Flange gasket
Flange gasket: Everything you need to know
Flange gaskets are an indispensable component in many industrial applications. They are used to seal the joints between two flanges to prevent liquids or gases from escaping.
The history of flange gaskets goes back a long way and reflects the development of the industrial revolution. Originally made from simple materials such as hemp, they have developed into highly sophisticated components with specific properties for various applications.
The function of flange gaskets is to ensure the integrity of piping systems. They play a key role in industries such as petrochemicals, mechanical engineering and power plants.
A crucial aspect of flange gaskets is their ability to withstand different pressure levels, chemical properties of the transported media and temperature conditions.
Important facts:
- Variety of materials: Modern flange gaskets are made from a variety of materials including rubber, plastic, metal and special composite materials.
- Areas of application: They are used in many branches of industry, from water and waste water treatment to aerospace technology.
- Safety relevance: Their importance for safety in industrial plants cannot be overestimated.
Due to their versatility and importance, flange gaskets are a fascinating subject that requires an in-depth understanding of their selection, application and maintenance.
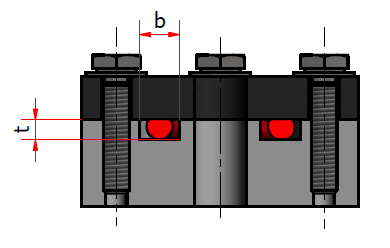
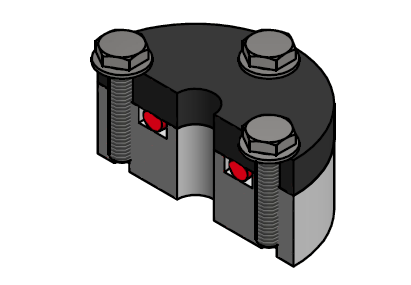
REQUEST O-RINGS QUICKLY AND EASILY?
Almost any dimension available
Offer received in record time
No minimum order quantities or minimum item values
One contact for all concerns
#1 Flange gasket - basics and importance
Flange gaskets, essential components in numerous industrial sectors, play a crucial role in ensuring the integrity and safety of piping systems.
These gaskets, which are fitted between two flanges, prevent the escape of liquids and gases, thus fulfilling a critical function in various applications.
History and development
The development of flange gaskets is closely linked to the progress of industrial technologies.
Originally made from simple materials such as hemp, they have evolved over time into complex and highly specialized components that can be made from a variety of materials.
Function and meaning
The main function of a flange gasket is to create a secure and tight connection between two pipe flanges.
This is particularly important in industries where safety and reliability are top priorities, such as petrochemicals, mechanical engineering and power plants.
Flange gaskets must be able to withstand various environmental conditions such as pressure, temperature and chemical stress.
Versatile applications
Flange gaskets are used in a wide range of applications, from water and wastewater treatment to aerospace. Their flexibility and adaptability to different conditions make them an indispensable component in many technical systems.
Safety aspect
The safety relevance of flange gaskets cannot be emphasized enough. They are crucial for preventing leaks, which can lead to environmental damage, operational downtime and, in extreme cases, serious accidents.
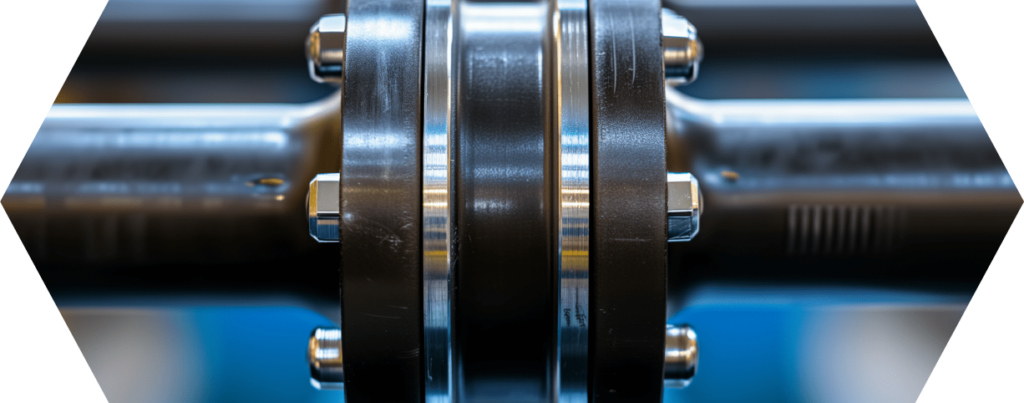
#2 Different types of flange gaskets and their properties
Special care must be taken when installing flange gaskets to ensure reliable sealing and operational safety.
Due to their specific properties and areas of application, some seal types require particularly careful installation and correct tightening. Here are some seal types that require particularly careful installation:
1. spiral wound seals
- Properties: Consist of a metallic winding strip and a softer filling material (often graphite or PTFE).
- Special feature: Tends to be damaged if handled incorrectly, as the soft filling material can be displaced by excessive pressure.
- Assembly: Requires even and controlled tightening to achieve uniform compression.
2. metallic flat gaskets (e.g. stainless steel, aluminum)
- Properties: Consist of rigid metals and are used in high pressure and high temperature applications.
- Special feature: Excessive tightening torque can lead to deformation and cracks.
- Assembly: Requires exact tightening torques to avoid overstressing.
3. PTFE seals
- Properties: Chemically resistant, but relatively soft and sensitive to over-compression.
- Special feature: PTFE can flow when overstressed and lose its sealing properties.
- Assembly: Careful tightening is required to ensure an adequate seal without material displacement.
4. non-asbestos-containing fiber gaskets
- Properties: Consists of compressed fiber materials, often with binders and fillers.
- Special feature: Can be easily damaged and lose their sealing ability if handled improperly.
- Assembly: Tighten evenly, taking into account the specific gasket thickness and materials.
5. rubber seals
- Properties: Elastic and flexible, but sensitive to excessive compression.
- Special feature: Excessive tightening can lead to deformation and loss of elastic properties.
- Assembly: Requires controlled tightening to maintain the elasticity of the seal.
For all of these gasket types, it is critical to follow the manufacturer’s instructions exactly and follow specific torque and installation instructions. The use of torque wrenches and a crosswise tightening method are generally recommended practices to ensure an even distribution of pressure on the gasket.
Seal type | Pressure range | Temperature range | Cost range | Areas of application |
---|---|---|---|---|
Metallic | High | High | Higher | Petrochemicals, power plants |
Non-metallic | Low | Low to medium | Lower | Food industry, water treatment |
Spiral wound | Medium to high | Medium to high | Medium to High | Oil and gas industry |
Rubber | Low | Low to medium | Lower | General industry |
Plastic | Low to medium | Medium | Medium | Chemical industry |
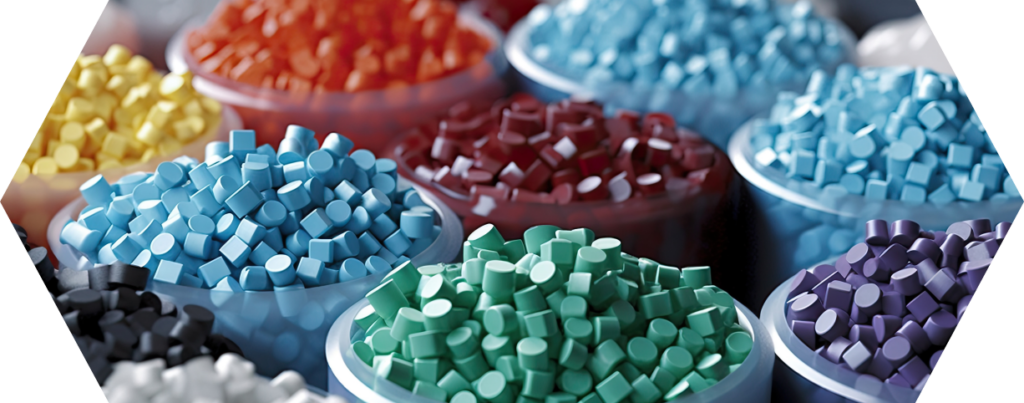
#3 Selection criteria for the perfect flange gasket
Selecting the right flange gasket is crucial for the safety and efficiency of industrial systems.
There are several factors that need to be considered when selecting a flange gasket to ensure that it is the best fit for the requirements of the application.
Material selection and chemical resistance
- Materials: The choice of the right material depends on the type of liquids or gases that are transported in the pipelines. For example, corrosive chemicals require a seal with high chemical resistance, such as PTFE.
- Chemical resistance: The seal must be resistant to the specific chemicals with which it comes into contact in order to prevent corrosion and material degradation.
Temperature and pressure resistance
- Temperature range: The seal must be suitable for the operating temperature range of the application. High-temperature applications, for example, require metallic or special high-temperature seals.
- Pressure range: The maximum pressure load to which the seal is exposed determines the choice of seal type. High-pressure applications require more robust, often metallic seals.
Flange type and size
- Flange compatibility: The gasket must exactly match the flange type and its size. This includes consideration of the flange geometry, bolt distribution and gasket fit.
- Sizing: Correct sizing is essential for sealing efficiency. A seal that is too large or too small can lead to leaks.
Checklist for the selection
- Determine the chemical compatibility: Make sure that the sealing material is compatible with the transported media.
- Determine the required temperature and pressure range: Select a seal that can withstand the operating conditions.
- Check the flange specifications: Ensure the exact fit and size for your specific flange.
- Take the ambient conditions into account: Ensure that the seal remains functional even under the prevailing ambient conditions.
By carefully considering these factors, you can ensure that you select the optimum flange gasket for your specific requirements. The right choice contributes significantly to the safety, efficiency and longevity of your systems.
Seal type | Materials | Temperature range | Pressure resistance | Costs | Main applications | Special properties |
---|---|---|---|---|---|---|
Metallic seals | Steel, stainless steel, other metals | Very high (up to 1,000°C) | Very high (over 250 bar) | Higher | Petrochemicals, power plants, high-temperature plants | High strength, durability, suitable for extreme conditions |
Non-metallic seals | Rubber, PTFE, graphite | Low to medium (up to 250°C) | Low to medium (up to 100 bar) | Lower | Food industry, water treatment, general industry | Flexibility, good chemical resistance, cost-efficient |
Spiral wound seals | Metallic winding strip, graphite/PTFE filling material | Medium to high (up to 700°C) | Medium to high (up to 200 bar) | Medium | Oil and gas industry, power generation, heavy industry | Adaptable to pressure fluctuations, robust, versatile applications |
Rubber seals | Nitrile, neoprene, EPDM | Low to medium (up to 150°C) | Low (up to 25 bar) | Lower | Sanitary, HVAC, vehicle construction | Elasticity, good sealing at low pressure, weather resistance |
Plastic seals (e.g. PTFE) | PTFE, Teflon | Low to high (up to 260°C) | Low to medium (up to 100 bar) | Medium | Chemical industry, pharmaceutical industry | Excellent chemical resistance, low friction, temperature resistant |
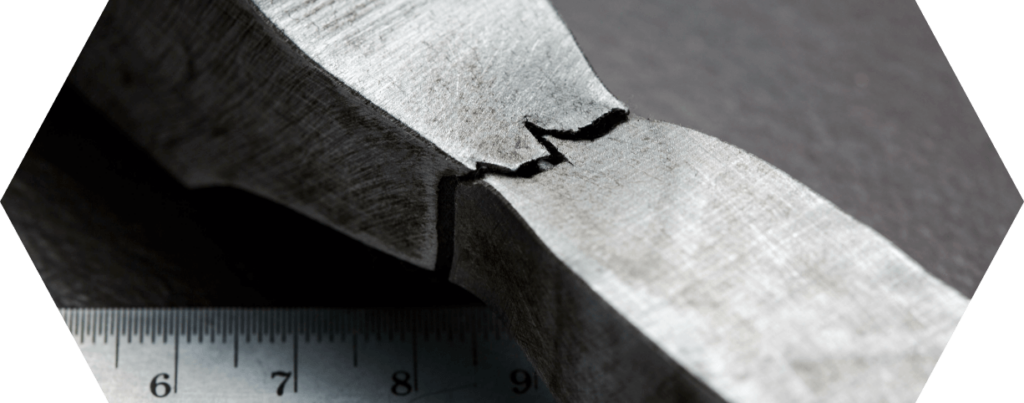
#4 Overview of the different flange types
Flanges are an essential part of many piping systems and are used to connect pipes, valves, pumps and other components.
There are various types of flanges that differ in their design, areas of application and specific properties. Here are some of the most common flange types, their distinguishing features and typical areas of application:
1. welding neck flanges
- Features: Have a long, tapered neck that is welded to the tube.
- Areas of application: Frequently used in high-pressure and high-temperature applications, such as in the petrochemical industry and in power plant construction.
- Advantages: Strong and tight connection, well suited for alternating loads.
2. weld-on flanges
- Features: Are slid over the pipe end and welded to it.
- Areas of application: Used in systems with lower pressure and temperature, such as water supply and heating systems.
- Advantages: Easier installation and lower costs than welding neck flanges.
3. blind flanges
- Features: Do not have a hole and are used to close the end of a pipe.
- Areas of application: Wherever pipes need to be sealed temporarily or permanently.
- Advantages: Allow easy access for inspections and repairs.
4. lap joint flanges
- Features: Consists of two parts, a ring and a flange, which are overlapped.
- Areas of application: Ideal for applications where frequent disassembly is required, such as in systems with corrosive media.
- Advantages: Easy replacement of the seal without moving the pipe.
5. Threaded flanges
- Features: Have an internal thread into which the pipe is screwed.
- Areas of application: In applications where welding is impractical, such as certain chemical processes.
- Advantages: Easy installation without welding.
6. Socket-weld flanges
- Features: The pipe is inserted into a recess in the flange and welded on.
- Areas of application: In smaller pipelines with high pressure requirements.
- Advantages: Good strength and leak resistance.
7. Orifice flanges
- Features: Specially designed for flow measurements, often connected to measuring instruments.
- Areas of application: In systems where flow measurement is important, such as in oil and gas pipelines.
- Advantages: Enable accurate measurements and easy maintenance of the measuring devices.
Each flange type has its own specific advantages and is selected according to the requirements of the respective application.
The selection depends on factors such as pressure level, temperature, medium, necessary strength and installation and maintenance requirements.
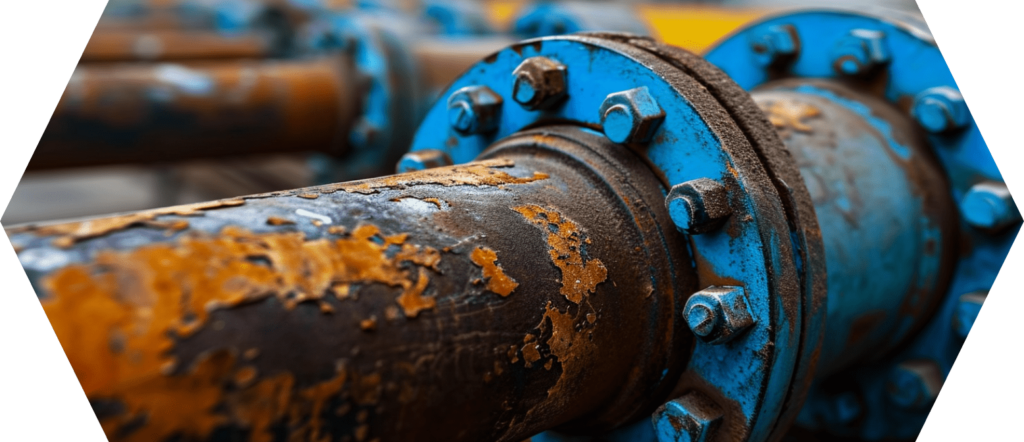
#5 Instructions for the installation and maintenance of flange gaskets
Correct installation and regular maintenance are crucial to ensure the functionality and longevity of flange gaskets.
In this chapter, we will look at the best practices for installing and maintaining these important components.
Correct dressing sequence
- A crosswise tightening sequence is important to ensure an even distribution of pressure over the entire seal.
- Tip: Start with the screw in the 12 o’clock position, then move to the 6 o’clock position, followed by 3 o’clock and 9 o’clock. Continue in this pattern until all screws have been tightened.
Avoidance of overtightening
- Overtightening the screws can damage the gasket, shorten its service life and even lead to leaks. This happens because the excessive pressure compresses or deforms the gasket material excessively.
- Tip: Use a torque wrench to tighten the screws to the torque recommended by the manufacturer. This ensures that you apply exactly the right amount of pressure.
Screws and their torques for flange gaskets
This table provides a guide to the common bolt sizes and their corresponding torques when installing flange gaskets.
The values may vary depending on the material of the screws and the specific application conditions. It is advisable to consult the manufacturer’s instructions for exact specifications.
Screw size | Torque for steel screws | Torque for stainless steel screws |
---|---|---|
M8 (8mm) | 20 – 25 Nm | 15 – 20 Nm |
M10 (10mm) | 40 – 50 Nm | 30 – 40 Nm |
M12 (12mm) | 70 – 85 Nm | 55 – 70 Nm |
M16 (16mm) | 160 – 200 Nm | 120 – 160 Nm |
M20 (20mm) | 300 – 350 Nm | 230 – 280 Nm |
M24 (24mm) | 450 – 500 Nm | 340 – 380 Nm |
M30 (30mm) | 800 – 900 Nm | 600 – 700 Nm |
Notes:
- Screw material: The torques vary depending on the material. Steel screws can generally absorb higher torques than stainless steel screws.
- Application conditions: The values given are general guidelines. Specific applications, such as high temperatures or corrosive environments, may require different torques.
- Gasket material: Also note the material of the flange gasket, as some materials react more sensitively to pressure and require an adapted torque.
- Manufacturer’s instructions: Always follow the gasket and screw manufacturer’s recommendations to ensure optimum performance and safety.
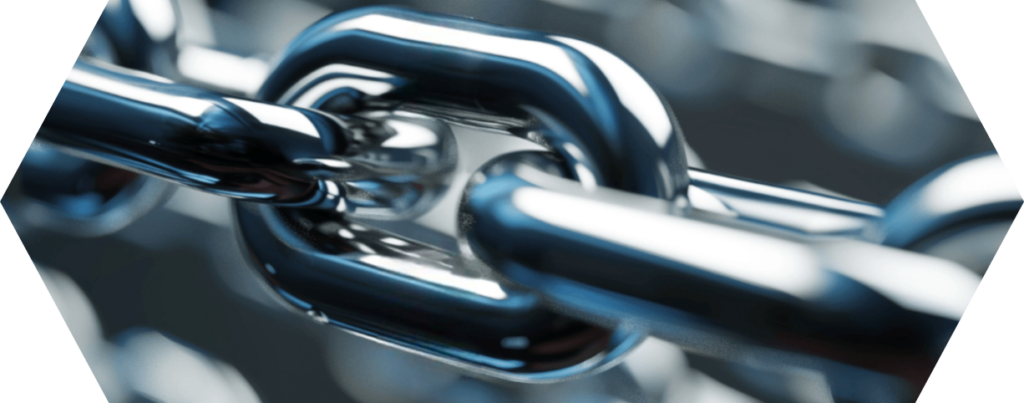
#6 Optimal maintenance of flange gaskets
Flange gaskets are crucial components in many industrial systems, and their correct functioning is essential for operational safety.
Nevertheless, various problems can occur in the course of their use. In this chapter, we will look at some common problems and point out solutions.
Leaks and their causes
- Causes of leaks: These can occur for a number of reasons, such as uneven flange surfaces, incorrect tightening of bolts, gasket wear or unsuitable gasket selection.
- Solutions: Ensure flanges are level and clean, tighten bolts evenly and to the correct torque, and select the correct gasket for the specific operating conditions.
Corrosion and material fatigue
- Corrosion: Chemical reactions, especially in aggressive environments, can lead to corrosion of the seal.
- Material fatigue: Long-term loads and temperature fluctuations can cause the material to fatigue.
- Countermeasures: Choose materials that are suitable for the chemical and physical conditions and carry out regular inspections to detect early signs of wear or damage.
In which industries should flange gaskets be serviced at least once a year? We have compiled some examples below.
Petrochemical industry: In refineries and chemical processing plants where flange gaskets are often exposed to high temperatures, corrosive chemicals and high pressure.
Power plants: Especially in power plants that work with steam or high temperatures, such as coal, gas or nuclear power plants, where a failure of the seals can lead to serious operational disruptions or safety risks.
Offshore oil and gas platforms: In this environment, the seals are exposed to extreme weather conditions, salt water and high pressure, which makes regular maintenance essential.
High-pressure gas lines: Here, the integrity of the seals is crucial to prevent gas leaks, which can lead to environmental damage or even explosion hazards.
Pharmaceutical and food industry: In these industries, the reliability of the seals is important to prevent contamination and meet strict hygiene standards.
Biotechnological and medical systems: Similar to the food and pharmaceutical industries, where sterility and contamination prevention are crucial.
Critical water treatment plants: In plants that treat drinking water or waste water, where leaks can lead to environmental pollution or health risks.
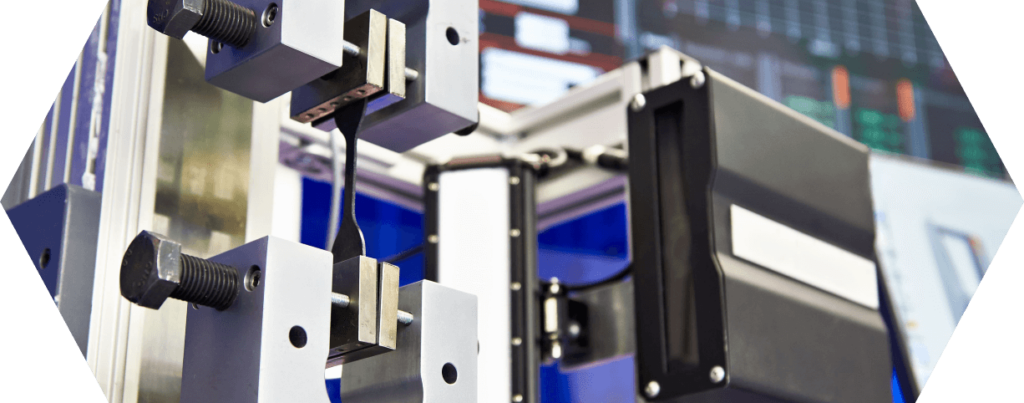
#7 Use of O-rings as a flange seal
O-rings are a popular type of gasket used in various applications, including as flange gaskets.
They differ from flat gaskets in terms of design and area of application. Here are the reasons for using O-rings, the differences to flat gaskets and their advantages and disadvantages:
Why are O-rings used?
- Flexibility and versatility: O-rings can adapt to different surfaces and shapes.
- Cost efficiency: They are generally cheaper to manufacture and use than many other types of seal.
- Easy installation and maintenance: O-rings are easy to install and require little maintenance.
- Reliability: Provide an effective seal under a wide range of pressure, temperature and media conditions.
When do you use flat gaskets and when do you use O-rings?
- Flat gaskets:
- Used for larger flange connections, especially when a larger sealing surface is required.
- Suitable for applications in which the seals are exposed to high pressures and temperatures.
- Often used in industrial plants and in the petrochemical industry.
- O-rings:
- Used in smaller or complex shaped applications where a compact and flexible seal is required.
- Ideal for dynamic applications where parts move relative to each other.
- Frequently used in the automotive industry, in hydraulic/pneumatic systems and in consumer electronics.
Advantages and disadvantages
O-rings
- Advantages:
- High tightness for a wide range of applications.
- Resistant to many chemicals and temperature changes.
- Simple installation and low space requirement.
- Disadvantages:
- Not ideal for applications with extremely high pressures or temperatures.
- Can be damaged by sharp edges or rough surfaces.
- Requires precise groove dimensions and surface quality.
Flat gaskets
- Advantages:
- Suitable for high pressures and temperatures.
- Can compensate for major irregularities in the flange surfaces.
- Wide range of materials for different requirements.
- Disadvantages:
- Can be more complicated to install.
- Larger space requirement and potentially higher costs.
- May cause leaks if used incorrectly.
In summary, the choice between O-rings and flat gaskets depends on the specific requirements of the application, including size, pressure, temperature and the type of liquids or gases to be sealed.
O-rings offer an efficient solution for many standard applications, while flat gaskets may be more suitable for more demanding, industrial applications.
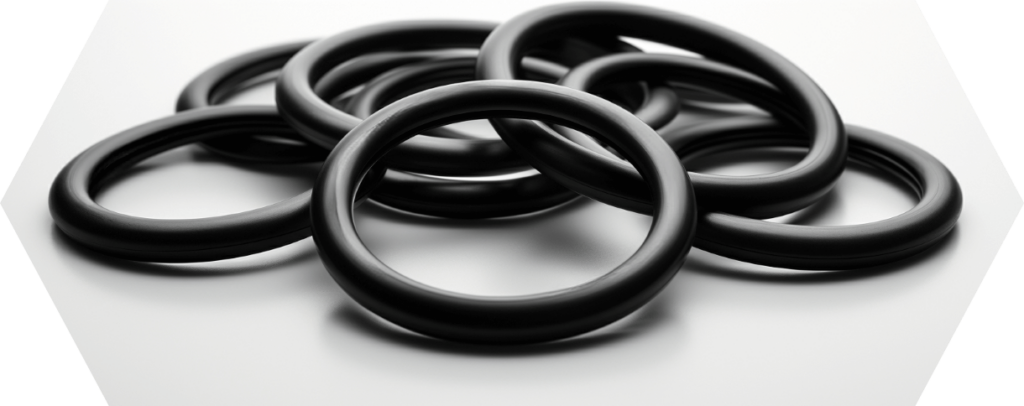
#8 Future trends and innovations in flange gasket technology
In Industry 4.0, which is characterized by digitalization, networking and the use of smart technologies, flange gaskets are also undergoing a remarkable transformation.
They are becoming intelligent and can collect and communicate data in real time. Here are some key points on how flange gaskets work in Industry 4.0 and the benefits they offer:
Functions of flange gaskets in Industry 4.0
Integration of sensors:
- Modern flange gaskets can be equipped with sensors that monitor various parameters such as pressure, temperature and possibly chemical composition in real time.
- These sensors can detect changes in seal performance at an early stage, which enables timely maintenance.
Data transmission and analysis:
- The collected data is sent to a central system where it can be analyzed to identify patterns and potential problems.
- This analysis can be used to predict maintenance requirements or to detect operating anomalies.
Networking with other system components:
- Flange gaskets can be part of a networked system that includes all components of a plant, enabling comprehensive monitoring and optimization of operations.
Concrete advantages of flange gaskets in Industry 4.0
Improved maintenance strategies:
- By collecting precise operating data, maintenance work can switch from a reactive to a proactive approach based on actual wear and performance.
- This reduces unplanned downtimes and extends the service life of the seals.
Increased security:
- Early detection of problems such as leaks or material fatigue helps to minimize potential safety risks.
- This is particularly important in critical and hazardous applications such as in the chemical or petrochemical industry.
Energy efficiency and resource conservation:
- By optimizing operation and avoiding leaks, energy consumption can be reduced and the use of resources minimized.
- By optimizing operation and avoiding leaks, energy consumption can be reduced and the use of resources minimized.
Data-based decision making:
- The availability of detailed operating data makes it possible to make well-founded decisions about the maintenance and operation of the system.
- In the long term, this can help to optimize overall operations and reduce operating costs.
Integration into overall systems:
- The ability to integrate sealing data into larger operational management systems enables a holistic view and control of the production process.
Overall, smart flange gaskets in Industry 4.0 enable greater operational efficiency, improved safety and more sustainable production through advanced monitoring and data-driven maintenance approaches.
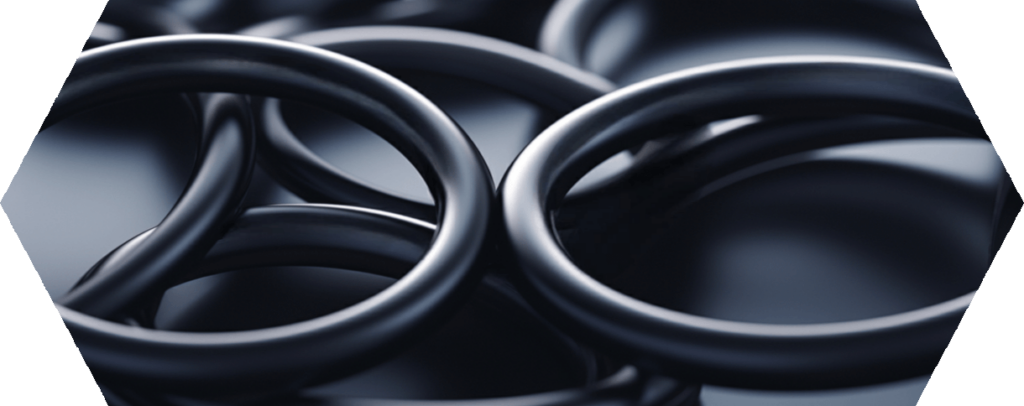
#9 FAQ section: Flange gasket
Finally, some answers to frequently asked questions.
#9.1 What is a flange gasket and what is it used for?
A flange gasket is a special gasket that is used between two flanges in piping systems to ensure a secure and leak-free connection.
They are indispensable in many industries, such as petrochemicals, mechanical engineering and power plants, to maintain the integrity of systems by preventing the escape of liquids or gases.
#9.2 What materials are used for flange gaskets?
Flange gaskets are made from a variety of materials, including rubber, PTFE (polytetrafluoroethylene), metals such as steel and stainless steel, as well as special composite materials.
The choice of material depends on the specific application, including the temperature and pressure conditions as well as the chemical compatibility with the transported media.
#9.3 How to choose the right flange gasket
Selecting the right flange gasket requires consideration of several factors: the material, which must be compatible with the transported media, the temperature and pressure range of the application, the flange size and type as well as the operating conditions.
Correct selection ensures efficient and safe operation of the piping system.
#9.4 How important is the maintenance of flange gaskets?
The maintenance of flange gaskets is crucial for the longevity and safety of piping systems.
Regular inspections help to detect wear, damage or leaks at an early stage. Maintenance includes checking the condition of the flanges, tightening the screws evenly and replacing the gasket if necessary.
#9.5 What role do spiral wound seals play in the industry?
Spiral wound gaskets, consisting of a metallic winding strip and a softer filler material, are particularly important in industries that work with high pressures and temperatures, such as the oil and gas industry.
They offer excellent adaptability to changing operating conditions and are known for their reliability under regular pressure fluctuations.
#9.6 How is flange gasket technology developing?
Flange gasket technology is constantly evolving, with a focus on new materials, improved manufacturing techniques such as 3D printing, sustainability and integration into smart industrial systems.
Innovations such as smart seals with integrated sensors provide real-time data and enable predictive maintenance, which increases the safety and efficiency of industrial plants.
#9.7 Who are three manufacturers of flat gaskets and blanks from Germany?
#9.8 What is the difference between flange seal, piston seal and rod seal?
Flange gasket
- Intended use: Flange gaskets are used to seal the joint between two flanges in piping systems.
- Function: They prevent the escape of liquids or gases at the connection point.
- Properties: These seals must be able to withstand pressure, temperature fluctuations and sometimes corrosive environments. They can be made of different materials such as rubber, PTFE, metal or graphite.
- Fields of application: Used in a wide range of industries such as oil and gas, petrochemicals, water treatment and the food industry.
Piston seal
- Intended use: Piston seals can be found in hydraulic or pneumatic cylinders. They seal the space between the cylinder housing and the moving piston.
- Function: They prevent fluid (hydraulic oil, air) from seeping through from one side of the piston to the other, thus enabling effective power transmission.
- Properties: These seals must be resistant to pressure, abrasion and possibly high temperatures. Often made of elastomers, PTFE or other polymer materials.
- Areas of application: Frequently used in construction machinery, automotive hydraulic systems and in the manufacturing industry.
Rod seal
- Intended use: Rod seals are used in hydraulic and pneumatic cylinders, similar to piston seals, but they seal the area around the cylinder rod.
- Function: Prevent liquids from escaping along the cylinder rod to the outside and at the same time protect the cylinder from external contamination.
- Properties: Must be able to withstand pressure, dynamic movement, abrasion and possibly environmental factors. Made from materials such as polyurethane, nitrile rubber or PTFE.
- Areas of application: Use in hydraulic presses, elevators, agricultural machinery and many other hydraulically or pneumatically operated systems.
“I am convinced that we should share our knowledge with the world. I hope I have been able to answer all your questions. If you have any further questions, please feel free to contact us at any time. We will be happy to help you.”
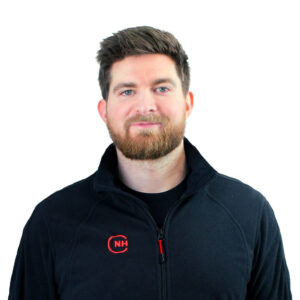
Lord of the O-rings
Author of the Sealing Academy