O-RING applications | EXPLANATION SIMPLY EXPLAINED
Everything you need to know about O-ring sealing types
O-rings are very versatile sealing elements.
Thanks to their round shape and elastic properties, they can seal technical components against each other in various constellations. O-rings are also suitable for separating the inside of a machine or system from the environment.
Regardless of pressure, certain media or temperatures: correctly installed O-rings reliably maintain the conditions inside the sealing system. In order to fulfill this task, technicians must take the specific requirements of the respective application into account when designing a seal.
We characterize the applications and summarize what is important.
REQUEST O-RINGS QUICKLY AND EASILY?
Almost any dimension available
Offer received in record time
No minimum order quantities or minimum item values
One contact for all concerns
#1 These O-ring applications are available
The most important distinction between different O-ring applications concerns the direction of compression. Seen from the installation direction, the cross-section of O-rings can be pressed axially or radially.
Compression is the elastic deformation of the O-ring between the two sealing surfaces.
It is necessary in order to close the sealing surfaces cleanly. The sealing element adapts to any unevenness in the workpiece surfaces thanks to the pressing process. Even components positioned slightly off-center in relation to each other are securely sealed by this pretensioning of the O-ring.
This is also important because the positioning of the components can change at any time due to external influences such as an impact.
Axial and radial compression are the two categories of common O-ring applications. They can be subdivided even further and have specific requirements in terms of design, O-ring material selection and many other parameters.
#2 Sealing type: Flange seal
The flange seal is an O-ring application in which the sealing element is used purely statically.
The sealing surfaces between which the O-ring is pressed rest here. It is therefore a rigid connection, but is usually designed to be detachable with screws. Flange gaskets are characterized by compression in the axial direction.
The deformation force therefore acts in the installation direction of the O-ring. Examples of flange gaskets include pipe connections or inspection openings. Reducing pieces for the pipe cross-section are also secured with a flange seal.
1. Materials
In principle, many elastomer materials are suitable for use as flange gaskets. Because assembly requires hardly any stretching, materials with low elasticity can also be used without any problems.
In the chemical and food industries, for example, the rigid but extremely media-resistant PTFE
is a very common material for flange gaskets. EPDM is often used in sanitary and heating installations.
2. Groove design
When designing the groove of flange gaskets, it should be noted above all that the pressure direction determines the installation position of the O-ring. With internal pressure, the sealing element should be in contact with the outer edge of the groove – and vice versa with external pressure. The pressure thus increases the sealing effect.
3. Assembly
The installation of flange gaskets is usually unproblematic thanks to the easily accessible grooves. During installation, the O-ring can be inserted into the groove from the front without being excessively deformed.
With external pressure, only a slight expansion of the inner diameter is required; with internal pressure, minimal compression of the outer diameter is necessary.
4. Fields of application
The flange seal with O-rings is always used where round components are to be statically connected to each other. Flanges and the corresponding gaskets secure joined pipes, close end points with covers and integrate inspection openings.
#3 Sealing type: Piston seal
With the piston seal, the O-ring is pressed radially. The deformation is therefore orthogonal to the installation direction.
Another criterion characterizes the piston seal. Here is the installation groove is located in the inner part of the seal, i.e. the piston. The pressing takes place on the sealing surface of the outer part.
Piston seals are therefore also referred to as externally sealing. They are generally cheaper than rod seals, as the installation groove in the inner part is easier to produce using machining processes.
1. Materials
The piston seal can be used both statically and dynamically. While the load on the O-ring due to friction is particularly relevant in dynamic applications, it is not critical in stationary sealing applications.
With one exception: with stationary seals, changing pressure conditions can cause strong friction.
The O-ring then moves alternately from one groove flank to the other to be located on the side facing away from the pressure. With dynamic seals, on the other hand, the sealing surfaces regularly move against each other and thus also against the O-ring. The most common examples of this are hydraulic and pneumatic applications.
The dynamic application of O-rings as piston seals requires particularly friction-resistant sealing materials. Abrasion-resistant materials include NBR, PTFE, EPDM and FKM.
2. Groove design
The groove design should also take dynamic use into account. A significantly reduced compression must be provided so that the friction is limited to the technically necessary minimum.
This protects the O-ring from premature wear and increases its durability. Higher surface qualities of the sealing surfaces also contribute to durability.
In general, when designing the groove, it is crucial to set the target dimension for the grouting via the depth of the groove.
The width of the groove is determined depending on the expected swelling behavior and the pressure conditions. The groove must be wide enough to allow the O-rings to increase in volume when in contact with certain media.
On the other hand, it should not be excessively large, as the O-ring can migrate under changing pressure conditions. The inside diameter of the O-ring is selected to be slightly smaller than the groove base diameter. In general, an elongation of the O-ring of 1 to 6 percent is recommended.
In addition to the actual groove, insertion chamfers must also be provided in the outer part of the piston seal. They help to gently position the piston and cylinder correctly in relation to each other during assembly.
Without the insertion chamfers, there is a risk of the O-ring being crushed by a hard workpiece edge.
3. Assembly
When fitting a piston seal, the O-ring must be stretched. Depending on the elasticity of the O-ring material, it should be assessed whether critical elongation can occur during assembly.
Careful heating and the use of installation aids can make installation more convenient and safer. Mounting cones ensure even stretching and make it easier to drive over edges.
4. Fields of application
This O-ring application is particularly prevalent where two round components are inserted into each other. First and foremost are the pistons and cylinders. These can be static and dynamic sealing cases.
#4 Sealing type: Rod seal
Rod seals have the direction of compression in common with the piston seal. However, the installation space for the O-ring in the rod seal is located in the outer part or cylinder.
When designing, the O-ring is selected so that it snaps into the installation groove in a slightly compressed state. The compression is then made on the sealing surface of the inner part or piston.
It results from the gap dimension between piston and cylinder, cord thickness of the O-ring and the depth of the installation groove. Rod seals are internally sealing.
1. Materials
As with the piston seal, the individual load profile determines which O-ring materials are suitable.
Taking friction, process media, temperatures and pressure into account, the design engineers select the O-ring quality with the best fit. Economic efficiency is also taken into account.
2. Groove design
When designing the groove for a rod seal, the required defined compression on the outside diameter must be achieved in addition to the compression.
The compression should be between 1 and 3 percent for O-rings with an inner diameter of less than 250 mm and up to 5 percent for larger dimensions. Insertion chamfers on the inside make assembly a reliable process.
3. Assembly
O-rings must be compressed in order to install them in a rod seal. A particularly gentle procedure is important here so that the sealing element is not damaged.
The best way to install the seal is to first place one half of the seal in the groove before carefully pushing the remaining part into place with a tool.
4. Fields of application
Dynamically stressed rod seals are mainly used in hydraulics and pneumatics. There they are secured with support rings at high pressures.
However, not only O-rings are used for this application, but also special asymmetrically shaped lip seals. External sealing systems are often preferred to rod seals because they are cheaper to manufacture.
“I am convinced that we should share our knowledge with the world. I hope I have been able to answer all your questions. If you have any further questions, please feel free to contact us at any time. We will be happy to help you.”
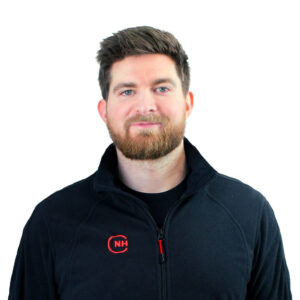
Lord of the O-rings
Author of the sealing academy