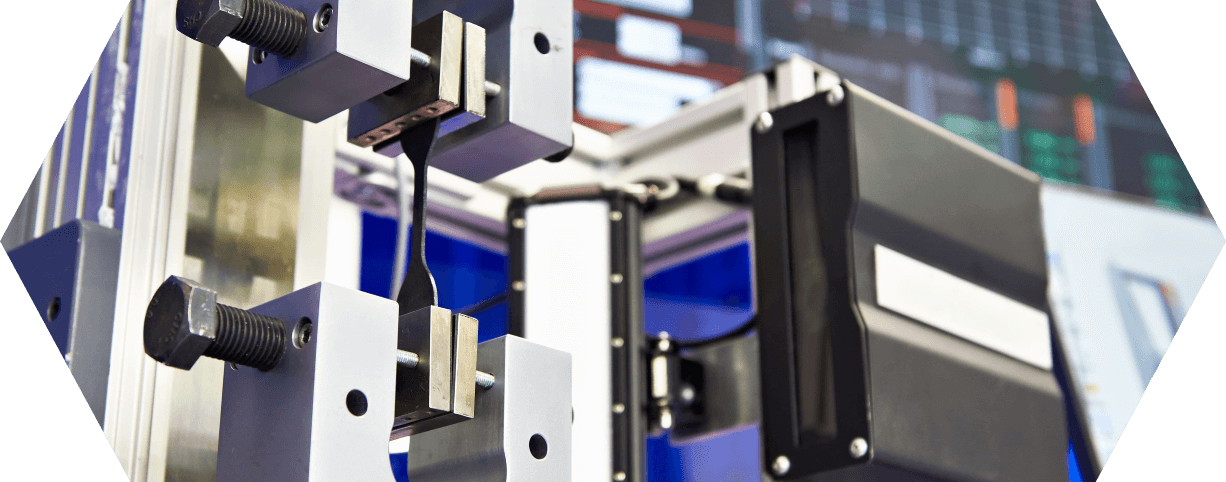
10 Fragen: O-Ring Datenblätter
Die 10 wichtigsten Fragen zur korrekte Auslegung von O-Ring Datenblätter beantworten wir Ihnen in diesem kurzen Beitrag einfach und verständlich.
Durch die Reibung im Kontakt mit härteren Bauteilen lösen sich Partikel aus der Oberfläche von O-Ringen. Sie verlieren also punktuell oder über den gesamten Umfang an Masse. Ist dieser Verschleißmechanismus stark ausgeprägt, kann das schnell zum Versagen der Dichtung führen.
Denn das fehlende Material bedingt Undichtigkeiten. Nun kann sie zwar zu übermäßigem Abrieb führen, doch ganz ausschließen lässt sich die Reibung nicht.
Denn sie ist essenziell für das Herstellen der Dichtungswirkung. Nur indem die Druckverhältnisse den O-Ring gegen die Dichtflächen pressen, kann er neben dem Dichtspalt kleine Unebenheiten in den Bauteiloberflächen verschließen.
Gerade bei dynamischen Anwendungen stellt der Abrieb ein großes Problem für die Haltbarkeit der Dichtung dar. Doch es gibt mehrere Ansatzpunkte für die Verringerung des mechanischen Verschleißes. Auch darauf gehen wir nach der Beschreibung des Schadensbildes und seiner Ursachen ein.
Ist der O-Ring dauerhaft verformt, dann hat er sich an eine statische Position im Dichtungssystem angepasst. Diese ist durch die Verpressung des Querschnitts zwischen den Dichtflächen vorgegeben.
Zusätzlich kann ein Medium wie Kühlwasser oder Hydrauliköl Druck auf das Dichtungselement ausüben. Auch dies bestimmt die Positionierung des O-Rings im Dichtspalt und kann eine weitere Verformung seines Querschnitts hervorrufen.
Bei einer dynamischen Abdichtung kommt mit der Reibung noch eine weitere entscheidende Komponente hinzu. Denn vor allem hierbei entsteht das Schadensbild des übermäßigen Abriebs.
Bei der Schadensanalyse fällt auf, dass der O-Ring gegenüber dem Ausgangszustand deutlich an Masse verloren hat. In der Regel ist die Querschnittsfläche über den gesamten Umfang reduziert.
So lässt sich der Abrieb auch von der bleibenden Verformung abgrenzen. Zwar nehmen die Querschnitte in beiden Fällen ähnliche Formen an, doch die starke Masseabnahme zeigt sich nur beim Abrieb.
Abrieb entsteht durch den Kontakt des O-Rings mit den Dichtflächen, der Effekt kann aber durch abrasive Partikel in den Medien verstärkt werden. Die für die Dichtwirkung notwendige Verpressung sorgt dafür, dass der O-Ring an den Dichtflächen anliegt.
Dichtet er ein druckbeaufschlagtes Medium gegen die Atmosphäre ab, drückt dieses den O-Ring zudem an die druckabgewandte Flanke der Nut. So kann auch bei der Abdichtung eigentlich unbewegter Maschinenteile eine Reibung am O-Ring entstehen.
Bei dynamischen Anwendungen führen die Bauteile dagegen regelmäßig eine Relativbewegung zueinander aus. So ist es etwa bei Kolben und Zylinder.
Hier liegt der O-Ring in einer Nut, die in den Kolben eingestochen ist. Ein Übermaß des Außendurchmessers des O-Rings gegenüber dem Innendurchmesser des Zylinders sorgt für die Verpressung des O-Ring-Querschnitts. Jedes Mal, wenn der Kolben im Zylinder auf und ab gleitet, reibt der O-Ring über die Dichtfläche. Dabei entsteht Wärme, aber auch ein mechanischer Materialabtrag.
Der Materialabtrag betrifft den O-Ring, denn dieser ist naturgemäß weicher als das Material, aus denen Zylinder und Kolben bestehen. Nur so kann er seine Dichtaufgabe wahrnehmen. Diese besteht darin, kleine herstellungs- oder verschleißbedingte Unebenheiten in den metallischen Bauteiloberflächen auszugleichen. Ein Mindestmaß an Reibung ist also stets nötig, um die Dichtwirkung zu erreichen.
Wegen ihrer Oberflächeneigenschaften neigen Elastomere dazu, aneinander und an Maschinenoberflächen zu haften. Sie haben allgemein einen hohen Reibkoeffizienten. Entsteht sehr starker Abrieb am O-Ring, dann ist das in der Regel auf einen Einsatz als dynamische Dichtung zurückzuführen.
Doch bereits bei der Montage kann ein gewisser Materialabtrag durch Abrieb entstehen. Das ist jedoch ein klarer Montagefehler, der durch entsprechende Schulung des technischen Personals zu verhindern ist.
Schuld daran sind wechselnde Druckverhältnisse. Sie lassen den Dichtring über die gesamte Breite der Nut wandern. Ein hoher Abrieb ergibt sich vor allem bei der zyklischen Abfolge extremer Druckbedingungen. Das geschieht trotz des geringen Weges, den der O-Ring in axialer Richtung in der Nut zurücklegt.
O-Ringe als dynamische Dichtung sind am häufigsten von übermäßigem Abrieb betroffen. Hier gleiten sie ständig über die Laufflächen der Bauteile.
Reibungsverluste lassen sich zwar nie ganz vermeiden, doch sie reduzieren die Effizienz eines technischen Systems. Denn ein Teil der eingesetzten Energie geht durch Reibung verloren und wird in Wärme umgewandelt.
Diese kann erstens oft nicht weiterverwertet werden und sorgt zweitens für eine lokale Erhitzung am O-Ring. Das ist genauso unerwünscht, denn die Temperatureinwirkung kann die Materialeigenschaften des O-Rings verändern.
Bei dynamischen Abdichtungen ist besonders auf eine hohe Oberflächengüte der Laufflächen der Dichtung zu achten. Je glatter sie sind, desto weniger Reibung entsteht. Außerdem stellen harte Partikel in den Medien ein Problem dar. Beispielsweise können kleine Metallspäne in Schmieröl die Lauffläche beschädigen und wiederum für mehr Reibung zwischen ihr und der Dichtung sorgen.
Eine weitere Ursache für den erhöhten Abrieb kann eine fehlende Schmierung sein. Laufen die Dichtungen trocken, steigen Reibung und thermische Belastung an.
Das Maß der Verpressung bestimmt über die Reibung mit. Diese kann der Techniker jedoch nur in engen Grenzen reduzieren.
Eine Mindestverpressung muss aufrechterhalten bleiben, damit der O-Ring genug Reserven für eine elastische Rückverformung hat. Gerade bei dynamischen Abdichtungen liegt die Verpressung bereits am unteren Limit, um Reibungsverluste im Rahmen zu halten.
Vielversprechender ist es da, höhere Oberflächengüten für die Laufflächen der Dichtung zu spezifizieren. Schleifen und Polieren oder das Verchromen der Bauteile sind Verfahren, die die Reibung deutlich reduzieren können.
Eine Senkung des Reibungskoeffizienten der O-Ring-Oberfläche ist dazu geeignet, Abrieb zu verhindern. Dies kann durch die geeignete Werkstoffauswahl und zusätzliche Beschichtungen erreicht werden. Die Hersteller mischen den O-Ring-Werkstoffen Füllstoffe und Weichmacher bei, die die Reibungseigenschaften mitbestimmen. Doch bereits die Basispolymere unterscheiden sich in ihrer Abriebbeständigkeit.
Beispielsweise ist diese bei Silikon so gering ausgeprägt, dass hier generell von einem dynamischen Einsatz abgesehen werden sollte. Der Werkstoff NBR eignet sich ebenso wie Silikon für Lebensmittelanwendungen, ist jedoch deutlich abriebfester.
Der Markt bietet verschiedene Verfahren zur Oberflächenbehandlung von Elastomeren an. Die Senkung des Reibungskoeffizienten verbessert die Gleiteigenschaften des O-Rings. Das ist nicht nur für den späteren Einsatz im Dichtungssystem relevant. Auch die voll- oder teilautomatisierte Montage von O-Ringe profitiert davon. Denn haften die Dichtungen nicht aufeinander, können sie besser vereinzelt werden.
Hier geht es jedoch um Beschichtungen für den dynamischen Einsatz und nicht um solche, die in erster Linie der Montageerleichterung dienen.
Moderne Beschichtungsverfahren überziehen O-Ringe und Formdichtungen mit einer Gleitlackschicht im Nanobereich. Das zusätzliche Material beeinflusst die Materialeigenschaften des O-Rings dadurch nur sehr gering. Die Kernmaterialien EPDM, NBR, HNBR oder Silikon können also weiterhin ihre individuellen Stärken ausspielen.
Jedoch ist zu beachten, dass die Beschichtung stabil gegenüber den Einflüssen im Betrieb sein muss. Dazu gehört etwa die Sterilisation mit heißem Dampf oder der Kontakt mit Säuren und Laugen. Als Werkstoff für den Gleitlack kommen beispielsweise PTFE oder Polysiloxan zum Einsatz.
Auch hier sind die Ingenieure gefordert, aus der Vielzahl an Lösungen mit den jeweiligen Anforderungen konforme Beschichtungssysteme auszuwählen. Bei uns erhalten sie dabei fachkundige Unterstützung. Denn unsere Anwendungsexperten kennen die technischen Möglichkeiten genauso wie industriespezifische Anforderungen. So können sie die bestgeeignete Alternative identifizieren.
„Ich bin überzeugt davon, dass wir unser Wissen mit der Welt teilen sollten. Ich hoffe, dass ich alle Ihre Fragen beantworten konnte. Sollten Sie noch Fragen haben, dann können Sie sich jederzeit gerne bei uns melden. Wir helfen Ihnen gerne weiter.“
Herr der O-Ringe
Autor der Dichtungsakademie
Die 10 wichtigsten Fragen zur korrekte Auslegung von O-Ring Datenblätter beantworten wir Ihnen in diesem kurzen Beitrag einfach und verständlich.
Die 10 wichtigsten Fragen zur korrekte Auslegung von O-Ring Nuten beantworten wir Ihnen in diesem kurzen Beitrag einfach und verständlich.
Die 10 wichtigsten Fragen zur korrekte Lagerung von O-Ringen beantworten wir Ihnen in diesem kurzen Beitrag einfach und verständlich.
Sie müssen den Inhalt von reCAPTCHA laden, um das Formular abzuschicken. Bitte beachten Sie, dass dabei Daten mit Drittanbietern ausgetauscht werden.
Mehr Informationen