FEP (fluoroethylene propylene)
FEP material: Everything you need to know
Fluoro-ethylene propylene (FEP) is a high-performance fluoropolymer that is valued in modern industry for its remarkable properties.
As a member of the fluoropolymer family, FEP offers exceptional chemical resistance, outstanding thermal stability and excellent electrical insulation properties.
This combination makes it an ideal material for a wide range of applications, from aerospace engineering to electronics and medical technology. FEP is particularly valuable in environments that require high reliability under extreme conditions, as it can withstand temperatures from -200°C up to 200°C and is inert to almost all chemicals.
Its ability to deliver clear and flexible products expands its use in applications that require transparency or precise fluid flow. The development and use of FEP reflects the pursuit of materials that improve performance and safety in critical applications.
Feature | Property Description | Application examples |
---|---|---|
Chemical resistance | Resistant to most chemicals and solvents. | Chemical processing, laboratory equipment |
Thermal stability | Resistant in a wide temperature range (-200°C to 200°C). | Aerospace, electronics |
Electrical insulation | Excellent dielectric properties, ideal for electrical applications. | Insulation of cables and wires, electronic components |
Mechanical strength | Withstands mechanical stresses, even under extreme conditions. | Industrial seals, hoses |
Transparency | Clear and transparent, enables visual inspections. | Medical devices, safety applications |
Processability | Easier to mold and process than other fluoropolymers. | Complex components, custom-made products |
Environmental compatibility | Research focuses on more environmentally friendly production and improved recyclability. | Sustainable development projects |
REQUEST O-RINGS QUICKLY AND EASILY?
Almost any dimension available
Offer received in record time
No minimum order quantities or minimum item values
One contact for all concerns
#1 What is FEP?
Fluoro-ethylene propylene (FEP) is a high-performance fluoropolymer that has proven itself in numerous industrial sectors thanks to its exceptional properties.
In this chapter, we answer essential questions about FEP to give you a deeper understanding of this material.
The basics of fluoro-ethylene propylene
What makes FEP unique? FEP is a copolymer resulting from the polymerization of tetrafluoroethylene (TFE) and hexafluoropropylene (HFP). It is characterized by its extraordinary chemical resistance and thermal stability. Its ability to withstand extreme temperatures while providing excellent electrical insulation makes it indispensable in many technical applications.
Why is FEP preferred in the industry?
- Chemical resistance: FEP is virtually immune to many chemicals and solvents, making it ideal for use in chemical processing.
- Temperature resistance: It can withstand temperatures from -200°C to 200°C, making it suitable for extreme environments.
- Electrical properties: With its excellent dielectricity, FEP is a preferred choice in the electronics industry.
Historical background of FEP
How has FEP developed? The development of FEP began in the 1960s to meet the need for materials with special properties such as heat resistance and chemical stability. Since then, FEP has played a transformative role in various industries, from aerospace to medical technology.
What milestones have shaped the history of FEP?
- 1960s: Market launch of FEP.
- 1970s: Expansion of use to electrotechnical and medical applications.
- Present: Continuous further development for technologically advanced applications.
FEP has proven to be indispensable in areas that require high performance and reliability. Its unique properties contribute significantly to innovation in modern industry.
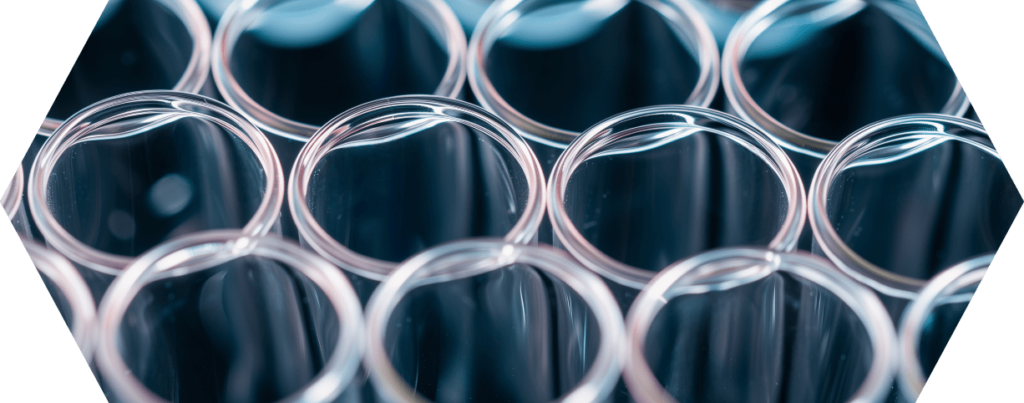
#2 Key properties of FEP
In this chapter we focus on the specific properties of FEP and how these contribute to its versatile applications in industry.
The unique properties of fluoro-ethylene propylene
FEP, known for its exceptional physical and chemical properties, plays an important role in various technical fields. But what makes it so special?
What are the key properties of FEP?
- Chemical resistance: FEP resists aggressive chemicals, making it ideal for coatings in chemical processing.
- Thermal stability: It retains its properties over a wide temperature range, making it indispensable for high-temperature applications.
- Electrical insulation: With its excellent dielectric properties, FEP is in demand in the electrical and electronics industry.
Diverse applications for fluoro-ethylene propylene
In which areas is FEP used? FEP is used in a number of industries that benefit from its durability and reliability.
- In electronics: As insulating material in cables and wires, especially in high-temperature environments.
- In the chemical industry: FEP is used for lining reaction vessels and pipelines to resist chemical attack.
- In the medical field: Due to its non-toxicity and sterilizability, it is ideal for medical devices and implants.
- In the aerospace industry: Used for insulated wires and seals that are exposed to extreme conditions.
FEP in the industry: an overview
What industrial applications does FEP have?
- Cable and wire industry: FEP is used in the manufacture of high-performance cables and wires due to its excellent insulating properties and heat resistance.
- Processing industry: It is used in the manufacture of semiconductor components and in chemical processing where high purity and chemical resistance are required.
- Aerospace: FEP is used for seals and insulations that have to function under extreme conditions.
Here are a few interesting short questions answered quickly and simply:
What role does FEP play in the semiconductor industry?
FEP is valued in the semiconductor industry for its chemical resistance and purity, ideal for wafer carriers and insulation.
How can FEP-sheathed cables be used in extreme environments?
FEP-sheathed cables are suitable for extreme environments thanks to their high temperature and chemical resistance as well as UV stability.
What innovative applications are there for FEP in medical technology?
FEP is used in medical technology for biocompatible devices, catheters and implants due to its non-toxicity and sterilizability.
How do fillers influence the properties of FEP?
Fillers such as glass or carbon improve FEP’s mechanical strength and thermal stability, thus extending its industrial applicability.
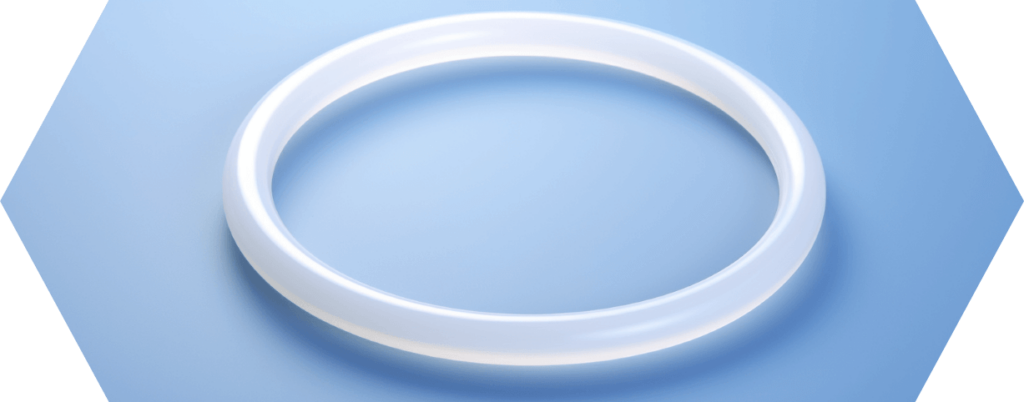
#3 FEP manufacturing process: a detailed look
In this chapter, we examine the process of manufacturing and processing FEP to ensure a comprehensive understanding of how it is produced.
Processing techniques for fluoro-ethylene propylene
FEP production is a specialized process that requires precise control and expertise. But how exactly is FEP manufactured and processed?
How is FEP produced?
- Polymerization: FEP is produced by copolymerizing tetrafluoroethylene (TFE) and hexafluoropropylene (HFP) in an emulsion polymerization process.
- Extrusion: The resulting pellets are then extruded into the desired shape, which gives FEP its versatility.
Quality control and standards in FEP production
How is the quality of FEP ensured? Quality control is a crucial aspect of FEP production. This includes:
- Rigorous testing: FEP materials undergo a series of tests to ensure that they meet the required specifications, particularly in terms of thermal stability and chemical resistance.
- International standards: Production follows internationally recognized standards to ensure consistency and reliability. This includes ISO standards and specific industry standards, depending on the area of application.
There are several renowned manufacturers worldwide for the production of FEP (fluoro-ethylene propylene) as a basic raw material. The best known include:
-
DuPont: DuPont is one of the leading manufacturers of FEP and offers a variety of FEP grades for different applications. Their product “Teflon™ FEP” is widely used in the industry.
-
Daikin Industries: As a global company, Daikin produces a range of fluoropolymers, including FEP, known for their high quality and performance.
-
3M (Dyneon™): 3M offers a wide range of fluoropolymers through its Dyneon™ brand, including FEP for various industrial applications.
-
Solvay: Solvay produces FEP under the brand name “Hyflon®” and is known for its innovative fluoropolymer solutions for demanding applications.
-
AGC Chemicals: AGC offers Fluon® FEP, which is valued in various industries for its outstanding chemical resistance and thermal stability.
These manufacturers are known for their ability to produce high-quality FEP that meets the high demands of various industrial and technological applications.
DuPont | Teflon® | United States |
Daikin Industries | Neoflon® | Japan |
3M | Dyneon® | United States |
Solvay | Hyflon® | Belgium |
AGC Chemicals | Fluon® | Japan |
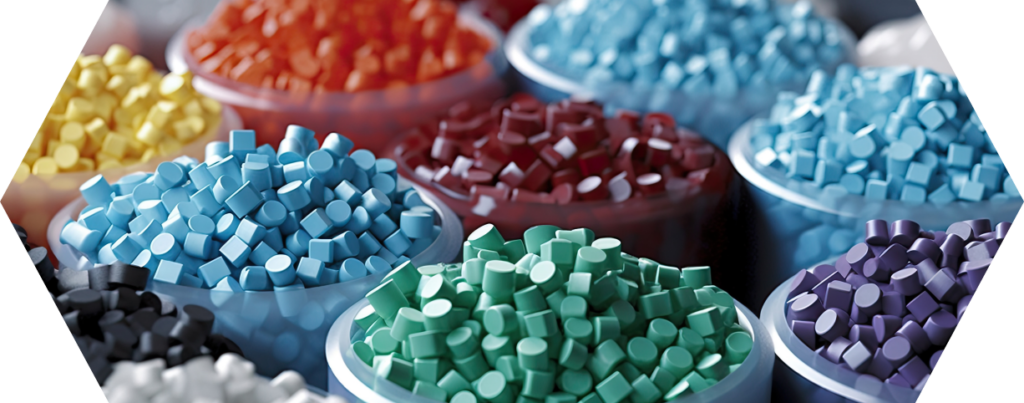
#4 FEP vs. PTFE: A comparison of processing and areas of application
A comparison between FEP (fluoro-ethylene propylene) and PTFE (polytetrafluoroethylene) reveals significant differences in processing and applicability.
These differences are crucial when it comes to selecting the right material for specific applications.
A key feature that distinguishes FEP from PTFE is its weldability. This property considerably expands the processing and application possibilities of FEP.
Weldability and coating options for FEP
FEP can be processed by welding, which enables seamless encapsulation of components.
This ability makes FEP ideal for applications where a complete seal is required, such as in the chemical industry or in semiconductor manufacturing. In contrast, PTFE cannot be welded, which limits its application to wrappings or coatings.
This limitation means that while PTFE provides an excellent surface coating for non-stick and anti-corrosion purposes, it is not suitable for applications that require a seamless coating.
Areas of application
FEP is used in a variety of industries due to its weldability and ability to be encapsulated, including:
- Chemical processing: For hoses, valves and pumps that have to withstand aggressive chemical exposure.
- Semiconductor industry: In the manufacture of wafer carriers and other components that require high purity and chemical resistance.
PTFE is used here in particular:
- Food industry: As a non-stick coating for cookware.
- Aerospace: For seals and plain bearings that are exposed to extreme conditions.
- Electronics: As insulation for cables and plug connections due to its excellent dielectric properties.
PTFE fillers and their advantages
PTFE can be provided with various fillers to improve its physical properties:
- Glass: Increases abrasion resistance and thermal resistance, ideal for applications requiring higher mechanical strength.
- Carbon: Improves wear resistance and heat dissipation, suitable for applications where lower friction and better heat resistance are required.
- Fiber composites: Increase overall strength and resistance to deformation under load, making them ideal for demanding industrial applications.
The choice between FEP and PTFE ultimately depends on the specific requirements of the application, including the need for weldability, the type of chemical exposure and the physical properties required.
By taking these factors into account, engineers can select the material that offers the best performance for their specific needs.
synthetic material | Properties of plastic | Main areas of application |
---|---|---|
FEP | High chemical resistance, heat resistant | Chemical industry, cable sheathing, semiconductor production |
PTFE | Extremely heat-resistant, non-stick, chemically inert | Seals, coatings, plain bearings, in the chemical and food industries |
PE (polyethylene) | Good chemical resistance, impact resistant | Packaging, pipes, containers, in the construction industry |
PU (polyurethane) | Wear-resistant, flexible, good elasticity | Seals, hoses, rollers, shoe soles, furniture upholstery |
POM (polyoxymethylene) | High rigidity, wear resistance, low friction | Precision parts in mechanical engineering, gear wheels, bearings, household appliances, automotive components |
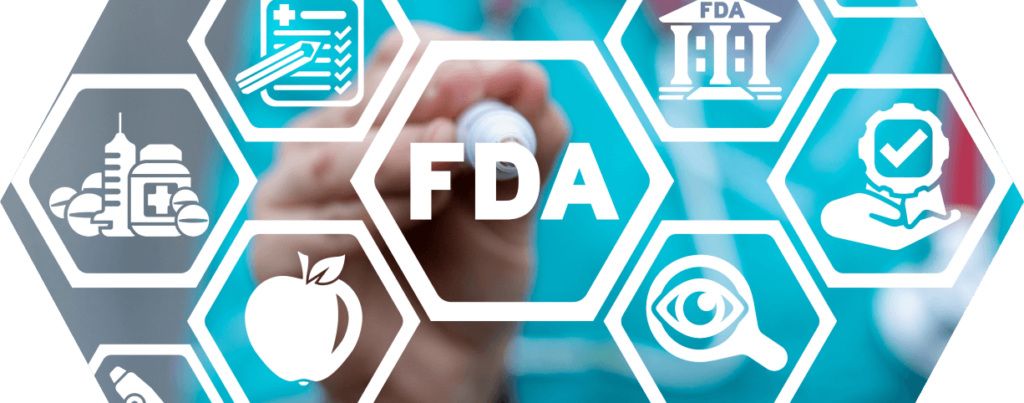
#5 Precise temperature control during FEP processing
Precise control of the processing temperature is critical when handling FEP (fluoro-ethylene propylene) to ensure the integrity and performance of the material.
FEP has a relatively narrow processing temperature range, which must be carefully observed.
Improved processing temperature control for FEP
Optimum processing temperature: FEP melts at a temperature of around 260°C to 280°C. This melting temperature should be precisely controlled to ensure uniform processing and avoid thermal degradation.
Temperatures above 280°C can lead to decomposition of the material, which has a negative effect on the physical properties of FEP and can result in the release of harmful gases.
Lower temperature limit: While the upper temperature limit is mainly important during processing, the lower temperature limit is relevant for the application.
FEPremains flexible and functional down to temperatures of around -200°C, making it suitable for applications in extremely cold conditions.
Thermoregulation systems: Professionals use advanced thermoregulation systems for precise temperature control during FEP processing.
These systems enable precise monitoring and adjustment of the temperature during the extrusion process, welding or other processing methods.
By using such systems, manufacturers can ensure the quality of their FEP products by guaranteeing uniform material properties without overheating or unwanted chemical decomposition.
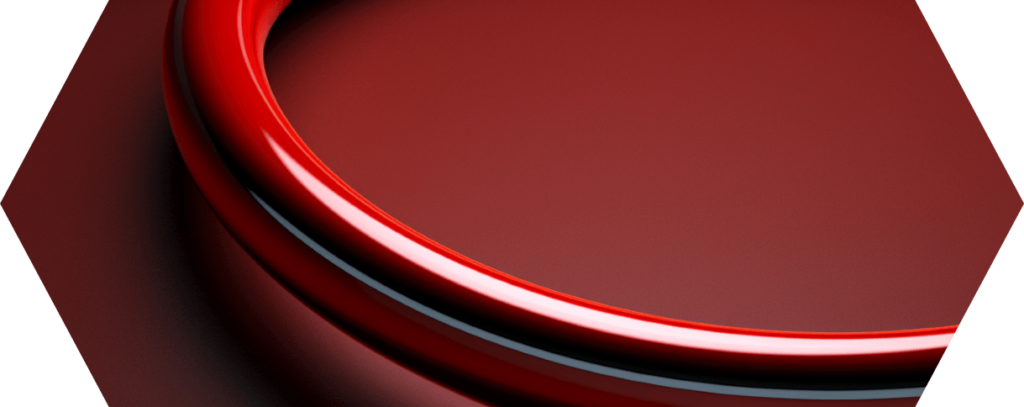
#6 FEP-coated O-rings: A guide to core materials
FEP-coated O-rings offer an innovative solution for applications that want to combine the chemical resistance of fluoropolymers with the elasticity of traditional elastomers.
These O-rings consist of an elastomer core coated with a layer of FEP (fluorine-ethylene-propylene) in order to utilize the advantages of both materials.
In this chapter, we examine the special features of FEP-coated O-rings, the core materials used and the difference between FEP and PFA (perfluoroalkoxy) O-rings.
What are FEP-coated O-rings?
FEP-coated O-rings combine the high chemical resistance and wide temperature range of FEP with the flexibility and sealing properties of an elastomer core.
These O-rings are particularly useful in environments where aggressive chemicals, high temperatures and cleanliness requirements prevail.
Which core materials are used?
- FKM (fluororubber): Known for its excellent heat, oil and chemical resistance. FKM is the preferred choice for most industrial applications.
- Silicone: Offers excellent flexibility and temperature resistance over a wide range. It is ideal for applications where low temperatures prevail.
- EPDM (ethylene propylene diene rubber): Less commonly used, but offers good chemical resistance and is suitable for applications involving steam or water.
When to use which core material?
- FKM is used in most chemical and industrial environments due to its extensive resistance to oils, chemicals and heat.
- Silicone is the choice for applications that require excellent low-temperature flexibility or food compatibility.
- EPDM is particularly suitable for applications in aqueous or steam-based systems where good water and steam resistance is required.
Difference between FEP and PFA O-rings
- Temperature resistance: PFA can withstand higher temperatures than FEP and is therefore better suited to more extreme conditions.
- Processability and flexibility: FEP is generally more flexible and easier to process, making it attractive for O-ring applications where flexibility and sealing are important.
- Cost: FEP is generally less expensive than PFA, making it an economical choice for many applications.
FEP-coated O-rings offer an effective solution to complex sealing problems by combining the advantages of fluoropolymers with the elasticity of rubber.
The choice of core material and sheath type depends on the specific requirements of the application, including chemical exposure, temperature range and required sealing properties.
Core material | Temperature limits | Chemical resistance | Compression set |
---|---|---|---|
FEP/FKM | -20°C to +200°C | Almost universal resistance | Low |
FEP/silicone | -60°C to +200°C | Almost universal resistance | Medium |
FEP/EPDM | -45°C to +200°C | Almost universal resistance | Medium to high |
- Temperature limits indicate the range in which the core material retains its physical properties and functions effectively.
- Chemical resistance: All core materials, in combination with an FEP coating, offer broad chemical resistance to a wide range of aggressive media.
- Compression set: This is a measure of the material’s ability to return to its original shape after a compressive load. “Low” means that the material returns well to its original shape, while “Medium to High” indicates that the material may exhibit permanent deformation under certain conditions.
This table is intended to serve as a guide to help select the appropriate core material for specific applications by highlighting important properties and differences between the various FEP-coated O-ring types.
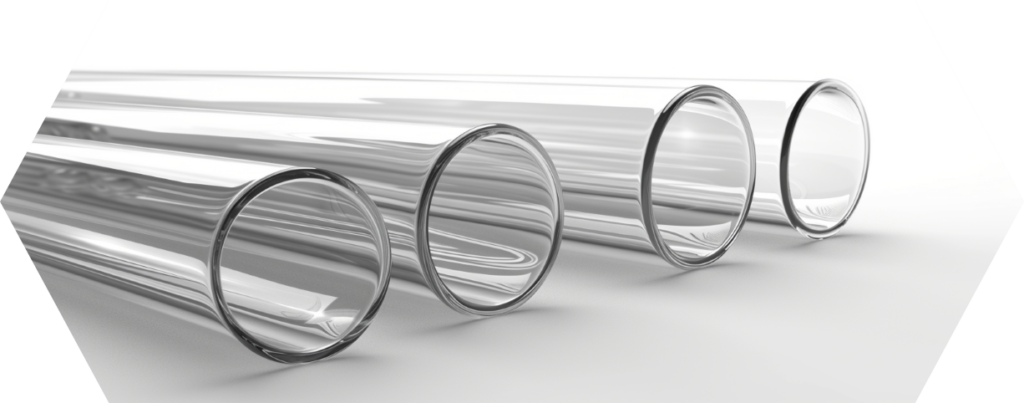
#7 FAQ section: FEP material
Finally, some answers to frequently asked questions.
#7.1 What is fluoro-ethylene propylene (FEP)?
FEP is a fluoropolymer known for its chemical resistance and thermal stability. It is produced by the copolymerization of tetrafluoroethylene and hexafluoropropylene.
FEP is valued for its excellent insulating properties and resistance to extreme temperatures and chemicals in industry and technology.
#7.2 What is FEP typically used for?
FEP is frequently used in the electronics and aerospace industries for cable and wire insulation, in the chemical industry for corrosion-resistant linings and in medical technology for biocompatible applications.
Its unique properties make it ideal for high-temperature and chemical-resistant applications.
#7.3 How is FEP produced?
FEP is produced by emulsion polymerization by copolymerizing tetrafluoroethylene (TFE) and hexafluoropropylene (HFP).
This process requires precise temperature control and purity standards in order to obtain a product with optimum properties.
#7.4 Can FEP surfaces be modified to improve adhesion with other materials?
Yes, FEP surfaces can be modified by plasma treatment or chemical etching to improve adhesion.
#7.5 Is FEP environmentally friendly?
FEP is more environmentally friendly to produce and use than many other plastics.
Current research is aimed at making its production more environmentally friendly and improving its recyclability in order to further minimize its environmental impact.
#7.6 What does the future of FEP look like?
The future of FEP looks promising, with increasing demand in various industries.
Innovations in processing technology and a growing focus on environmental compatibility will expand the areas of application for FEP, particularly in the fields of renewable energies and biomedicine.
“I am convinced that we should share our knowledge with the world. I hope I have been able to answer all your questions. If you have any further questions, please feel free to contact us at any time. We will be happy to help you.”
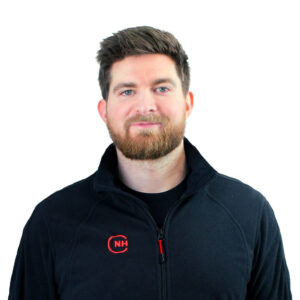
Lord of the O-rings
Author of the Sealing Academy