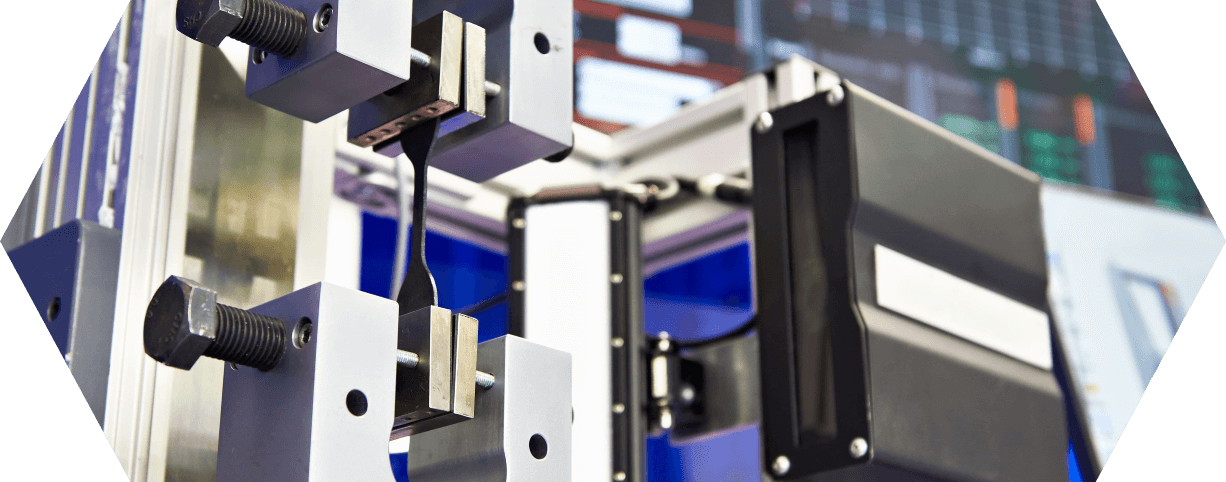
10 questions: O-ring data sheets
In this short article, we answer the 10 most important questions about the correct design of O-ring data sheets in a simple and understandable way.
Users hardly notice a well-functioning seal: it performs reliably over a long period of time.
Once a seal comes into focus, this usually has unpleasant consequences. Because if a machine comes to an unscheduled standstill due to a leak, there is a risk of high sales losses.
This risk is very high for highly networked production systems. These are particularly prevalent in the chemical, pharmaceutical and food industries, where O-rings also encounter challenging operating conditions. Particularly high or cold temperatures, aggressive media and high pressures put the seals to the test.
Machine failures are not the only problem: other potential consequences of a failed seal are more difficult to quantify. These include recalls of products that have been produced under undetermined production conditions or environmental damage caused by leaks of hazardous substances.
A look at the most common causes of damage to O-rings shows that our customers can avoid many failures in practice with simple measures. In this article, we provide an overview of the main reasons for O-ring failure and how these can be avoided.
Every practitioner knows that if you want to increase the reliability of waterproofing, you should look for the cause in the event of damage.
A reason for the seal defect can often be identified. In more complex cases, the interaction of several causes can lead to a leak, but here too a damage analysis enables the experts to at least rule out uninvolved factors as the cause.
Assembly, installation space and operating conditions stress the O-ring during use. To check whether the engineers have selected the right solution for the sealing task, all these factors need to be scrutinized.
In addition, the sealing elements can be exposed to undesirable influences during manufacture and storage until they are used. An expert eye and experience in dealing with seals often provide valuable information about the causes of damage.
In many cases, this eliminates the need for time-consuming and expensive physical and chemical tests in the laboratory. Depending on the application, however, detailed analysis measures such as spectroscopy or chromatographic methods may also be necessary. However, the time for this is usually only found afterwards, as the maintenance technician has to act quickly to minimize the interruption to production operations.
In any case, it is important to draw the right conclusions from the test results in order to improve the performance of the seal in the future. This is where the exchange of experience with O-ring experts from manufacturers and specialist dealers pays off.
From working with customers from various industries in application support, they are familiar with many cases of damage and suitable countermeasures for the sealing system.
Experts divide the causes of seal defects into four categories.
They distinguish between damage caused by the effects of process media, the weakening of the material due to temperature and ageing, manufacturing defects and impermissible physical stresses.
An unsuitable combination of sealing material and medium can lead to severe swelling of the O-ring. This happens when the medium penetrates the sealing material.
In the opposite case, shrinkage is also possible. The medium causes this by dissolving compound components from the material of the O-ring. Media exposure is not limited to ongoing operation.
Unsuitable assembly oils or greases can chemically damage the O-rings before they are used. Both phenomena result in a change in the material properties. As a result, rubber elasticity, the very property that makes elastomers so suitable for sealing applications, suffers.
Cracks and embrittlement often occur. The effect of the media can also manifest itself in the form of permanent deformation. Another indication of media exposure is the feel of the O-ring. This is because under the influence of the media, the possibly. the surface structure and the O-ring feel a little “muddy”.
This all happens when O-rings come into contact with media for which they are not suitable. This does not always have to be because the designer has disregarded the resistance list issued by the seal manufacturer.
Operating conditions that deviate from the original planning or simply a mix-up in the bearing can also be responsible for the impermissible pairing of O-ring and media. The widely used O-rings made of FFKM (perfluoro rubber) are a good example: They are known for their particularly wide range of applications.
However, in contact with hot water above 150 degrees, common material formulations show severe deformation after just a few weeks, causing the seal to fail.
Solution approach for damage caused by media exposure
Cracking or embrittlement is a common type of damage in the temperature and ageing category. This is often due to the upper continuous temperature for which the seal is approved by the manufacturer being significantly exceeded.
It is important to note that the temperature resistance specified on a data sheet has been tested in unpressurized and media-free (air) applications.
Accordingly, it must be taken into account in real applications that pressure and medium have a negative effect on the temperature resistance of a material. In most cases, the failure of a seal due to excessive temperature exposure is easy to identify because the feel of the O-ring changes significantly. This is because the O-ring feels brittle and sooty and, in extreme cases, can also break apart under a little pressure.
The cause of damage, ageing, only includes the effect of substances contained in the ambient air and heat and can therefore be distinguished from damage caused by the effects of media.
Dhe sun’s radiation can cause permanent damage to O-rings, resulting in long-term seal failure. For example, the reaction of O-rings made of NBR (acrylonitrile butadiene rubber) with ozone from the ambient air causes irreparable damage to the material within a few days.
The deep cracks, known as light cracks, always occur perpendicular to the direction of the stress acting on the O-ring when installed. This can be remedied, for example, by coating the O-ring or changing to an ozone-resistant rubber.
Solution approach for thermal loads
Incorrect installation of O-rings is by far the number one reason why an O-ring seal fails after some time.
Incorrect assembly includes almost all defects that occur without prior damage to the network structure of the sealing element. Only the inappropriate treatment of the O-ring during manufacture does not fall into this category.
Instead, the focus of the error lies in the installation process, the design of the installation space and insufficient or excessive compression. It is encouraging to note that although these damages occur most frequently, they are also the easiest to avoid with appropriate training.
It is often the lack of lubrication during installation and missing or unsuitable installation aids that cause permanent damage to the O-ring. Among other things, this is due to impermissibly high deformation forces caused by the necessary expansion of external O-rings.
Excessive twisting also damages the O-ring, but can hardly be avoided when fitting large seals with a thin cord. The error may also have occurred in the design department.
Sharp-edged groove recesses, inappropriate pressing or excessive diameter play are common causes of damage.
A frequently observed phenomenon is that the O-ring is pressed into the sealing gap due to incorrectly designed grooves or excessive pressure and is peeled off after some time. Extrusion of the O-ring is one of the most common causes of O-ring failure and can be easily recognized by the peeled rubber material.
Solution approach for physical stress
Similar to O-rings damaged by assembly errors, sealing elements with manufacturing defects often fail after a fraction of the expected service life. Both causes of damage are therefore difficult to separate.
A key indication of a manufacturing defect is if the limit dimensions for O-rings specified in DIN ISO 3601 are exceeded. Cracks and their precursors, radial flow lines, are also clear deviations from the target condition of an unused O-ring.
Peroxide cross-linked materials such as FKM are significantly more prone to faults than NBR in this respect. In addition, there is under-vulcanization, in which the molecular cross-links in the elastomer do not fully develop. The result is the undefined formation of the desired rubber-elastic property.
Quantitative studies show that mechanical and physical factors influencing the seal are most frequently responsible for its failure.
This is followed by errors from the temperature and ageing category. Incompatibility of the gasket material with the process media and manufacturing errors, on the other hand, are much less likely to be the cause of failure.
In view of the fact that assembly-related damage and inadequately designed installation spaces dominate the most common group of faults, one thing is clear: if users attach greater importance to an error-free assembly process and conscientious design and manufacture of the groove for the sealing ring, they can extend the service life of many seals.
The training of employees in the assembly and design department contributes to this, as does the provision of suitable assembly equipment and auxiliary materials.
The consequences of a failing seal are often grossly disproportionate to its procurement costs. This is precisely why conscientious supplier selection pays off.
By working with NH Dichtungsservice, users not only gain access to a flexible supplier of high-quality seals made from a wide range of materials. You also gain access to the expertise of experienced employees who work with customers to design the right seal for their individual application.
“I am convinced that we should share our knowledge with the world. I hope I have been able to answer all your questions. If you have any further questions, please feel free to contact us at any time. We will be happy to help you.”
Lord of the O-rings
Author of the sealing academy
In this short article, we answer the 10 most important questions about the correct design of O-ring data sheets in a simple and understandable way.
In this short article, we answer the 10 most important questions about the correct design of O-ring grooves in a simple and understandable way.
In this short article, we answer the 10 most important questions about the correct storage of O-rings in a simple and understandable way.
You need to load content from reCAPTCHA to submit the form. Please note that doing so will share data with third-party providers.
More Information