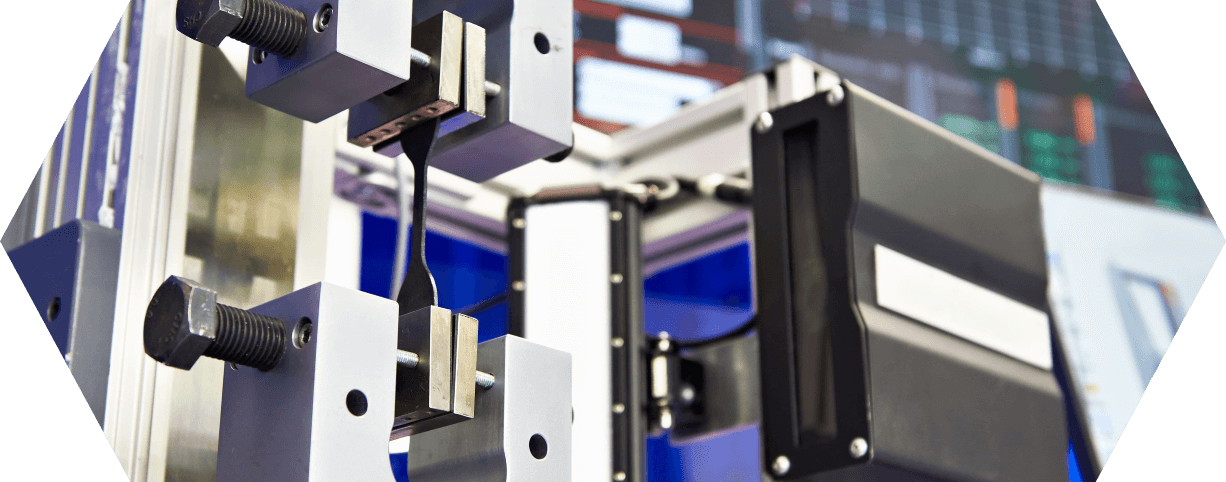
10 Fragen: O-Ring Datenblätter
Die 10 wichtigsten Fragen zur korrekte Auslegung von O-Ring Datenblätter beantworten wir Ihnen in diesem kurzen Beitrag einfach und verständlich.
Ein Mindestmaß an Verpressung zwischen den Bauteiloberflächen ist notwendig, damit O-Ringe ihre Dichtwirkung entfalten. Der notwendige Druck geht zum einen von den abzudichtenden Maschinenelementen und zum anderen von druckbeaufschlagten Medien aus.
Doch gerade hohe Betriebsdrücke beanspruchen O-Ringe stark. Dabei kann es zu mechanischen Schäden und bleibenden Verformungen kommen. Hier lesen Sie, wie mit O-Ring-Härte und Dichtspalt die wichtigsten Faktoren unter Druck zusammenwirken.
Die Dichtwirkung eines O-Rings kommt erst durch die elastische Verformung seines Querschnitts im Einbauraum zustande. Denken wir an eine Flanschdichtung: Der Monteur legt das Dichtungselement mit kreisförmigem Querschnitt in die Nut des Gehäuses ein.
Beim Verschrauben der Deckplatte entsteht ein Druck, der den Querschnitt des O-Rings verformt. In diesem Fall erfolgt die Verformung in axialer Richtung zwischen Nutgrund und Dichtfläche. Der Querschnitt der Elastomerdichtung ist nun nicht mehr rund, sondern oval. So verschließt das Dichtungselement Unebenheiten in den Dichtflächen.
Bei einer radialen Abdichtung, also einer klassischen Kolben- oder Stangendichtung, ergibt sich ein radiales Spaltmaß zwischen innerem und äußerem Maschinenteil.
Dieses Maß wird in der Dichtungstechnik als Dichtspalt bezeichnet. Dieser Spalt ist besonders entscheidend, wenn es um die Abdichtung zwischen zwei Räumen mit verschiedenen Druckniveaus geht. Denn der höhere Druck bewegt den O-Ring gegen die druckabgewandte Seite der Nut.
Das muss sich nicht negativ auf die Funktion der Dichtung auswirken. Innerhalb gewisser Grenzen kann die zusätzliche Flächenpressung die Dichtleistung unterstützen. Besonders hohe Drücke können jedoch zu einer großen Belastung für das Dichtungssystem werden. Sie pressen den O-Ring in den Dichtspalt und verursachen damit mechanische Schäden. Dazu tragen hohe Temperaturen und abrupte Druckstöße bei.
Die Härte des O-Rings sagt aus, wie leicht er sich unter der Einwirkung von Druck verformen lässt. Wenn er zwischen Dichtfläche und Einbaunut verpresst wird, passt er sich den Bauteilkonturen an und dichtet auch feine Kratzer oder andere Fehler in den Oberflächen ab.
Je geringer die Härtes des O-Rings ist, desto weniger Druck wird für die notwendige Verpressung benötigt.
Bei O-Ringen kommen zwei Verfahren für die Härtemessung zum Einsatz: Shorehärte und IRHD. Beide Messmethoden beruhen darauf, dass ein definierter Prüfkörper mit einem bestimmten Gewicht auf die Materialprobe einwirkt. Über die Eindringtiefe ergibt sich die Härte nach Shore oder IRHD. Beide Verfahren nutzen Skalen von 0 bis 100.
Dabei steht eine Härte von 100 jeweils dafür, dass der Prüfkörper überhaupt nicht in die Probe eingedrungen ist. Die Shorehärte des O-Ring-Werkstoffes ist eine zentrale Angabe im technischen Datenblatt. Der Kennwert stellt oft ein entscheidendes Kriterium bei der Werkstoffauswahl dar.
Entscheidend für Praktiker: Auf den Datenblättern der O-Ring-Werkstoffe findet sich in der Regel die an Materialproben ermittelte Shorehärte. Abweichungen zwischen der Shorehärte einer Normprobe und der Härte des Endprodukts O-Ring lassen sich nicht vermeiden. Zu groß sind die geometrischen Unterschiede zwischen Probe und Fertigteil. Die Verfahren sind daneben anfällig für Messfehler.
Entgegen verbreiteter Annahmen ist ein härterer O-Ring nicht automatisch besser als ein weniger hartes Exemplar. Wahr ist, dass härtere O-Ringe sich unter einer Druckeinwirkung weniger leicht verformen. Das hat Vorteile hinsichtlich der Haltbarkeit der Dichtung.
Härtere O-Ringe passen sich dadurch aber auch weniger gut den feinsten Unebenheiten in den Dichtungsflächen an. Das richtige Maß für die Härte eines O-Rings ergibt sich also immer aus der Gesamtheit der Betriebsbedingungen und der Gestaltung aller Bauteile des Dichtungssystems.
Die Shorehärte ist aber nicht allein verantwortlich für den Verformungswiderstand eines O-Rings. Daneben spielt der Druckverformungsrest eine wichtige Rolle. O-Ringe nehmen unter Druckbelastung nicht nur eine elastische, sondern auch eine plastische Verformung an.
Diese sollte möglichst gering ausfallen, damit sich der O-Ring über lange Zeit wechselnden Betriebsbedingungen anpassen kann. Je geringer der Druckverformungsrest, desto weniger bleibende Verformung behält ein O-Ring nach seiner Entlastung zurück.
Zuerst die gängigen Richtwerte für die Gestaltung von Nuttiefe und Schnurdurchmesser: Wie stark die druckbedingte Verformung des O-Rings in der Einbaulage ausfällt, das gibt die Verpressung an. Dabei handelt es sich um den prozentualen Anteil des Schnurdurchmessers, um den der Querschnitt zusammengepresst wird.
Übliche Verpressungen für den statischen Einsatz von O-Ringen bewegen sich zwischen 15 und 30 Prozent. Die Breite der Nut sollte so ausgelegt sein, dass das Medium von der druckbelasteten Seite gleichmäßig eindringen kann.
Ein häufig angesetzter Richtwert: Die rechteckige Querschnittsfläche der Nut sollte etwa das 1,25-fache der runden Querschnittsfläche des O-Rings betragen. Der Mediendruck presst den O-Ring nicht nur gegen die Flanke der Nut, sondern auch an den Dichtspalt zwischen den Bauteilen.
Der Dichtspalt ergibt sich aus dem Durchmesserspiel zwischen den beiden abzudichtenden Bauteilen. Wirkt der Druck eine ausreichend hohe Kraft auf die Dichtung aus, kann der O-Ring in diesen Spalt hineingepresst werden. Ein größerer Dichtspalt begünstigt diesen Vorgang. Das gilt vor allem für radiale Abdichtungen.
O-Ringe mit geringerer Shorehärte lassen sich bereits mit geringerem Druck in den Dichtspalt pressen. Das kann zu einer bleibenden Verformung der Elastomerdichtung und damit zu ihrem Versagen führen. Dabei ergibt sich auch das Schadensbild der Spaltextrusion: Hier schert die Nutkante das Material in dünnen Schichten vom O-Ring ab.
Solche mechanischen Schädigungen des O-Rings stellen noch vor Alterung und Medienangriff die häufigste Ursachenkategorie für das Versagen einer O-Ring-Dichtung dar.
Bei Druckanwendungen ist die direkteste Lösung in der Regel keine Option: Der Systemdruck kann gewöhnlich nicht reduziert werden, um den Anforderungen der Abdichtung Rechnung zu tragen. Stattdessen sind Optimierungen am Dichtungssystem gefragt.
Bei Anwendungen mit hoher Druckbelastung sollte der Konstrukteur O-Ringe mit höhere Shorehärte vorsehen. Mit den verbreiteten Basiselastomeren wie FKM oder NBR lassen sich durch die Wahl unterschiedlicher Compounds Shorehärten im üblichen Bereich von 70 bis 90 Shore A erzeugen.
Wenig geeignet für Druckanwendungen sind Silikone wie VMQ oder FVMQ. Hier sollte der Dichtspalt besonders gering gewählt werden. Polyurethanwerkstoffe halten einem hohen Systemdruck deutlich besser Stand. Sie haben einen sehr geringen Druckverformungsrest.
Nach der Entlastung nehmen sie also ihre ursprüngliche Form zu einem hohen Maß wieder an. O-Ringe mit höherer Schnurstärke haben mehr Reserven und behalten so auch bei Spaltextrusion länger ihre Dichtwirkung. Zusätzlich können Gewebearmierungen oder extrusionsfeste Stützringe die Haltbarkeit der Dichtung steigern.
Erst nachdem die Werkstoffauswahl ausgereizt ist, sollten konstruktive Maßnahmen folgen. Allgemeine Tabellen geben Anhaltspunkte zur Gestaltung des Dichtspalts in Abhängigkeit vom O-Ring. So sehen sie für einen O-Ring mit einer Härte von 70 Shore A und einer Schnurstärke zwischen 2 und 3 Millimetern folgendes vor: Bei einer Druckbelastung bis 70 bar darf der Dichtspalt maximal 0,08 Millimeter betragen.
Ein O-Ring gleicher Schnurstärke mit 90 Shore A kann bei gleicher Druckbelastung dagegen in einen Einbauraum mit einem Spaltmaß von bis zu 0,15 Millimetern eingesetzt werden.
Durch die Fertigung der Bauteile mit möglichst geringen Toleranzen lässt sich der Dichtspalt verkleinern. Die Anforderungen an die Wirtschaftlichkeit begrenzen diesen Ansatz jedoch. Einbaunuten für O-Ringe werden auf rotationssymmetrischen Bauteilen mit einem Drehmeißel eingestochen.
Bei Flanschdeckeln kommt ein entsprechender Nutfräser zum Einsatz. Die Präzision dieser Verfahren zu verbessern oder das Endergebnis durch nachgelagerte Verfahren wie das Schleifen zu steigern, treibt die Fertigungskosten in die Höhe. Genauso wichtig ist aber auch, wie genau die beiden Bauteile im Einbauzustand zueinander positioniert sind. Etwa können Führungen die Exzentrizität der Werkstücke wirksam begrenzen.
Die konstruktive und fertigungstechnische Optimierung der Nutgestaltung hat ihre Grenzen: Enge Toleranzen und hohe Oberflächengüten stellen einen erheblichen Kostenfaktor dar. Um den Aufwand für eine leistungsfähige Abdichtung in einem wirtschaftlichen Rahmen zu halten, müssen auch die übrigen Komponenten des Dichtungssystems auf die Druckanwendung hin optimiert werden.
Unsere Anwendungsexperten unterstützen Sie gerne bei der Suche nach ganzheitlichen Lösungen.
„Ich bin überzeugt davon, dass wir unser Wissen mit der Welt teilen sollten. Ich hoffe, dass ich alle Ihre Fragen beantworten konnte. Sollten Sie noch Fragen haben, dann können Sie sich jederzeit gerne bei uns melden. Wir helfen Ihnen gerne weiter.“
Herr der O-Ringe
Autor der Dichtungsakademie
Die 10 wichtigsten Fragen zur korrekte Auslegung von O-Ring Datenblätter beantworten wir Ihnen in diesem kurzen Beitrag einfach und verständlich.
Die 10 wichtigsten Fragen zur korrekte Auslegung von O-Ring Nuten beantworten wir Ihnen in diesem kurzen Beitrag einfach und verständlich.
Die 10 wichtigsten Fragen zur korrekte Lagerung von O-Ringen beantworten wir Ihnen in diesem kurzen Beitrag einfach und verständlich.
Sie müssen den Inhalt von reCAPTCHA laden, um das Formular abzuschicken. Bitte beachten Sie, dass dabei Daten mit Drittanbietern ausgetauscht werden.
Mehr Informationen