions, please feel free to contact us at any time. We will be happy to help you.”
Lord of the O-rings
Author of the sealing academy
In this short article, we answer the 10 most important questions about the correct design of O-ring data sheets in a simple and understandable way.
In this short article, we answer the 10 most important questions about the correct design of O-ring grooves in a simple and understandable way.
In this short article, we answer the 10 most important questions about the correct storage of O-rings in a simple and understandable way.
You need to load content from reCAPTCHA to submit the form. Please note that doing so will share data with third-party providers.
More Information