Shore hardness
Shore hardness: Everything you need to know
Shore hardness is a central concept in the world of materials science and plays a decisive role in the quality assessment of rubber, plastic and other elastomeric materials.
Hardness provides information about the resistance of a material to penetration and deformation, which is of great importance for many industries.
We will examine its definition, the basics of its measurement, its applications in different industries and the factors that influence it. In addition, we will also show how to measure Shore hardness and how to choose the right equipment for such measurements.
Whether you are a materials testing professional, work in manufacturing or simply have an interest in materials science, this guide will provide you with in-depth insights and practical information about Shore A and D hardness.
Shore hardness | Description | Typical applications | Measuring range |
---|---|---|---|
Shore A | Measures soft to medium-hard materials | Rubber, elastomers, soft plastics | 0 (very soft) to 100 (medium hard) |
Shore D | Measures harder materials | Hard plastics, denser elastomers | 0 (medium hard) to 100 (very hard) |
Shore B | Middle ground between A and D | Medium-hard materials | 0 (soft) to 100 (harder than A) |
Shore O | For soft elastomers | Very soft elastomers and rubbers | 0 (very soft) to 100 (similar to A) |
Shore M | For extremely soft materials | Foams, very soft rubbers | 0 (very soft) to 100 (softer than O) |
REQUEST O-RINGS QUICKLY AND EASILY?
Almost any dimension available
Offer received in record time
No minimum order quantities or minimum item values
One contact for all concerns
#1 What is Shore hardness?
Shore hardness is a measure of the hardness of elastomeric, plastomeric and other polymeric materials.
Hardness is measured using an instrument called a Shore hardness tester and indicates how resistant a material is to penetration by a specific pressure body.
Historical background
The Shore hardness scale was developed in the early 1900s by Albert F. Shore. Shore, an engineer and inventor, was looking for a standardized method to measure the hardness of materials.
This led to the development of the Shore scales, including the most commonly used Shore hardness A and Shore hardness D scales.
Definition and meaning
The A hardness scale is typically used to measure the hardness of soft to medium-hard materials such as rubber, elastomeric plastics and other soft polymers.
A higher number means a higher hardness of the material. For example, car tire rubber typically has a hardness rating of around 70 A, while soft rubber hose has lower values.
Hardness is of critical importance to many industries as it is directly related to product performance and durability. Materials with inadequate hardness can lead to product failure, safety risks and increased costs.
Areas of application
- Automotive industry (e.g. tires, seals)
- Construction industry (e.g. elastomer seals, hoses)
- Medical technology (e.g. catheters, seals)
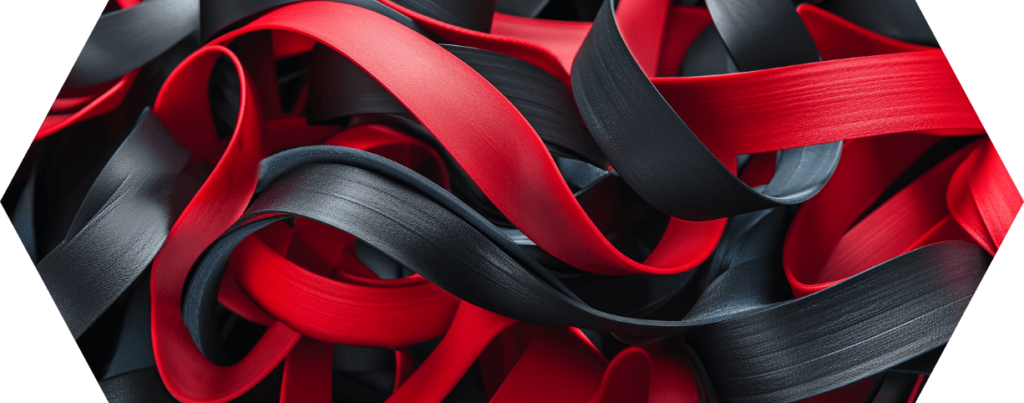
#2 Basics of Shore hardness measurement
Measuring Shore hardness is a straightforward but precise process that provides important information about the properties of a material.
Functionality of a hardness tester for elastomers
A hardness tester measures the hardness of a material by pressing a standardized pressure pin into the material with a certain force.
The depth to which the pin penetrates provides information about the hardness of the material: the less the pin penetrates, the harder the material is.
Steps of the hardness measurement
- Preparation of the material: The material to be tested should have a flat, smooth surface and be stored at a standardized temperature.
- Carrying out the test: The hardness tester is placed vertically on the material and the pressure pin is released.
- Reading the measured values: The scale on the device shows the hardness, which generally ranges from Shore hardness 0 (very soft) to 100 (very hard).
Different types of Shore A hardness testers
- Digital hardness testers: Offer precise and easy-to-read digital displays.
- Manual hardness testers: Traditional devices that are operated manually and offer an analog display.
- Portable hardness testers: Ideal for on-site testing or in situations where the material cannot be taken to a laboratory.
Importance of accurate measurements
Precise hardness measurements are crucial for quality assurance and product development. Inaccurate measurements can lead to incorrect conclusions about the suitability of a material for a particular application.
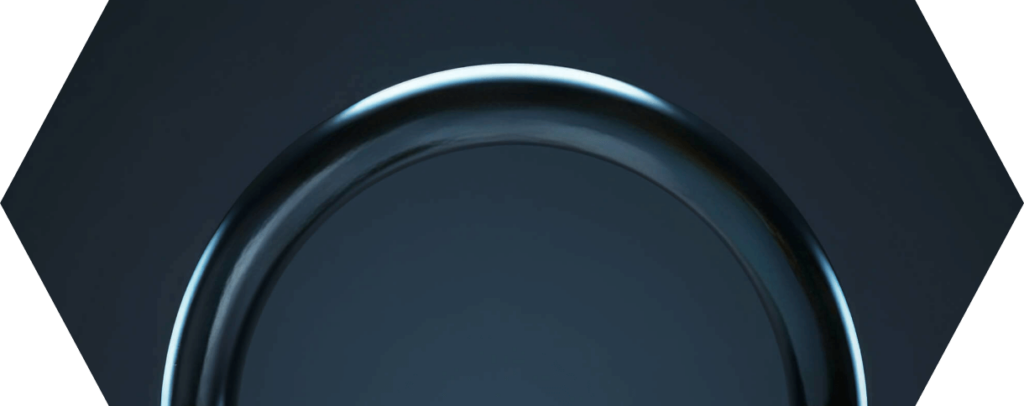
#3 Shore A vs. Shore D
The Shore hardness scales, in particular Shore A and hardness D, are decisive for evaluating the hardness of various materials.
Although both are used to measure material hardness, there are significant differences between them.
Differences between Shore A and Shore D
- Area of application: Shore A is mainly used for soft to medium-hard elastomers, while Shore D is intended for harder plastics and elastomers.
- Measuring method: The scales use different pressure pins and forces, resulting in different hardness ranges.
- Scale range: Shore A ranges from 0 (very soft) to 100 (medium hard), while Shore D ranges from 0 to 100, with 100 standing for very hard materials.
Importance of choosing the right scale
- The choice between Shore A and Shore D depends on the type of material and the expected hardness.
- An incorrect choice of scale can lead to inaccurate or misleading results.
Examples of areas of application
- Shore A: Rubber-like materials such as tires, shoe soles or seals.
- Shore D: Harder plastics such as helmet shells, high-tech plastic components.
Understanding the scales for better material selection
- Understanding the differences between the scales helps engineers and designers to select the right materials for their specific requirements.
- It facilitates communication about material specifications and ensures that the material selection meets the requirements.
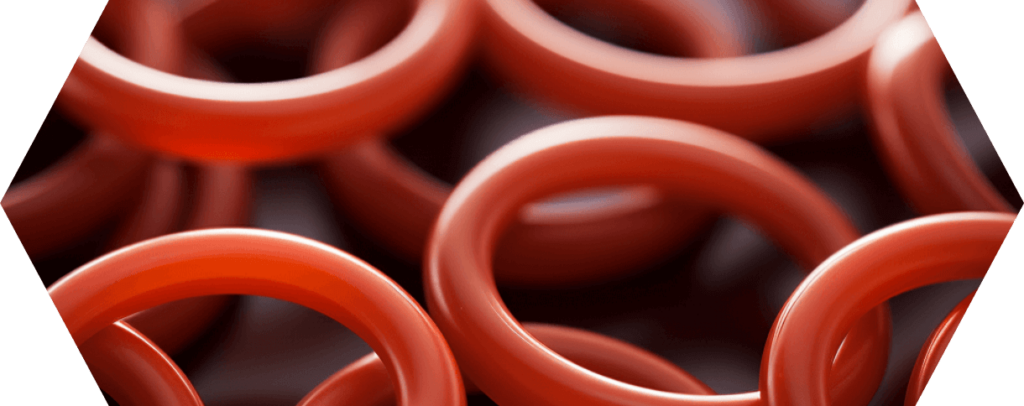
#4 Importance of Shore A in the industry
Hardness is more than just a technical specification; it has far-reaching effects in various industries.
Why is Shore hardness A important?
- Quality control: Hardness values help to assess the quality and consistency of materials, which is crucial for product reliability.
- Product design: The hardness of a material influences design decisions, especially in areas such as ergonomics and durability.
- Safety and compliance: Some industries have specific requirements for the hardness of materials that must be met for safety reasons.
Examples of materials that are tested according to Shore hardness A
- Automotive tires: A classic example in which the hardness of the elastomer influences performance and safety.
- Medical devices: Certain medical products, such as catheters, require specific degrees of hardness for functionality and patient comfort.
- Building and sealing materials: The hardness of these materials influences their ability to seal in the long term.
Hardness measurements in product development
- Material selection: Engineers select materials based on hardness to meet flexibility and strength requirements.
- Prototyping and testing: Hardness measurements are often carried out during the prototyping phase to ensure that the material meets the requirements.
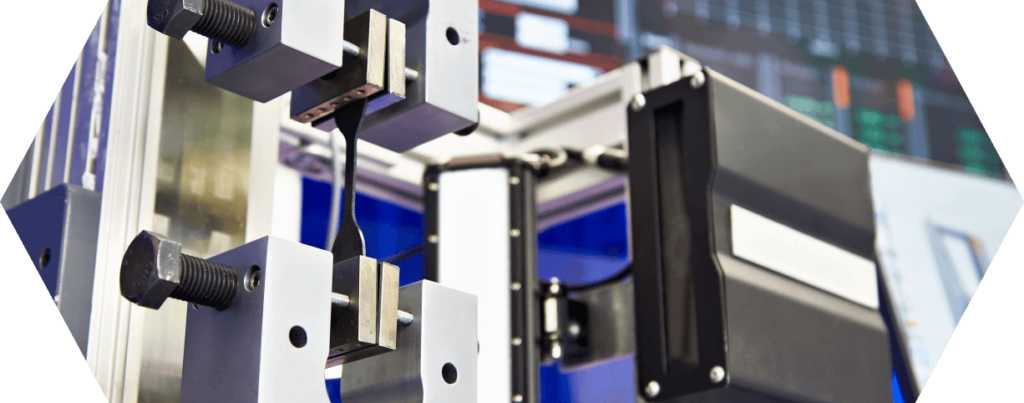
#5 Carrying out Shore hardness A tests
The correct execution of hardness tests is crucial in order to achieve accurate and reliable results.
Step-by-step instructions for carrying out a Shore A test
- Preparation of the material: Make sure that the material to be tested is clean, flat and at room temperature.
- Calibrating the device: Calibrate the hardness tester according to the manufacturer’s instructions.
- Carrying out the test: Press the hardness tester vertically onto the material and hold it for the recommended time (usually a few seconds).
- Measurement and reading: Read the value on the scale of the device as soon as the pressure pen has fully penetrated.
Tips for accurate measurement results
- Consistent test conditions: Perform tests under similar environmental conditions to minimize variability.
- Multiple measurements: Perform multiple tests and calculate the average to achieve higher accuracy.
- Device maintenance: Regular maintenance and calibration of the hardness tester are crucial for reliable results.
Different hardness tester for Shore A (round) and Shore D (pointed)
- Shore A hardness tester: Uses a rounded tip to measure the hardness of softer materials. The round tip allows for even pressure distribution on softer surfaces.
- Shore D hardness tester: Has a more pointed tip for measuring harder materials. The pointed shape is necessary to leave a sufficient impression on the harder materials.
Why different test probes?
- The choice of test tip depends on the hardness and nature of the material. Softer materials would be deformed too much under a pointed tip, which would lead to inaccurate measurements. Conversely, a round tip would be ineffective on hard materials as it could not leave a significant impression.
Standard for Shore A and Shore D measurement
- DIN ISO 868: This standard specifies the method for determining Shore hardness. It defines the procedures for carrying out Shore A and Shore D hardness measurements and ensures that the results are internationally comparable.
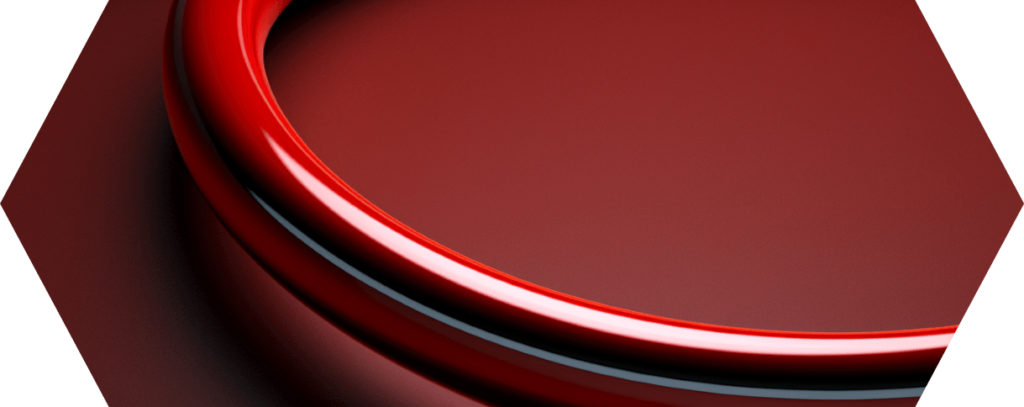
#6 Device specifications and measuring conditions according to DIN ISO 868
The DIN ISO 868 standard provides precise guidelines for the design and characteristics of devices for Shore hardness measurement as well as the conditions under which the measurements should be carried out.
Device specifications
- Indenter: For Shore A measurements, a rounded indenter with a defined radius is used. For Shore D measurements, the indenter is more pointed.
- Penetration depth: The standard specifies the exact penetration depth required for correct measurement.
- Force: The force acting on the indenter is also specified to ensure that the results are consistent.
- Scale and accuracy: The scale of the device must be clearly legible and have a certain accuracy in order to guarantee reliable measured values.
Measuring conditions
- Ambient temperature: The measurements must be carried out in an environment with a controlled and constant temperature. Typically, a room temperature of around 23°C is recommended.
- Humidity: The humidity in the room should be stable so as not to affect the properties of the material to be tested.
- Material condition: The material must be in a uniform and stable condition, free from deformation or damage.
- Waiting time after production: There is a recommended waiting time after production of the material before measurements are taken to ensure that the material has reached its final properties.
Difference in the measurement
- Test specimen vs. finished part: A major difference is that the measurements on a standardized test specimen are performed under ideal conditions, while measurements on the finished part reflect the real application conditions and can be influenced by the shape, size or design of the part.
Example for the evaluation of Shore A hardness
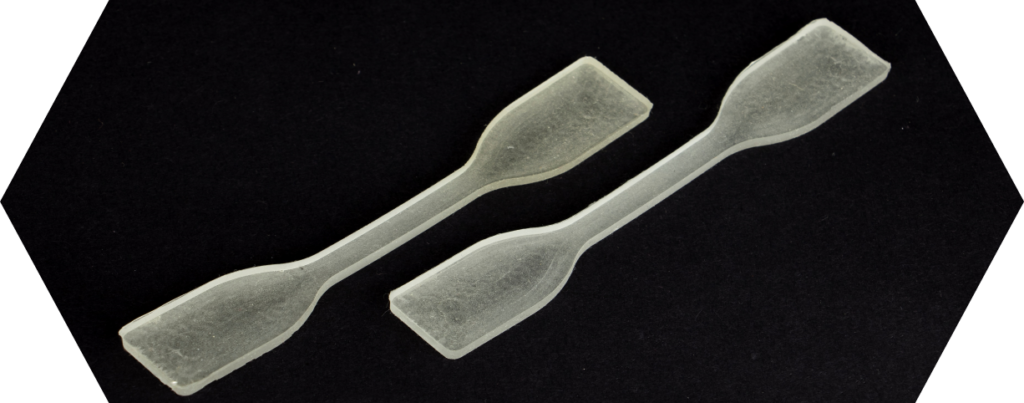
#7 International standards for Shore A hardness testing
Each standard has its own specifications and guidelines, which may differ depending on the region and the specific applications. Here are four prominent standards for Shore A hardness testing:
ASTM D2240 – American standard
- Origin: Developed by the American Society for Testing and Materials (ASTM).
- Description: ASTM D2240 is used in the United States and internationally. It provides a method for determining the indentation hardness of materials classified as rubber, elastomers, and soft plastics. This standard specifies the dimensions and type of durometer (hardness tester) and the method of applying the force.
DIN ISO 868 – German and international standard
- Origin: German Institute for Standardization (DIN) in Germany and adopted as an international standard (ISO).
- Description: DIN ISO 868 is similar to ASTM D2240, but may have specific differences in terms of test conditions and device specifications. It is widely recognized and used in Europe and other countries that follow ISO standards.
JIS K 6253 – Japanese standard
- Origin: Established by the Japanese Industrial Standards Committee (JIS).
- Description: The JIS K 6253 standard is the Japanese equivalent of the Shore hardness test. While it has many similarities to ASTM D2240 and ISO 868, there may be unique requirements or specifications tailored to Japanese industrial practices.
ISO 7619 – International standard
- Origin: Published by the International Organization for Standardization (ISO).
- Description: ISO 7619 is another international standard that provides guidelines for measuring the hardness of vulcanized or thermoplastic rubber. While similar to DIN ISO 868, ISO 7619 may have different clauses or specifications that focus on a broader international audience.
Differences between these standards
- Geographical application: Each standard is mainly used in its region of origin, but may also be recognized internationally.
- Specific guidelines: There may be differences in the details of the test method, the type of durometer used and the conditions under which the tests are carried out.
- Industry application: Certain industries may favor one standard over another based on historical usage, regional presence or specific industry requirements.
#8 FAQ section: Shore hardness A
Finally, some answers to frequently asked questions.
#8.1 What exactly does Shore hardness A measure?
Shore A hardness measures the hardness or resistance of elastomeric and soft plastic materials to penetration.
It is mainly used for materials such as rubber, elastomers and soft plastics.
Material | Shore hardness A | Shore hardness D |
Rigid foams | 20-70 | – |
Silicone rubber | 20-80 | – |
Natural rubber | 40-60 | – |
Ethylene propylene diene rubber (EPDM) | 30-90 | – |
Neoprene | 40-90 | – |
Nitrile rubber (NBR) | 30-95 | – |
Polyurethane rubber | 40-95 | – |
Soft PVC | 70-95 | – |
PE (polyethylene) | – | 40-65 |
PTFE (polytetrafluoroethylene) | – | 50-65 |
Acrylonitrile butadiene styrene (ABS) | – | 60-100 |
Polycarbonate (PC) | – | 75-90 |
POM (polyoxymethylene) | – | 70-90 |
#8.2 In which industries is the Shore A hardness test typically used?
Hardness testing is used in many industries, including the automotive industry, construction, medical technology and the manufacture of consumer goods.
Hardness testing is relevant wherever rubber or elastomeric plastics are used.
#8.3 Why is Shore hardness A important in the industry?
Hardness is crucial for quality assurance and product development.
It provides information on how a material reacts to pressure, which is important for the performance and durability of products such as tires and seals.
#8.4 What are the main differences between the international standards for Shore hardness A?
The main differences between international standards such as ASTM D2240, DIN ISO 868, JIS K 6253 and ISO 7619 lie in the specific test procedures, device specifications and the environmental conditions for carrying out the tests.
These differences reflect regional practices and specific industry requirements.
Standard | Origin | Area of application | Special features |
---|---|---|---|
ASTM D2240 | USA (ASTM) | International use, especially in the USA. Measurement of the hardness of rubber, elastomers and soft plastics. | Provides detailed instructions for carrying out the tests and the device specifications. Widely used in the industry. |
DIN ISO 868 | Germany (DIN) and International (ISO) | Used in Europe and other countries that follow ISO standards. Similar to ASTM D2240 in application. | May include specific requirements for European standards. Often used in research and industry in Europe. |
JIS K 6253 | Japan (JIS) | Japanese industrial standard. Similarities with ASTM D2240 and ISO 868, but with specific requirements for Japan. | Takes into account Japanese industrial practices. Frequently used by Japanese companies and in Asia. |
ISO 7619 | International (ISO) | International guidelines for measuring the hardness of vulcanized or thermoplastic rubber. | Provides a broader international framework that goes beyond the European standards. Used in various countries. |
“I am convinced that we should share our knowledge with the world. I hope I have been able to answer all your questions. If you have any further questions, please feel free to contact us at any time. We will be happy to help you.”
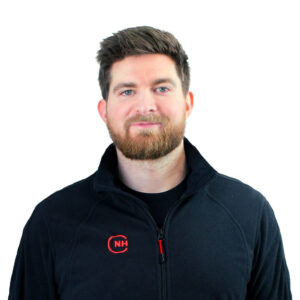
Lord of the O-rings
Author of the Sealing Academy