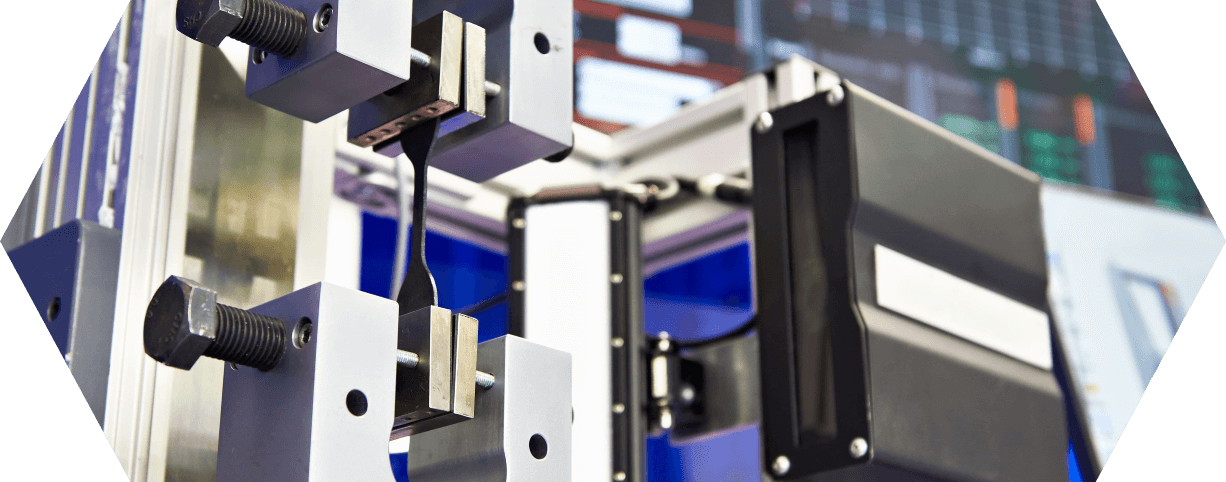
10 Fragen: O-Ring Datenblätter
Die 10 wichtigsten Fragen zur korrekte Auslegung von O-Ring Datenblätter beantworten wir Ihnen in diesem kurzen Beitrag einfach und verständlich.
Die Anforderungen der Kunden an Dichtungen hinsichtlich Medienkontakt, Druck- und Temperaturbelastung sowie Standzeit sind vielfältig. Entsprechend breit gestaltet sich das Portfolio an Dichtungselementen.
Wie sich für jeden Dichtungsfall das optimale Produkt finden lässt, so gilt es auch für dessen Herstellung das passende Fertigungsverfahren auszuwählen. Die Produktionsweise beeinflusst nicht nur die technischen Eigenschaften der Dichtung, sondern auch ihre Kosten. Für industrielle Anwender ist die erfolgreiche Auflösung des dabei entstehenden Zielkonflikts entscheidend.
Stückzahlen und für den Kunden akzeptable Lieferfristen geben aus ökonomischer Sicht den Ausschlag bei der Verfahrensauswahl. Auf der technischen Seite stehen mit Werkstückabmessungen, dem zulässigen Toleranzbereich sowie den physikalischen Eigenschaften weitere wichtige Faktoren. Dabei können die Experten anhand der Art der Dichtung und des Werkstoffes bereits eine Vorauswahl treffen.
Im weiteren Verlauf dieses Beitrags wird der Fokus auf der Herstellung von zwei Dichtungsklassikern liegen: O-Ringe und Flachdichtungen.
Der O-Ring als Dichtung mit der weitesten Verbreitung ist ein geschlossener Ring mit kreisrundem Querschnitt, dessen Abmessungen von Innendurchmesser und Schnurdurchmesser festgelegt werden. O-Ringe kommen für ruhende (statische) und bewegte (dynamische) Dichtungen zum Einsatz.
Die Dichtwirkung stellt sich ein, wenn Druck den Querschnitt des O-Rings elastisch verformt. Es entsteht eine Flächenpressung zwischen Dichtung und Nutgrund einerseits sowie Dichtung und Dichtfläche andererseits. Damit das System funktioniert, müssen Nutauslegung und Werkstoffauswahl stimmen.
O-Ringe bestehen vorwiegend aus Elastomeren, die gummielastische Eigenschaften aufweisen. Diese Eigenschaft erhält das Rohprodukt Kautschuk während der Vulkanisation.
Dieser Prozess führt zur Vernetzung der Makromoleküle und die dabei entstehenden Querverbindungen lassen das Material nach einer von außen bewirkten Formveränderung wieder in die Ausgangsposition zurückkehren.
Weil die Medienbeständigkeit der Elastomere selbst für viele anspruchsvolle Anwendungen nicht ausreicht, kann die Eigenschaft durch eine Ummantelung der O-Ringe mit geeigneten Werkstoffen gesteigert werden. Diesen fehlt häufig wiederum die elastische Eigenschaft eines Elastomers.
Beispiele für bei Dichtungsanwendungen häufig genutzte Elastomere sind NBR (Acrylnitril-Butadien-Kautschuk), FKM (Perfluorkautschuk) und FFKM (Fluorkautschuk). Ebenso bekannt sind die Materialien aber unter den geschützten Handelsnamen der jeweiligen Hersteller.
Flachdichtungen kommen vor allem zur Abdichtung von Flanschen zum Einsatz. Dabei handelt sich um im Rohrleitungsbau verbreitete Verbindungen mit zwei planen Dichtflächen. Hier ist die Auflagefläche des Dichtmittels deutlich größer als beim O-Ring.
Entsprechend fehlt der Flachdichtung dessen kreisförmiger Profilquerschnitt. Durch den etwa durch eine Verschraubung erzielten Anpressdruck gleicht die Flachdichtung Unebenheiten in den Flächen aus und dichtet sie ab.
Flachdichtungen dienen entsprechend nahezu ausschließlich für statische Dichtungsfälle. Zusammen mit der häufig aggressiven Umgebung in der Chemie-, Pharma- und Lebensmittelindustrie macht das neben Elastomeren noch andere Dichtungswerkstoffe interessant.
So bestehen Flachdichtungen auch aus Faserstoffen oder PTFE (Polytetrafluorethylen). Für Anwendungen unter hohem Druck kommen daneben metallverstärkte Werkstoffe zum Einsatz. Die Herstellungsverfahren müssen nicht nur die verschiedenen Materialien berücksichtigen. Flachdichtungen für spezielle Anwendungen nehmen daneben sehr individuelle Formen und Dimensionen an.
Die Herstellung herkömmlicher O-Ringe und Flachdichtungen unterscheidet sich grundlegend. Dennoch sind die hohen Anforderungen an Präzision, Wirtschaftlichkeit und kurzfristige Verfügbarkeit beiden Dichtungsarten gemein.
Kundenindividuelle Dichtungen müssen sich in kurzer Zeit herstellen lassen, um teure Maschinenausfälle beim Kunden zu vermeiden.
Für die Herstellung von Elastomeren O-Ringen kommen hauptsächlich zwei Verfahren zum Einsatz: Das Kompressionsverfahren, oder Formpressen (Compression Molding) und das Spritzgussverfahren (Injection Molding).
Das Kompressionsverfahren beginnt mit der Herstellung eines Rohlings im Strangpressverfahren. Dieser wird im nächsten Schritt in eine Form eingelegt und unter hoher Temperatur zu einem kreisförmigen O-Ring gepresst. Nach dem abschließenden Entgraten ist der O-Ring fertig. Das Verfahren eignet sich vor allem für die Herstellung geringerer Stückzahlen von Dichtungen mit großen Abmessungen.
Vorteile Formpressen:
Für O-Ringe in Standardgrößen, die der Markt in einem hohen Volumen nachfragt, eignet sich das Spritzgussverfahren besser.
Hier erhält das Ausgangsmaterial seine endgültige Form durch das automatische Einspritzen in die geschlossene Form. Nach dem Auswerfen ist der O-Ring fertig für Weiterbearbeitung oder Verkauf. Auch hier wirken hohe Temperaturen auf das Material, um die für die elastischen Eigenschaften notwendige Vulkanisation zu erzielen.
Vorteile Spritzgussverfahren:
Besonders große O-Ringe mit gebräuchlichen Schnurlängen von bis zu 3.000 mm verlangen einen weniger automatisierten Herstellungsprozess.
Dies trägt dem meist ungünstigen Verhältnis zwischen Nachfragemenge und den Kosten für die Werkzeugerstellung Rechnung. Am weitesten verbreitet ist das Stoßvulkanisieren von stranggepressten Schnüren. Dabei stellt die Verfügbarkeit der Rundschnur in verschiedenen Durchmessern die einzige Begrenzung der Gestaltungsfreiheit dar.
Zum Stoßvulkanisieren legt der Fachmann die Schnurenden in spezielle Vorrichtungen ein. Dort versieht er sie mit einer Haftmischung.
Nun wirken Temperatur und Druck, um die Stoßstellen zu vulkanisieren, also die Moleküle zu verketten. Das Verfahren hat durch die überlegenen physikalischen Werte der vulkanisierten Stoßstelle das vorher gebräuchliche Verkleben von O-Ringen weitestgehend abgelöst.
Dennoch stellt der Stoß eine Schwachstelle gegenüber der extrudierten Schnur dar. Dem Prozess geschuldet sind auch die im Vergleich zu den anderen Verfahren größeren Fertigungstoleranzen.
Vorteile Stoßvulkanisieren:
Das Ausgangsmaterial für Flachdichtungen stellen in der Regel plattenförmige Halbzeuge dar, die je nach Anwendung aus Elastomeren, Faserwerkstoffen oder auch mehrschichtigen Materialkombinationen bestehen können.
Flachdichtungen in einer Vielzahl von Konturen lassen sich mittels Stanzen, Plotten oder Wasserstrahlschneiden aus den Platten heraustrennen. Die Verfahrensauswahl erfolgt unter den Gesichtspunkten Stückzahl, Lieferzeit und Werkstoff.
Für das Stanzen einer Flachdichtung benötigt der Hersteller ein spezifisches Schneidewerkzeug, das eine hydraulische Presse in das Plattenmaterial drückt. Aufgrund der überschaubaren Werkzeugkosten lassen sich mit dem Stanzen Mittel- bis Großserien auf wirtschaftliche Weise abwickeln.
Bei kundenspezifischen Flachdichtungen stellt die Werkzeugerstellzeit einen Nachteil dar. Auch von technischer Seite besteht eine Einschränkung: Bei Werkstoffen mit einem zelligen und weichen Aufbau kann sich durch das Nachgeben ein konkaves Schnittbild ergeben.
Eine besonders präzise Alternative ist das Wasserstrahlschneiden. Es ist für solche Materialien prädestiniert, bei denen mechanische und thermische Verfahren an ihre Grenzen kommen.
Durch das Zerteilen des Dichtmaterials mit einem Wasserstrahl unter hohem Druck entstehen nicht nur kleinste Geometrien und Bohrungen in engen Toleranzen. Auch weiche Dichtungswerkstoffe lassen sich deformationsfrei verarbeiten. Selbst einfache dreidimensionale Dichtungen kann das Wasserstrahlschneiden erzeugen.
Ein weiterer Vorteil, der das Verfahren vor allem für die Kleinserien- und Einzelproduktion interessant macht: Ein digitales Modell der Flachdichtung reicht aus, um die Befehle für die CNC-gesteuerte Maschine zu erzeugen. Vorausgesetzt, das entsprechende Halbzeug ist verfügbar, kann die Produktion mit erfolgter Datenbereitstellung sofort beginnen.
Bei Materialien mit über 100 mm Höhe beginnt sich die zunehmende Streuung des Wasserstrahls negativ auf die Präzision auszuwirken. Im vorgesehenen Anwendungsbereich kann das Verfahren aber Werkstücke mit sehr dünnen Wandstärken und sauberen Kanten erzeugen.
Das Plotten eignet sich ebenfalls für die Herstellung kleinere bis mittlere Stückzahlen. Hier trennt ein elektronisch gesteuertes oszillierendes Messer die Kontur der Flachdichtung aus dem Halbzeug. Dem Verzicht auf ein spezifisches Werkzeug entsprechend fallen geringe Rüstkosten an. Ein Plus gegenüber dem Wasserstrahlschneiden stellt der Größenbereich dar.
Hier lassen sich je nach Schneidetisch auch sehr große Dichtungen von mehreren Metern Länge herstellen. Das Verfahren eignet sich in Abhängigkeit vom Werkstoff für maximale Materialhöhen bis 10 mm.
Ob eine Dichtung ihre Aufgabe zuverlässig erfüllen kann, das hängt nicht nur von der Materialauswahl und der korrekten Auslegung des Dichtsystems ab, sondern auch von den Herstellungsstandards. Bei allen diesen Fragen beraten Sie die Experten von NH O-RING und stellen so sicher, dass die Dichtung Ihre technischen und wirtschaftlichen Anforderungen erfüllt.
Bei Dichtungen mit spezifischen Geometrien oder Prototypenteilen liegt außerdem ein besonderer Fokus auf der schnellen Verfügbarkeit.
Egal ob Flachdichtungen als Plattenzuschnitt, Profilschnüre, oder Formteile, hier sind kurze Reaktionszeiten gefragt. Wir wählen das optimale Herstellungsverfahren aus, sodass Sie stets die Dichtungen schnellstmöglich geliefert bekommen.
„Ich bin überzeugt davon, dass wir unser Wissen mit der Welt teilen sollten. Ich hoffe, dass ich alle Ihre Fragen beantworten konnte. Sollten Sie noch Fragen haben, dann können Sie sich jederzeit gerne bei uns melden. Wir helfen Ihnen gerne weiter.“
Herr der O-Ringe
Autor der Dichtungsakademie
Die 10 wichtigsten Fragen zur korrekte Auslegung von O-Ring Datenblätter beantworten wir Ihnen in diesem kurzen Beitrag einfach und verständlich.
Die 10 wichtigsten Fragen zur korrekte Auslegung von O-Ring Nuten beantworten wir Ihnen in diesem kurzen Beitrag einfach und verständlich.
Die 10 wichtigsten Fragen zur korrekte Lagerung von O-Ringen beantworten wir Ihnen in diesem kurzen Beitrag einfach und verständlich.
Sie müssen den Inhalt von reCAPTCHA laden, um das Formular abzuschicken. Bitte beachten Sie, dass dabei Daten mit Drittanbietern ausgetauscht werden.
Mehr Informationen