10 questions: O-RING BEständigkeit
#1 How do you test the O-ring resistance?
To test the durability of O-rings, standardized tests are carried out under simulated operating conditions.
This includes compatibility tests with various media (oils, gases, chemicals), temperature change tests, pressure load tests as well as ageing and wear tests.
These tests measure the physical changes in the O-ring, such as volume change, hardness change and cracking, to determine its suitability for specific applications.
Test type | Test description | Aim |
---|---|---|
Compatibility tests | Exposure to specific media at different temperatures. | Determination of chemical resistance. |
Temperature cycling tests | Exposure to extreme temperatures and rapid temperature changes. | Evaluation of thermal resistance. |
Pressure load tests | Application of pressure and checking for leaks or structural changes. | Testing pressure resistance and tightness. |
Ageing and wear tests | Long-term tests under accelerated ageing conditions such as UV light, ozone or high temperature. | Evaluation of long-term durability and wear resistance. |
REQUEST O-RINGS QUICKLY AND EASILY?
Almost any dimension available
Offer received in record time
No minimum order quantities or minimum item values
One contact for all concerns
#2 How does temperature affect O-ring life?
The service life of an O-ring is significantly influenced by the temperature. High temperatures can age the material faster, make it softer or even degrade it, while very low temperatures can make it brittle and crack.
The optimum operating temperature depends on the material of the O-ring; exceeding the limit values leads to accelerated degradation and shortened service life. It is important to select the correct material for the specific application temperature.
Temperature range | Effects |
High | Accelerated ageing, softening, chemical degradation. |
Low | Hardening, brittleness, cracking. |
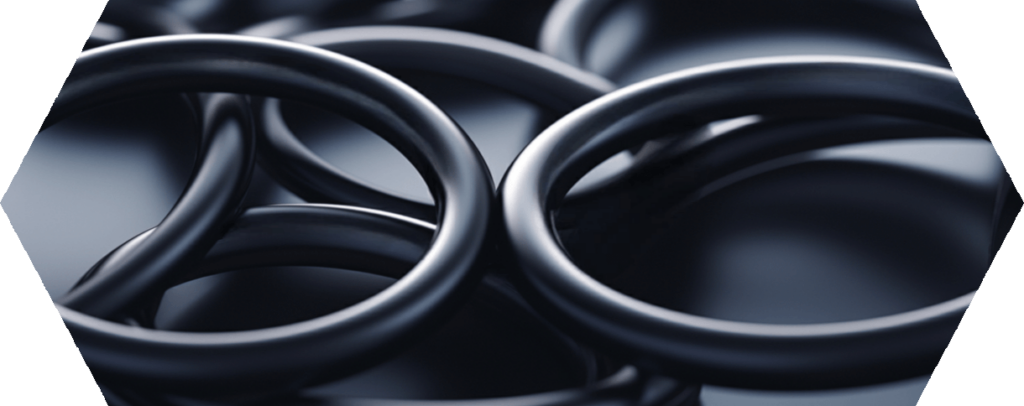
#3 How do you recognize O-ring wear?
O-ring wear can be recognized by physical changes such as cracking, hardening, softening, deformation or surface erosion.
Other indicators are loss of performance, such as leaks or pressure loss in a sealed system.
Regular inspections and monitoring of operating conditions are essential in order to identify signs of wear at an early stage and prevent breakdowns.
Signs of wear and tear | Causes | Consequences | Test methods |
---|---|---|---|
Cracking | Aging, ozone, UV light | Leaks, loss of function | Visual inspection, microscope |
Hardening | Exposure to cold, ageing | Brittleness, embrittlement | Hardness test |
Softening | Chemical effects, heat | Loss of material, leaks | Hardness testing, weight measurement |
Deformation | Excessive load, heat | Loss of fit, seal failure | Dimensional check, visual inspection |
Surface erosion | Abrasive media, turbulence | Leakages, loss of efficiency | Visual inspection |
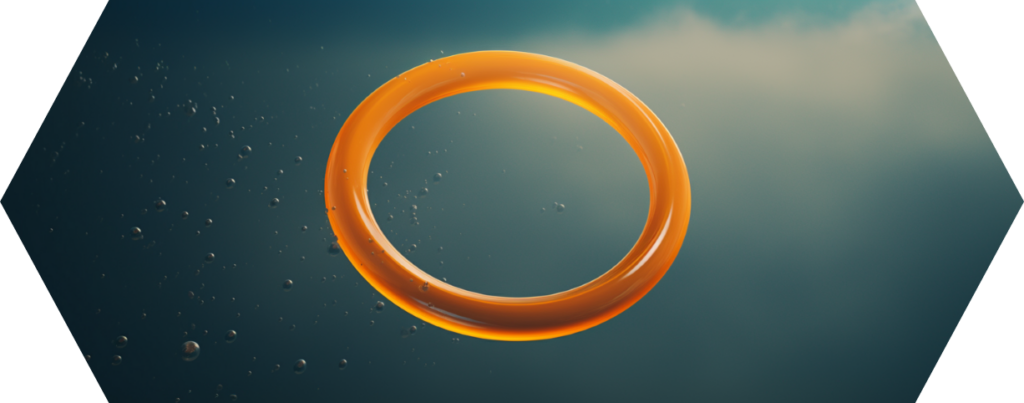
#4 How do chemicals affect O-rings?
Chemicals can affect O-rings in different ways, depending on the material of the O-ring and the type of chemical.
Some chemicals cause swelling, softening or dissolution of the material, while others can lead to hardening or cracking.
Chemical compatibility must be carefully checked before selecting an O-ring material for a specific application to avoid material failure and system downtime.
Material | Chemical resistance | Susceptible to | Area of application |
---|---|---|---|
Nitrile rubber (NBR) | Oils, greases | Ketones, ozone, strong acids | General industry, automotive |
Fluororubber (FKM) | High-temperature oils, chemicals | Ketones, low-molecular esters | Chemical industry, aviation |
Ethylene propylene diene monomer (EPDM) | Water, steam, alcohols | Mineral oils, hydrocarbons | Sanitary, automotive, HVAC |
Silicone | Heat, ozone, UV light | Aliphatic hydrocarbons, acids | Medicine, food, aviation |
Perfluoroelastomer (FFKM) | Almost all chemicals | Fluorinated solvents | Chemical processing, semiconductors |
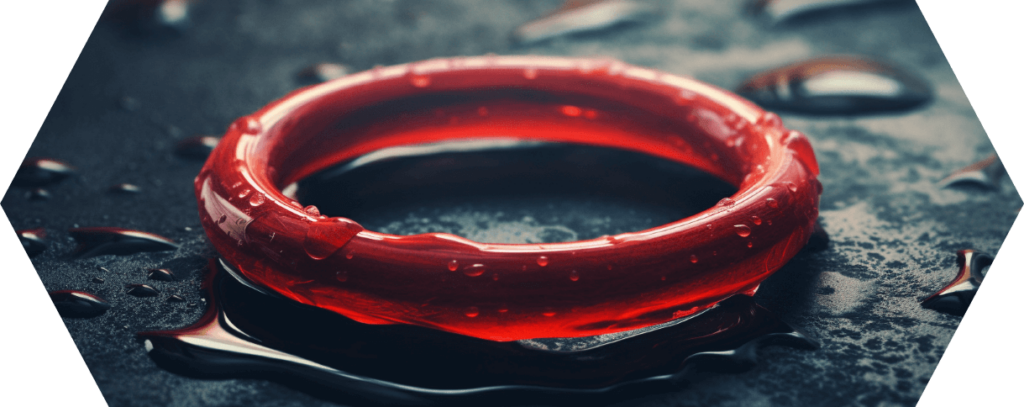
#5 How to choose durable O-ring materials?
The selection of resistant O-ring materials requires careful evaluation of operating conditions such as temperature, pressure and chemical exposure.
Materials such as nitrile rubber (NBR) are suitable for oil-based applications, while fluororubber (FKM) offers high resistance to heat and chemicals.
Perfluoroelastomers (FFKM) are ideal for extreme temperatures and exposure to chemicals. Compatibility with media, operating temperature and mechanical requirements are decisive for the choice of material.
Material | Resistance | Application | Temperature | Special |
---|---|---|---|---|
NBR | Oil, water | Automotive, hydraulics | -30°C to +120°C | Good abrasion resistance |
FKM | Chemicals, heat | Chemicals, aviation | -25°C to +200°C | Excellent chemical resistance |
EPDM | Steam, UV light | HVAC, sanitary | -45°C to +150°C | Good weather resistance |
Silicone | Extreme temperatures, UV light | Medicine, food | -60°C to +200°C | Flexible at low temperatures |
FFKM | Almost all chemicals | Semiconductors, chemicals | -40°C to +340°C | Highest chemical and temperature resistance |
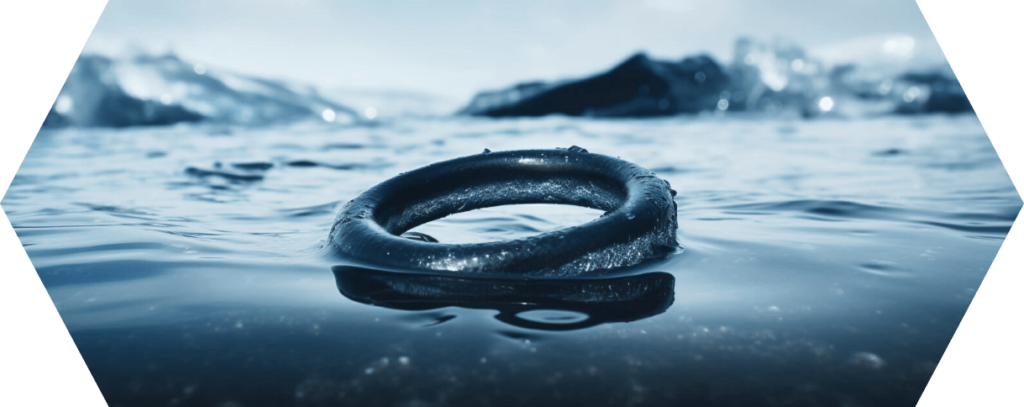
#6 How to store O-rings correctly?
The correct storage of O-rings is crucial to maintaining their service life and performance.
O-rings should be stored in a cool, dry room away from direct sunlight, ozone sources and extreme temperatures. The packaging should not be opened before use to avoid contamination.
It is important not to stretch, compress or store O-rings under weight, as this can lead to deformation. Observing the storage conditions and periods helps to maintain the integrity of the material.
Storage condition | Storage guideline | Purpose |
---|---|---|
Temperature | Cool, stable range (ideally 15-25°C) | Avoidance of material degradation |
Light avoidance | Dark storage, away from direct UV light | Protection against ageing due to UV radiation |
Ozone protection | Store away from ozone sources | Avoidance of cracking due to ozone |
Humidity control | Dry environment, control relative humidity | Prevention of moisture damage |
Packaging | Keep original packaging closed until use | Protection against contamination and deformation |
Deformation protection | No stretching or compression | Preservation of original shape and function |
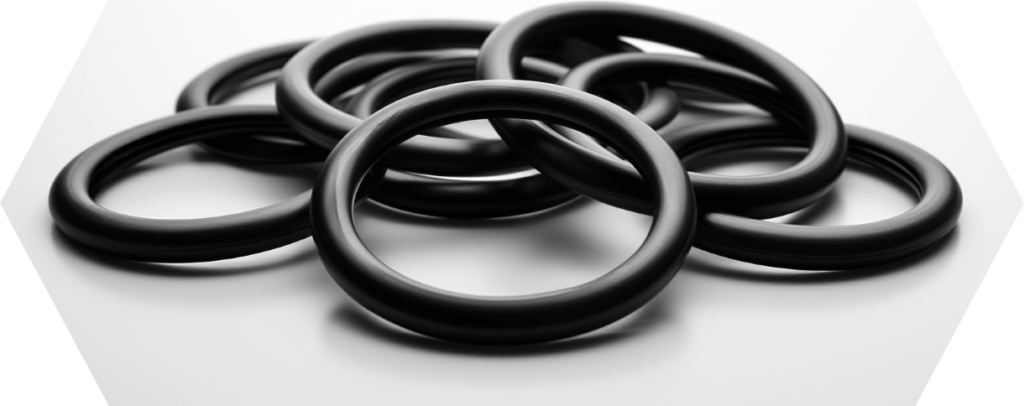
#7 How does pressure affect O-ring resistance?
Pressure has a significant influence on O-ring resistance by increasing the physical load on the material.
Under high pressure, extrusion and deformation of the O-ring can occur, which impairs the sealing ability. The selection of an O-ring with sufficient hardness and the use of back-up rings can help to improve resistance to high pressures.
Material selection and design must take into account the specific printing conditions of the application to ensure optimum performance and longevity.
Factor | Influence on O-ring | Measure for improvement |
---|---|---|
High pressure | Can lead to extrusion and deformation | Use of support rings |
Material hardness | Influences the resistance | Selection of a material with suitable hardness |
Design | Determines the susceptibility to compressive load | Optimization of the groove design |
Operating temperature | Influences material behavior under pressure | Selection of temperature-resistant materials |
Pressure fluctuations | Lead to cyclic loading | Design adaptations for dynamic applications |
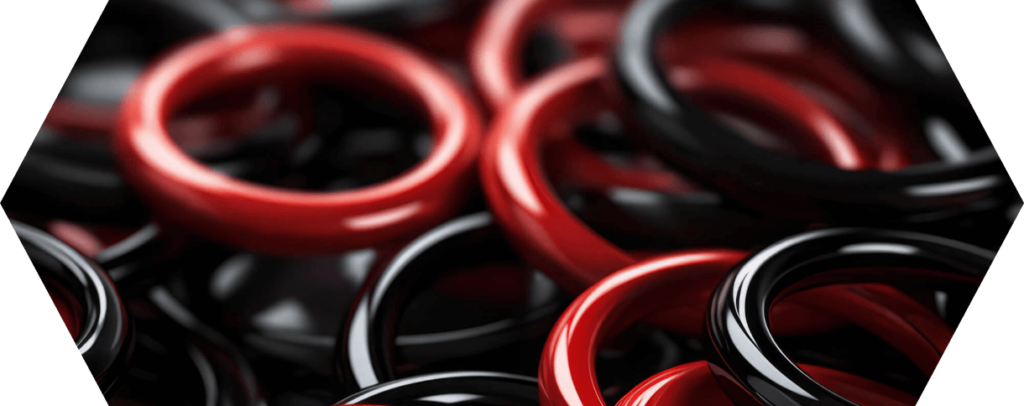
#8 How do you test O-rings for oil resistance?
O-rings are tested for oil resistance using long-term exposure tests in which the O-rings are exposed to different types of oil at different temperatures.
After exposure, the O-rings are examined for changes such as volume increase, change in hardness and cracking.
The selection of the O-ring material is based on the test results to ensure compatibility with specific oil types. Materials such as nitrile rubber (NBR) and fluorocarbon rubber (FKM) are known for their good oil resistance.
Test method | Test parameter | Change |
Long-term exposure | Oil type, temperature | Increase in volume, change in hardness, cracking |
Volume measurement | After exposure | Volume increase |
Hardness test | Before and after exposure | Hardness change |
Crack testing | After exposure | Crack formation |
Material selection | Based on results | Compatibility with oil types |
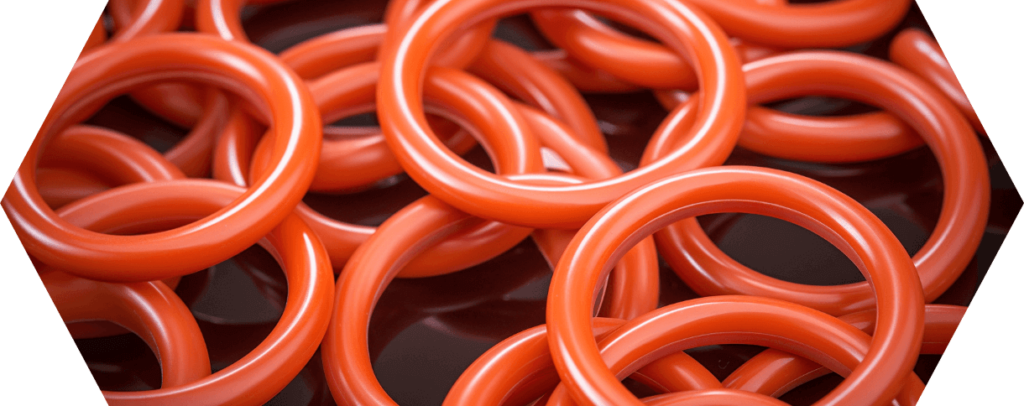
#9 How to prevent O-ring ageing?
The ageing of O-rings can be minimized by selecting the right material, appropriate storage and regular maintenance.
Materials such as EPDM and silicone offer excellent resistance to ageing. O-rings should be stored in a cool, dry place away from direct sunlight and sources of ozone.
The regular inspection and replacement of O-rings in critical applications also helps to minimize the risks of ageing.
Preventive measure | Description of the measure | Purpose |
---|---|---|
Material selection | Use of ageing-resistant materials | Extension of service life |
Appropriate storage | Cool, dry, UV and ozone protected | Avoid premature degradation |
Regular maintenance | Inspection and replacement if there are signs of ageing | Prevention of failures |
Avoidance of harmful influences | Keeping away chemicals that can attack the material | Protection against chemical degradation |
Design optimization | Adaptation of the design to minimize stresses | Reduction of mechanical ageing |
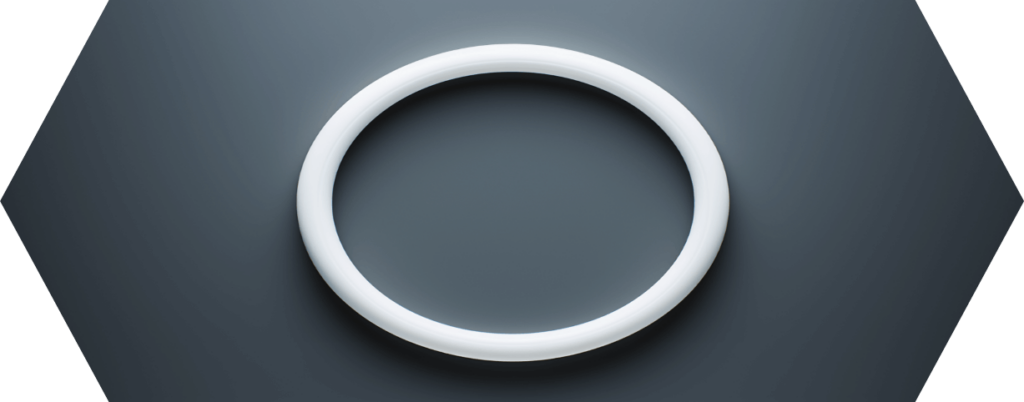
#10 How does UV light affect O-ring materials?
UV light can significantly damage O-ring materials by causing cracking, color change and loss of elasticity.
Materials such as EPDM and silicone show better UV resistance compared to other materials such as NBR.
The protection of O-rings from direct UV exposure by suitable covers or the use of UV-stabilized materials is essential for applications that cannot avoid UV exposure.
material | UV resistance |
---|---|
NBR (nitrile rubber) | Low |
FKM (fluororubber) | Medium |
FFKM (perfluoroelastomer) | High |
Silicone | High |
EPDM (ethylene propylene diene monomer) | Very high |
“I am convinced that we should share our knowledge with the world. I hope I have been able to answer all your questions. If you have any further questions, please feel free to contact us at any time. We will be happy to help you.”
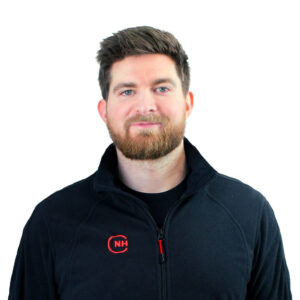
Lord of the O-rings
Author of the Sealing Academy